Make some changes to the world environment
-
Building 3, Wanyang Innovation City, Langxia Street, Yuyao City, Zhejiang Province
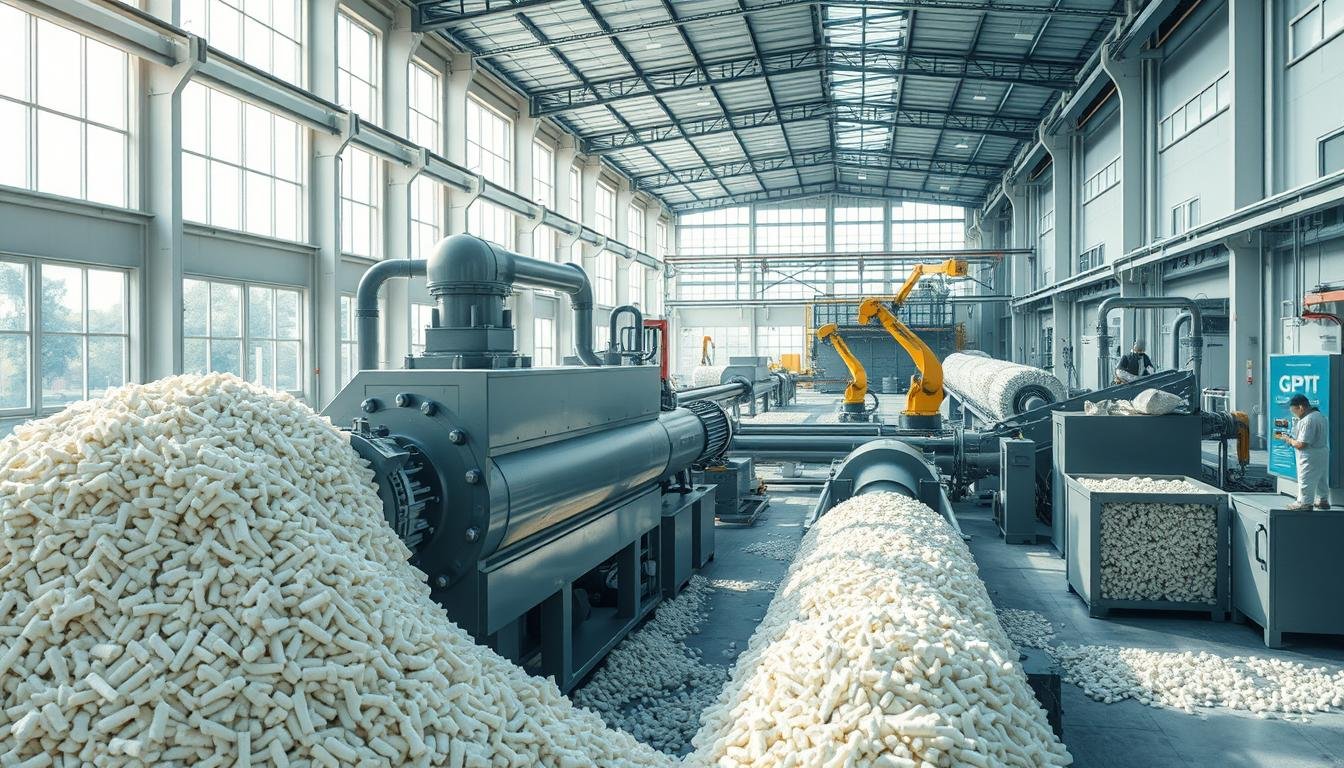
The Definitive Guide to Plastic Recycling Machines
In 2025, plastic recycling machines will be extensively used to transform plastic waste into reusable raw materials like pellets, flakes, or 3D printing filaments for new products; enable localized recycling to cut transportation costs and emissions; produce construction materials such as bricks or composites; convert non-recyclable plastics into fuel or energy via pyrolysis; leverage AI for efficient plastic sorting; and process ocean microplastics to reduce environmental pollution. These technologies will drive a circular economy, reduce landfill use, and effectively tackle global plastic pollution.
What is a plastic recycling machine?
A plastic recycling machine is equipment designed to process plastic waste into reusable materials. It typically includes components like shredders, extruders, and pelletizers that clean, melt, and reshape plastics into pellets or other forms for manufacturing new products. These machines vary in scale, from small units for community use to large industrial systems, and can handle different types of plastics, such as PET, HDPE, or PP, depending on their design. They help reduce plastic waste and promote a circular economy by enabling the reuse of materials.
