Make some changes to the world environment
-
Building 3, Wanyang Innovation City, Langxia Street, Yuyao City, Zhejiang Province
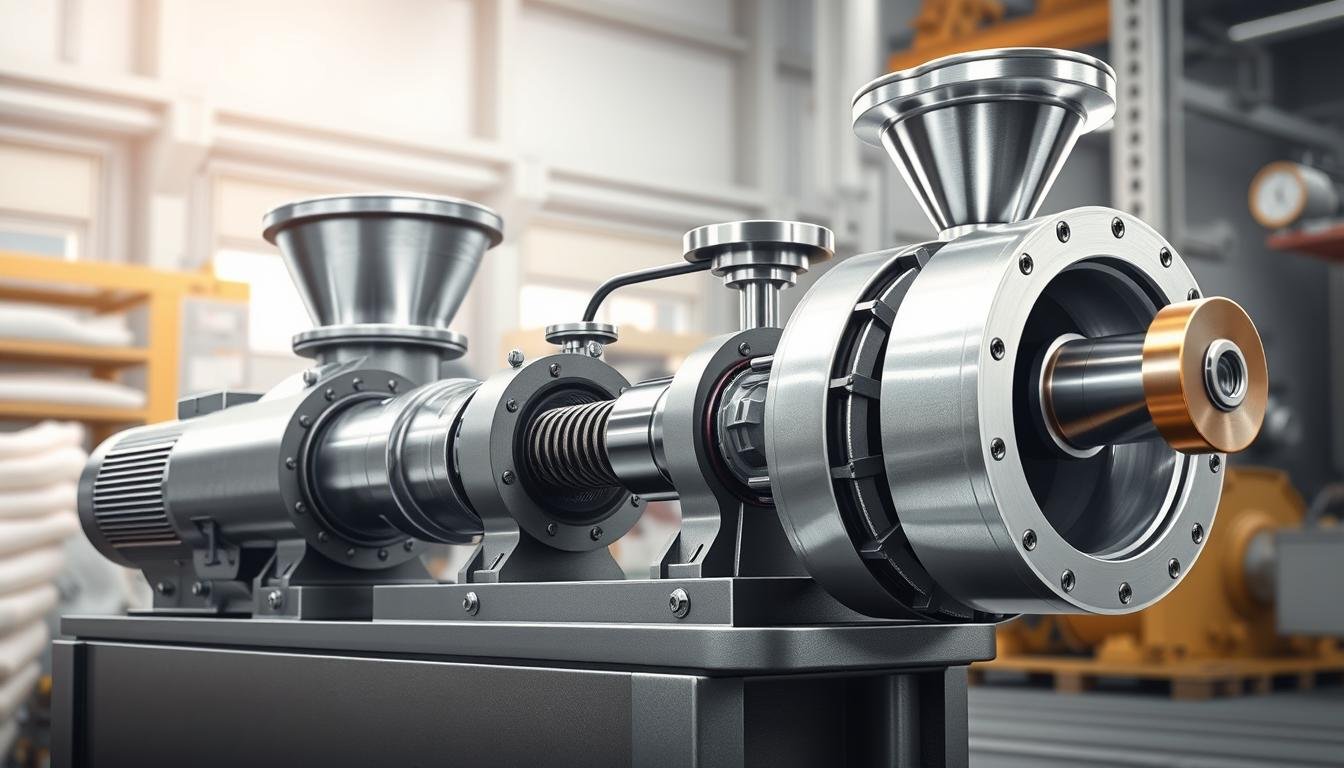
Comprehensive Guide to Single Screw Plastic Extruders
Single screw plastic extruders are essential in the world of plastic machinery. They transform and create polymer products. Through converting rotational energy, they open new doors in manufacturing. We view these extruders as key for making many items, from pipes to sheets.
This guide will explain their engineering and how they work. Understanding these aspects shows why they’re so important in the plastics industry. Let’s explore how they optimize making products and lead to excellence in manufacturing.
Key Takeaways
- Single screw extruders are foundational in manufacturing a variety of plastic products.
- Expertise in polymer extrusion technology is crucial for effective single screw extrusion.
- Optimization of single screw extruders can lead to remarkable efficiency and production quality.
