Make some changes to the world environment
-
Building 3, Wanyang Innovation City, Langxia Street, Yuyao City, Zhejiang Province
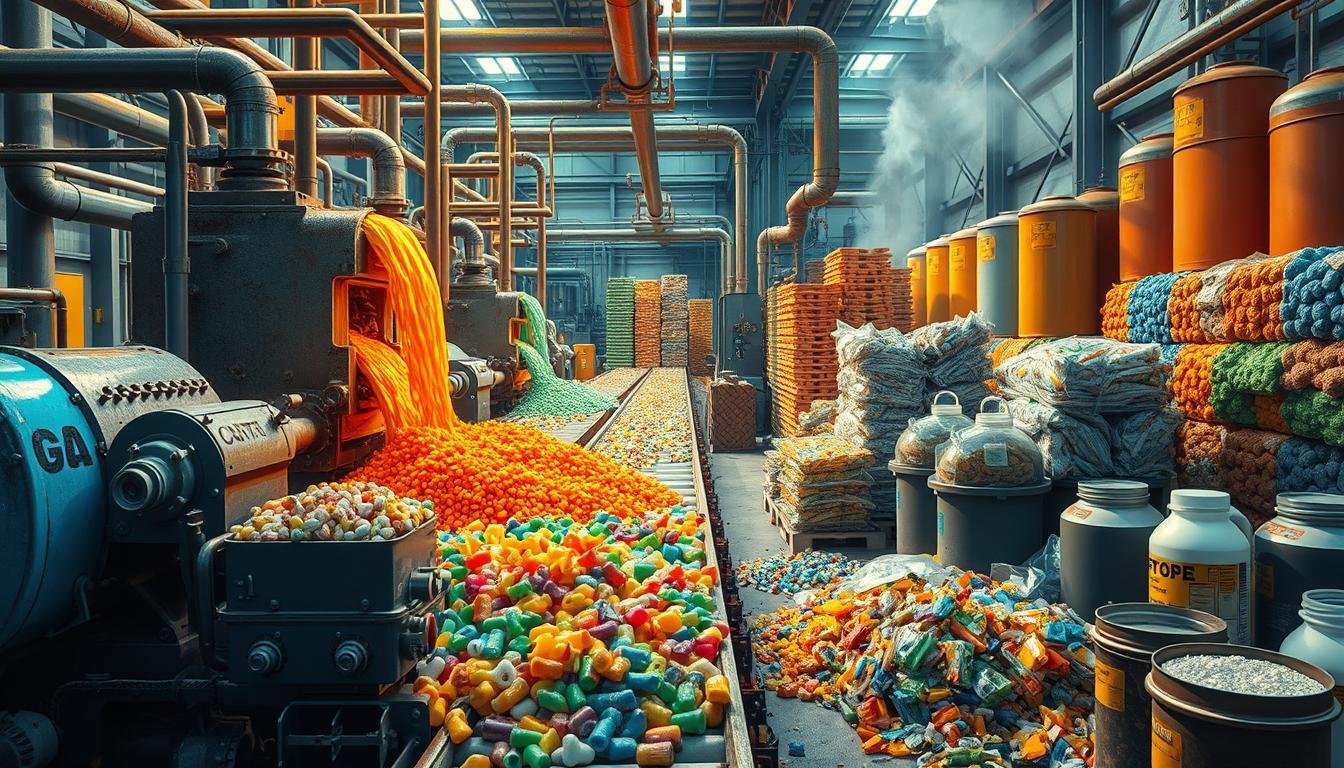
A Guide to How Plastic Materials Are Made
Have you ever wondered about the plastic manufacturing process? How are plastic materials made? Plastic products are a big part of our everyday lives and industrial uses. It’s important to know how they’re produced. Let’s explore the journey from raw materials to the final product. We’ll uncover the innovations and techniques behind modern plastic manufacturing.
Key Takeaways
- Thermoplastics can be recycled and reused multiple times without significant degradation1.
- Common additives in plastics enhance properties like color, strength, and heat resistance1.
- Synthetic plastics are made from coal, crude oil, or natural gas. Biobased plastics come from plants like starch and corn2.
- Polymerization is the chemical reaction that makes plastic polymers from smaller molecules like ethylene and propylene2.
- Polyethylene Terephthalate (PET) is the most produced synthetic plastic. It’s popular for its recyclability and toughness3.
We aim to give a deep understanding of how plastic is made. We also want to highlight the key parts of the plastic manufacturing process. These drive efficiency and spark creativity in the industry. Join us as we dive into the world of plastic making. Here, science blends with creativity, and innovation leads the way.