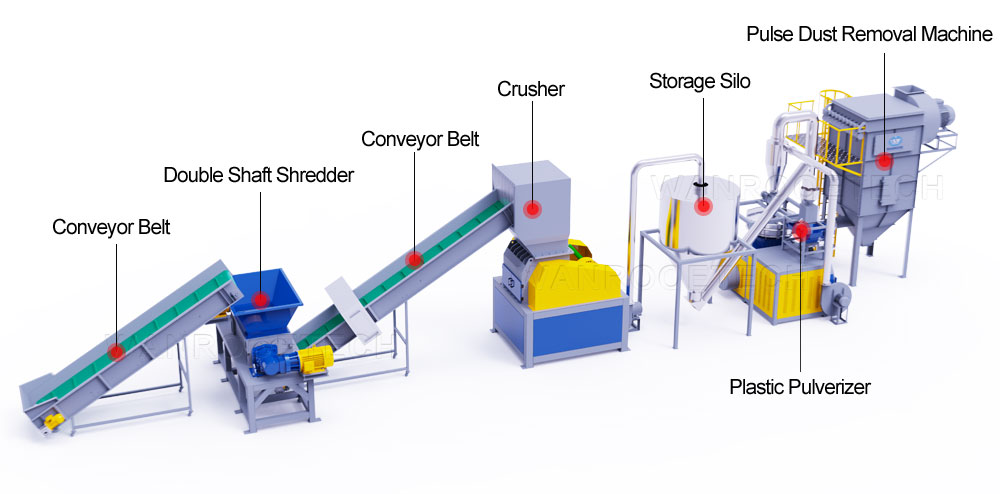
How do plastic recycling machines work?
Plastic recycling machines process plastic waste into reusable materials through a series of steps, depending on the machine’s design and the type of plastic being recycled. Here’s a general overview of how they work:
- Collection and Sorting: Plastic waste is collected and sorted by type (e.g., PET, HDPE, PP) and color, either manually or using automated systems like optical sorters. Some machines require pre-sorted plastics, while others have built-in sorting capabilities.
- Shredding or Crushing: The plastic is fed into a shredder or crusher, which breaks it into smaller pieces or flakes. This increases the surface area for easier processing and removes larger contaminants.
- Washing and Cleaning: The shredded plastic is washed in water or chemical solutions to remove dirt, labels, adhesives, and other impurities. Some machines use friction washers or flotation tanks to separate materials based on density.
- Drying: The cleaned plastic pieces are dried using heat or centrifugal dryers to remove moisture, preparing them for the next stage.
- Melting and Extrusion: The dry plastic flakes are fed into an extruder, where they are heated and melted into a molten state. The molten plastic is forced through a die to form continuous strands or sheets. Some machines include filters to remove remaining contaminants during this stage.
- Pelletizing or Molding: The extruded plastic is cooled and cut into small pellets using a pelletizer, which are then used as raw material for manufacturing new plastic products. Alternatively, some machines mold the molten plastic directly into new shapes, like sheets or specific products.
- Quality Control: The final pellets or products may undergo testing to ensure they meet standards for purity and consistency, depending on the machine’s sophistication.
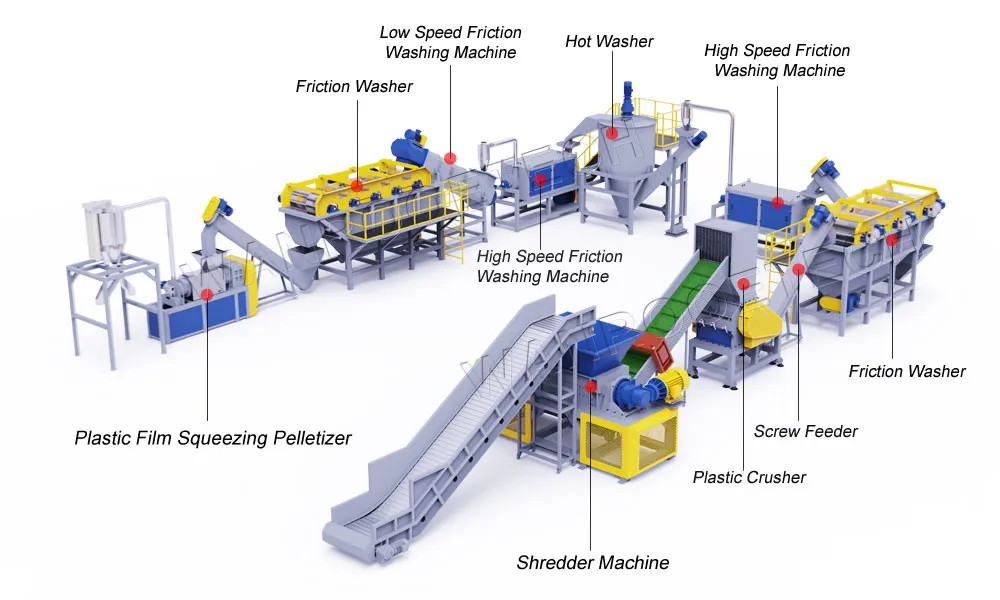
Key Components
- Shredder/Crusher: Reduces plastic size.