- Understanding the role and mechanics of plastic extruders enhances strategic operation.
- Investment in precise plastic processing machinery amplifies productivity and profitability.
- Global trends in extrusion highlight a shift towards energy efficiency and high performance.
Understanding Single Screw Plastic Extruders
Single screw extrusion technology combines mechanics and heat. It’s about how the machine works, moves materials, and uses screw designs. These details help us understand better how these machines melt polymers with shear stress.
Basic Principles of Single Screw Extrusion
Single screw extruders turn solid polymer bits into even melts. This depends on the screw design. It manages polymer melting by balancing stress and heat. The screw’s rotation creates heat from friction. This heat must be spread out evenly.
The Role of the Screw in Polymer Melting
The screw does more than just push materials. It’s key in melting polymers. Its design, with changes in depth and pitch, makes for controlled melting. This design helps avoid overheating and material damage. So, it keeps materials moving well.
How Material is Conveyed Through the Extruder
How material moves through an extruder depends on the screw design and internal pressure. The screw’s depth and pitch ensure materials move smoothly. This smooth flow is vital for regular product results. The screw and barrel’s design must work together to avoid material blockages.
We’ve looked into single screw plastic extruders. We see how vital exact screw design and the balance of heat and forces are. Knowing this helps make the extrusion process better. It improves product quality, which is key for high-quality plastic recycling machinery solutions.
Essential Components of a Single Screw Plastic Extruder
To truly grasp how single screw plastic extruders work, we need to look at their main parts. The journey begins with an effective feeding system. It’s where the plastic pellets start their journey from the hopper to the screw and barrel. This system controls how fast the pellets move, setting the production pace.
At the core of the extruder is the main motor. It powers the screw with help from a well-aligned gearbox. The gearbox adjusts the motor’s speed and power to meet the extrusion needs. Its reliability and accuracy are key to the extruder’s performance and long life.
The screw and barrel are vital for the melting, mixing, and moving of plastic. They’re made from strong steel and treated to resist wear. This is crucial as they face high temperatures and pressure.
Next, the screen changer is critical. It removes any impurities in the molten plastic, ensuring high-quality products. This device lets operators replace screens without stopping the machine, important for non-stop operation.
The electric control cabinet is the brain of the operation. It allows for precise adjustments in temperature and speed. With this control, the machinery works safely and accurately within set limits.
The machine base is the foundation that holds everything. It’s built to support the heavy, vibrating machine, ensuring everything runs smoothly and lasts longer.
We see the value in each component for the best performance of single screw plastic extruders. These parts work together to make the extruder efficient, whether for simple or complex products. This harmony is crucial for meeting various industrial needs.
Single Screw Plastic Extruder: Operational Mechanics
Our company focuses on improving operational mechanics of single screw plastic extruders. This is crucial for today’s fast-paced industries. The feeding process has been fine-tuned for accuracy, ensuring materials are fed consistently. This is essential for creating uniform products.
The Feeding Process and Material Introduction
The feeding process in a single screw extruder is complex. It requires careful control to keep material flowing smoothly. We use advanced sensors and control systems. These tools help adjust the feed rate on the spot, avoiding any issues.
Mechanics Behind the Melting Process
The melting mechanics in our extruders focus on efficiency and maintaining material quality. Heat and the screw’s actions melt polymer pellets evenly. This step is key in producing top-quality products.
Shear Stress and Polymer Flow Dynamics
Managing shear stress is crucial in our extrusion process. Too much shear stress harms the polymer, and too little causes mixing issues. Our screw designs find the perfect balance. This ensures materials flow well through the die.
We realize our single screw extruders must meet various industry needs, including efficiency and maintenance costs. That’s why we’re dedicated to enhancing the whole process, from feeding to melting. This approach supports both sustainability and efficiency.
Table
Criteria | Single Screw Extruder | Twin Screw Extruder |
---|---|---|
Complexity | Lower | Higher |
Cost | Cost-effective | Higher initial investment |
Operation | Easier to operate and maintain | Complex controls |
Material Processing | Good for steady flow rates | Superior mixing and shearing |
Throughput | Suitable for lower outputs | Higher outputs possible |
In the end, comparing the two shows twin screw extruders have their strengths, like better mixing. However, single screw extruders excel in consistent performance and keeping costs down. We aim to keep refining these machines. This way, they remain essential in various fields, offering custom, innovative extrusion solutions.