An Overview of Plastic Materials
Plastic materials have changed many industries with their flexible use and wide applications. They are mainly made from stuff like cellulose, coal, natural gas, salt, and crude oil. These materials are crucial in today’s world4. Starting in 1862 with the first synthetic plastic, their development has a long history. Now, we are aiming to make plastics more sustainable by using waste or renewable materials4.
Plastics can be recycled by breaking them down into new products or turned back into basic materials. This process helps recycle over 10 million tonnes of plastics in the EU by 20254. Knowing how plastics are made, from getting raw materials to shaping them, is key to making good plastics.
Plastics are sorted into types like acrylics, polyurethanes, and silicones based on their makeup5. They’re further grouped by how they’re made and how they react to things. There are plastics that melt with heat, and others that stay solid5. Adding different things to plastics can change their color, hardness, and resistance to bacteria or fire.
Plastics are used in many areas like health, farming, and construction. They help make things like saving energy and lowering fuel use possible4. As we find new ways to make and use plastics, they will keep playing a big part in making things better and more sustainable.
To learn more about how plastic is made, check out this detailed guide on plastic extruders. It covers how they work, what makes them efficient, and how they’re designed4.
Types of Plastic: Synthetic vs Biobased
When making plastic products, it’s key to know the difference between synthetic plastics and biobased ones. Synthetic plastics come from petrochemicals. Biobased plastics, however, come from things that grow.
Synthetic Plastics
Synthetic plastics need fossil fuels like crude oil, natural gas, and coal6. These fuels are taken out of the ground and refined to make important compounds. One key compound is naphtha, used to make many synthetic plastics. In Europe, only about 4 – 6% of oil and gas are used for plastics. The rest goes to transportation, electricity, and heating6.
Common synthetic plastics include:
- Polyethylene (PE): This plastic comes in types like HDPE and LDPE. HDPE is for things like pipes and plastic lumber. LDPE is for bags and bottles7.
- Polypropylene (PP): PP is tough and can take the heat. It’s used in cars, electrical stuff, and medical devices7.
- Polyvinyl Chloride (PVC): PVC comes in hard and soft types. Hard uPVC is good for construction, like pipes and windows. Soft PVC is used in cables and medical gear7.
- Polystyrene (PS): PS makes stuff like disposable forks and packaging. It’s chosen for its stiffness and ability to be shaped7.
Synthetic plastics are popular for their easy making and use in many fields6. Yet, they really add to climate change. They’re the third biggest petroleum product used around the world8.
Biobased Plastics
With worries about synthetic plastics, more people want biobased plastic choices. These come from renewable things like carbs, starch, and oils6.
Biobased plastics include:
- Polylactic Acid (PLA): Mostly made from corn, PLA can break down naturally. It is often used for packaging and can be composted industrially8.
- Biodegradable Plastics: These are made from plants like corn or sugarcane. They’re getting better and might help solve some environmental issues7.
Bioplastics were just 0.2% of the polymer market in 2014, but they’re growing8. These biodegradable plastics work like the usual ones but are less harmful. They help us rely less on limited oil resources6.
Understanding Polymer Chemistry
In polymer chemistry, we look at how certain materials change industries. Polymers have different sizes and weights that make them useful every day9. Knowing about polymers helps us create new stuff in factories.
People started using man-made polymers a lot in the early 1900s9. But, natural polymers like wool and wood have been around since the old days. This shows we’ve always needed them9. Now, we know a lot about polymers such as polyethylene, which is useful for many things9.
About 80% of plastics we use are thermoplastics, and 20% are thermosets10. Thermoplastics, like polypropylene and polystyrene, are popular because we can melt and shape them again1011. Thermosets get hard and can’t be reshaped, which makes them less common for some uses9.
We use special methods to make polymers fit for certain uses9. For example, in making cars, polymers help make parts like headlights and bumpers strong but light11.
Lately, there’s a lot of work with biodegradable and smart polymers. This has led to new materials like polylactic acid, which are stronger and can stand more heat11. These materials are really important for space and high-tech gadgets, showing how crucial polymer study is today.
Polymers are also key in making packages because materials like polyethylene are light, strong, and don’t cost much11. Knowing how these materials work helps makers build better products. If you want to learn more, you can check out polypropylene plastic uses and applications9.
Raw Materials in Plastic Production
It’s important to know where plastic materials come from if you’re in the plastics field. These materials mainly stem from oil and natural gas. They also have different fillers and additives to improve the final product.