In-depth Analysis of the Screw and Barrel Design
To truly understand screw and barrel design in single screw extruders, it’s key to grasp how they’re essential. They play a big role in polymer melting efficiency and in making the extruder work best. The screw shape and the inside of the barrel affect how the polymer is heated and shaped. This affects the quality and type of the final product.
Important parts of the design are channel depths, space between flights, and special parts like mixing pins. These parts help control pressure and how well the plastic is mixed. Changes in design can change how fast the plastic melts. This also changes how much energy is used.
Paying attention to screw and barrel design is also about safety. These machines work under a lot of pressure. A good design means less chance for failures that could cause accidents.
Screw Design | Function | Impact |
---|---|---|
High L/D ratio | Increases the contact area between the polymer and the screw | Improves heat transfer and mixing |
Compression zone | Reduces screw channel volume gradually | Increases pressure and heat, aiding in efficient polymer melting |
Tight clearance | Prevents backflow and maintains forward flow | Enhances product consistency and quality |
Thermally conductive materials | Enhances the transfer of heat from the barrel | Addresses conductive heating challenges, preventing material degradation |
Variable pitch | Alters shear rates and mixing intensity | Adaptable for different polymer types and melting characteristics |
Digging deeper into extruder optimization, changing the screw design matters a lot. Adding mixing sections and special flights is key. These changes help save energy and make the melted plastic more uniform. This leads to high-quality products that meet strict standards.
The continuous improvements in screw and barrel design show our drive for better and innovative methods in the polymer extrusion field. By focusing on these parts, we boost machine performance and safety. Plus, we make sure we can keep up with our clients’ changing needs.
The Science of Melting Polymers in Single Screw Extruders
In a single screw extruder, polymer science and mechanical engineering come together. It’s where resin transforms into something we can use, thanks to thermal energy conversion and the screw’s movement.
As the screw turns, it creates shear-induced heating. This heat changes polymers from solid to liquid. It shows how managing energy carefully is key within the extruder.
About 80% of melting happens at the barrel side. It’s why the barrel’s design is so important for heat transfer. The internal surface of the barrel directly affects how well and evenly the polymer melts.
Melting flux lets us know if our extruders are working right. It measures the melting capacity in kg/(hr m²).
Sometimes, at high speeds, solid bits of polymer don’t melt completely. These bits mean the screw might be going too fast. Or, that we need a better screw design.
- Optimal screw design includes special features for melting and mixing better.
- With polymer melt flows, advanced models improve our designs. They help avoid solid bits in the final product.
Learning more about how polymers move and melt helps us improve. This keeps pushing the tech of single screw extruders forward.
Speed (RPM) | Occurrence of Solid Fragments | Melting Flux (kg/(hr m²)) |
---|---|---|
70 | Increased | Data Not Available |
Below 70 | Decreased | Data Not Available |
Over 70 | Significantly Increased | Data Not Available |
Studying thermal energy conversion and flow dynamics leads to fewer defects. It means better and more reliable plastic extrusion machines. Our focus is on innovation and quality in polymer science.
Optimizing Single Screw Extruder Performance
Our firm understands how crucial it is to manage settings precisely for better extruder performance. We’ve learned through experience that careful adjustments in material handling, flow, and energy can boost single screw extruders. These changes improve their function and efficiency.
Material Considerations for Consistent Results
To get consistent materials, knowing how barrel temperature and screw settings affect the process is key. Setting barrel temperatures at about 165°C for moving solids and screw surfaces between 50°C and 80°C makes materials like HIPS resin move well without slowing down too much. Paying close attention to these temperature settings helps keep material consistency, which is vital for top-notch extrusion results.
Adjustments for Improved Material Flow and Mixing
Changing flow is essential for extruders to work well. For example, lowering barrel-zone temperatures by 10°C can drop discharge temperatures by 2 to 3°C, improving material flow and avoiding issues like surging or unmelted polymers. Also, tweaking screw channel depths based on extrudate temperature and melting capability can significantly enhance material throughput and quality of mixing.