Petroleum and Natural Gas
Petroleum is the key ingredient for making plastics. It comes from the remains of ancient animals and plants that were pressed under the earth for millions of years. Almost all plastics are from materials found in fossil fuels. Polyethylene is the most common plastic used for packaging today12. The processing of natural gas liquids, like ethane, creates various polymers. These polymers are crucial for making polyethylene13.
Common resins for plastic goods include polyethylene (PE), PET, PP, PVC, and PS. In the US, each person is tied to about 150 kilograms of polymers per year. This shows how much we depend on plastics made from petroleum13.
Fillers and Additives
Fillers are key in making better and more cost-effective plastic products. Calcium carbonate, for example, helps improve the strength, durability, and heat resistance of these products. Also, more eco-friendly materials like cellulose from softwood trees and sugar cane are being explored to lower environmental harm12.
Many things affect the use of fillers and additives, like the quality of the materials, transport costs, and the world market. Innovations, such as PBTL, a new type of recyclable polymer, show efforts to be more sustainable. These efforts aim to lessen the environmental effects seen with traditional materials13.
Now, let’s look at a comparison of different polymers and how they’re used:
Polymer | Application | Common Uses |
---|---|---|
Polyethylene (PE) | Wide-ranging | Bags, wire insulation, squeeze bottles |
Polypropylene (PP) | High versatility | Fibers, indoor-outdoor carpets, bottles |
Polystyrene (PS) | Insulation | Styrofoam products |
Polyvinyl chloride (PVC) | Durable | Food wrap, bottles, synthetic leather |
Polytetrafluoroethylene (PTFE) | Nonstick | Teflon, nonstick surfaces |
With these different uses and by carefully choosing fillers and additives, the plastic industry is making progress. It’s working on better performance, lowering costs, and taking care of the planet.
Key Steps in the Plastic Manufacturing Process
To create high-quality plastic products, it’s important to know the process from start to finish. This guide covers the essential steps from getting raw materials to the advanced polymerization techniques used.
Extraction of Raw Materials
The making of plastic starts by getting hydrocarbons from coal, natural gas, and petroleum14. These are the main materials used in making plastic14.
Refining and Processing
After getting the hydrocarbons, they’re refined to turn into monomers. Monomers are the starting point for polymers. Types of plastics like polyethylene and polypropylene come from a method called addition polymerization. Nylon and polyester come from condensation polymerization14. Polymers get improved by adding things like stabilizers and flame retardants14.
Polymerization Methods
Polymerization is key for changing monomers into polymers. It happens in two main ways: addition and condensation. There are tons of plastics made this way, including powders and liquid resins. These are then shaped for different purposes15. Methods like addition and condensation create plastics with unique traits for various needs14.
Molding processes give polymers their final shape. Techniques include rotational, blow molding, extrusion, and injection molding14. Injection molding is super important for making lots of precise parts. It works in fields like electronics and cars by melting pellets into molds1514. This method is great for making detailed and accurate components quickly14.
If you want to learn more about how plastic is molded and made, check out the ultimate guide to PVC plastic recycling. It has lots of info on the methods and tech in the plastic industry today15.
How Plastic Materials Are Made
Making plastic involves several key steps that change raw materials into useful plastic items. We need a deep understanding of these steps to create top-quality plastics for different uses.
Polymer Compounding
The first important step in making plastic is called polymer compounding. Here, base polymers are mixed with things like stabilizers and colorants. These mixes help make the plastic strong, flexible, or colored. Then, the mix gets heated and turned into pellets. These pellets are used later in the process.
Molding and Shaping
Next, the pellets are molded and shaped. The method used depends on what the final product will be. Some common methods are:
- Injection Molding: Polymer is pushed into a mold to get precise shapes.
- Blow Molding: Soft plastic is blown up like a balloon inside a mold, great for making bottles.
- Extrusion: Polymer is squeezed through a die to make long shapes, like pipes.
- Rotational Molding: A mold spins around, filling with polymer to make big, hollow items.
Creating a one liter PET bottle uses about two liters of water and a lot of energy16. Every year, we make over 300 million tons of plastic. Sadly, half is only used once17.
Post-Processing Techniques
After shaping, we refine and finish the products. Trimming, painting, and putting parts together are some ways we improve the products. These steps help meet the high-quality standards needed for their use.
Being eco-friendly is key in making plastics today. Using recycled plastics for PET bottles uses less energy and resources16. Also, using recycled plastic means we can skip some steps, saving more resources16.
Different Plastic Forming Methods
The plastic industry uses many forming methods to make a wide range of products. Each method fits certain plastics and uses, making things work better and more affordably. Knowing these methods helps choose the right one for what you’re making.
Injection Molding
Injection molding is a top choice because it’s accurate and efficient. In this method, hot plastic is injected into a mold to take shape. Over 80% of everyday plastic items, like toys, car parts, and household goods, are made this way18. Materials like ABS and PMMA are favorites for this method. They can be melted and reshaped many times without losing quality19.
Blow Molding
Blow molding is key for making hollow plastic items. It blows hot plastic into a mold to create shapes like bottles and cups. This method is great for making things like disposable bottles and cups from clear, tough materials like PET18. It’s chosen for its cost-effectiveness in making lots of thin-walled, light products.
Extrusion
Extrusion presses molten plastic through a die to form long, continuous shapes. This method fits high-quantity making really well. Thermoplastics, which melt easily, are typically used here19. Its uses reach from building to packaging, making it very adaptable.
Rotational Molding
This method is unique, perfect for big, hollow shapes like tanks or tubs18. It heats and rotates powdered plastic inside a mold for an even spread. This way, it makes strong, lasting items with great structure.
Forming Method | Application | Materials Used |
---|---|---|
Injection Molding | Household items, automotive components | ABS, PMMA, PA |
Blow Molding | Bottles, containers, disposable cups | PET, PEEK |
Extrusion | Pipes, sheets, films | Thermoplastics (pellets or sheets) |
Rotational Molding | Canoes, tubs, water storage tanks | Various plastic powders |
Modern Advancements in Plastic Production
Modern advancements in plastic production are deeply influenced by innovations in plastic manufacturing and the increasing demand for sustainable plastic production technologies. Synthetic polymers were first invented in 1869 by John Wesley Hyatt to substitute natural substances like ivory, opening a new era in material availability20. Since then, plastic production has evolved significantly, especially during and after World War II, when the United States saw a 300% increase in plastic production to support the war effort20. This demonstrates how critical innovations in plastic manufacturing have been through history.
Today, global plastic production exceeds 450 million tonnes annually, showcasing a sharp increase in the last 70 years from just 2 million tonnes in 195021. This tremendous growth is driven by continuous innovations in plastic manufacturing. Worldwide, over 360 Mt of fossil-based polymers are produced each year, reflecting an annual growth rate of 8.4%, which is double the global growth rate of production22. This boom highlights the role of plastic in modern life and the increasing need for sustainable plastic production technologies to curb environmental impact.
Amid growing environmental concerns, the industry is actively developing sustainable plastic production technologies. In 2018, the European plastic converter demand reached 51.2 Mt, predominantly for packaging, construction, automotive vehicles, and electronic devices22. Additionally, the EU’s total production capacity of biopolymers is projected to hit 2.45 Mt by 202422. Such milestones underscore the industry’s shift towards sustainable practices.
Effective recycling also plays a pivotal role in making plastic production more sustainable. For instance, 32.5% of recycled post-consumer plastic waste in 2018 was repurposed22, and bioplastics made from plant crops are gaining prominence as eco-friendly alternatives20. Nevertheless, only 9% of the world’s plastic waste is recycled, while a significant portion ends up in landfills or oceans, illuminating the need for improved waste management solutions21.
Sustainable plastic production technologies and better waste management practices are vital to reducing plastic pollution. Each year, 1-2 million tonnes of plastic waste make their way into the oceans, contributing to significant environmental challenges21. To counter this, best practices in plastic manufacturing and recycling must be adopted globally, ensuring that plastics can be part of a sustainable future.
Conclusion
Understanding how plastics are made and recycled matters to us. We strive to make better recycling machines. The process from starting with basic materials to making plastics is complex. It involves many steps, like turning raw stuff into polymers and then into products.
Plastics play many roles and come from different sources. Some are man-made, while others come from plants. This variety makes the plastic market rich and always changing. We keep finding new ways to make and use plastics.
Right now, we’re not doing great with plastic waste. Only 9% gets recycled, 12% is burned, and 79% ends up in dumps or nature23. If we don’t change, we’ll make over 1.1 billion tons of plastic a year by 205024. Plus, tiny plastic bits and harmful chemicals are bad for our health25.
We’re serious about making less waste and recycling more. The future of plastics needs us to make, recycle, and manage waste better. We’re here to change how things are done, aiming for less pollution and harm. Our team across the world is ready to help industries with these big problems.