Energy Transfer from Drive to Polymer
Moving energy efficiently from the drive to the polymer is key for cost-effective extrusion. We aim to perfectly match drive energy with operation needs, cutting down on extra energy use while boosting output rates. For instance, changing screw speed to suit metering-channel depth alterations helps keep a steady throughput, optimizing energy use.
By focusing on these strategies, we not only keep our extruders running at their best but also lead to new advancements in single screw extruder technology. We are committed to excellence and driving progress in the field.
Applications and Versatility of Single Screw Plastic Extruders
Single screw plastic extruders handle many applications, proving their versatility in different fields. They support plastic films production, pipe extrusion, and sheet manufacturing. This shows their flexibility and cost-saving benefits. They are key in both packaging and construction. Their role in profile extrusion and granulation shows they make functional and structural parts.
These machines are easy to operate and maintain. This makes them popular in fields like food and medical tubing. They can process many materials, from polyethylene to advanced polymers. This proves their ability to adapt and innovate in various applications.
Industry | Application | Materials Processed |
---|---|---|
Packaging | Film and Sheet Production | Polyethylene, Polypropylene |
Construction | Pipe and Profile Extrusion | PVC, HDPE |
Medical | Tubing | Flexible Polyvinyl Chloride |
Recycling | Granulation | Manufacturing Waste |
The Mosaic+ controller system by Milacron boosts these extruders’ performance. It offers faster speeds and better control. This is vital for achieving specific material properties in special uses.
The above table shows how these machines serve many sectors. They make everything from thin films for packaging to strong pipes for construction. Thus, single screw extruders are crucial in the world of plastic processing technology.
Advanced Design Innovations for Single Screw Extruders
Our team leads the way in plastic extrusion technology. We aim to develop single screw extruders that go beyond what the industry expects. With a focus on design innovations like enhanced mixing, polymer adaptation, and extruder customizations, we have made big strides. These improvements let us process many types of polymers effectively, offering clients the best and most fitting solutions.
Enhancements for Better Mixing and Uniformity
Our latest models boost the quality and uniformity of extruded products. They have new screw designs and barrel setups. These changes lead to better mixing, which is key for uniform products over long production periods.
Adapting to Various Polymer Types
We know that different polymers pose different challenges. That’s why our extruders can easily switch to handle various materials, from HDPE to PP and recycled PET. They are built to manage the specific needs of each polymer, like temperature sensitivity and viscosity.
Customization for Specific End-Products
We understand that different fields need extruders to do specific things. So, our extruders can be customized to meet unique demands, such as throughput rate, melt quality, and efficiency. This means our equipment can be finely tuned for making anything from construction profiles to packaging materials and advanced composites.
Parameter | Standard Model | Customized Model |
---|---|---|
Barrel Length-to-Diameter Ratio | 24:1 | Variable |
Hopper Capacity (kg) | 50 – 500 | Up to several tons |
Operating Temperature (°C) | 180 – 300 | Adjustable |
Cooling Length (meters) | 2 – 20 | Customizable |
Throughput Rates (kg/h) | Standard Rates | 35 – 2000 (MRS Extruder PET Rates) |
Energy Efficiency Improvement (%) | 15 – 25 |
Our single screw extruders stand out because of their innovative design features. They offer better performance and are reliable over time. By constantly innovating and adapting, we aim to push the plastic recycling machinery industry ahead. Our goal is to deliver top-notch solutions to clients around the world.
Conclusion
This guide has shown us how single screw extruders are key in plastic processing. These machines are vital in many industries. They are used in making films to granulating materials. Their efficiency and high production rates make them essential for top-quality manufacturing.
Single screw extruders are cost-friendly and easy to use and maintain. This makes them great for small and medium businesses. The importance of screw speed and temperature in processing polymers like PLA was also discussed. These extruders can handle over 140,000 tons of PLA each year. They combine great design with material science, pushing plastic manufacturing forward.
We have seen the huge impact these machines have on the plastic industry. They lead to better production methods and higher quality. Our goal is to give our clients the tools and knowledge they need for single screw extrusion. This ensures they reach the highest manufacturing standards.