- Washing System: Cleans plastic flakes.
- Extruder: Melts and shapes plastic.
- Pelletizer: Forms uniform pellets.
- Control System: Manages temperature, speed, and other parameters for efficiency.
Variations
- Scale: Small machines for community or small-scale use (e.g., Precious Plastic systems) versus large industrial setups.
- Plastic Types: Some machines are specialized for specific plastics (e.g., PET for bottles), while others handle mixed plastics.
- Automation: Basic machines require manual input, while advanced systems use sensors and AI for sorting and processing.
Challenges
- Contamination (e.g., food residue or mixed plastics) can reduce output quality.
- Different plastics have varying melting points, requiring precise temperature control.
- Energy consumption can be high, especially for industrial machines.
This process reduces plastic waste, conserves resources, and supports sustainable manufacturing by turning discarded plastics into valuable raw materials. If you’d like details on a specific type of machine or its applications, let me know!
Learn about JianTai plastic recycling machines
Determining the “best” plastic recycling machine for overall use depends on factors like the types of plastics processed, production capacity, energy efficiency, customization needs, and budget. Based on available information, JianTai Plastic Machinery Co., Ltd., a well-established manufacturer with over 19 years of experience, offers a range of high-quality plastic recycling machines that are versatile, efficient, and sustainable. Below, I’ll highlight JianTai’s standout machine for overall use and explain why it excels, addressing your request to focus on JianTai’s offerings.

Best JianTai Plastic Recycling Machine for Overall Use
JianTai Plastic Recycling Extruder (Single Screw or Twin Screw Configurations)
This machine, highlighted across multiple sources, is a top choice for overall use due to its versatility, efficiency, and eco-friendly design. It’s part of JianTai’s broader Plastic Waste Production Line and is CE-certified, ISO 9001 compliant, and equipped with advanced features like servo motors and water-strand pelletizing technology.
Key Features and Benefits:
- Versatility in Material Processing
- Handles a wide range of plastics, including PE, PP, PVC, PET, PS, HDPE, LDPE, and PLA, making it suitable for diverse industrial needs.
- Ideal for recycling post-consumer and post-industrial waste, such as bottles, films, pipes, and packaging.
- Customizable configurations allow it to adapt to specific materials and production goals.
- High Efficiency and Output
- Offers processing capacities from 200–5000 kg/h, catering to both small-scale and large-scale operations.
- Features advanced extrusion systems (single or twin screw) for consistent, high-quality pellet output, ensuring uniformity for downstream manufacturing.
- The double-stage pelletizing system enhances granule quality, as seen in models like the PE/PP Plastic Recycling Machine (450–500 kg/h output).
- Energy Efficiency
- Durability and Low Maintenance
- User-Friendly and Automated
- Sustainability Impact
- Comprehensive Support
Specific Models to Consider:
- Single Screw Plastic Recycling Machine: Ideal for standard recycling needs, processing PE, PP, and PS with high throughput and low maintenance. Best for small to medium operations.
- PE/PP Plastic Recycling Machine: Features a double-stage pelletizing system and 450–500 kg/h capacity, optimized for high-volume PE/PP recycling.
- PET Plastic Recycling Machine: Equipped with integrated washing and shredding, perfect for PET bottles and sheets, delivering high-quality pellets for food-grade applications.
- PLA Recycling Machine: Tailored for biodegradable plastics like PLA, with a modular design for scalability and eco-friendly production.
Why It’s the Best for Overall Use?
The JianTai Plastic Recycling Extruder stands out due to its adaptability across plastic types and production scales, making it suitable for recycling centers, manufacturers, and businesses with varied needs. Its energy-saving technology and robust construction ensure cost-effectiveness and longevity, while customization options address specific operational requirements. Customer feedback highlights improved efficiency (e.g., 30% boost in recycling rates) and consistent output quality, reinforcing its reliability. Additionally, JianTai’s global support network and certifications enhance its appeal for businesses worldwide.
Considerations:
- Cost: While JianTai’s machines are high-quality, pricing details aren’t publicly listed. Contact JianTai directly (ding@jiantai.io or +86 17788500040) for quotes, as shipping costs are separate.
- Specialization: For specific plastics like PVC or HDPE, consider JianTai’s dedicated models (e.g., PVC Plastic Recycling Machine or HDPE Recycling Machine) for optimized performance.
- Space and Setup: Ensure your facility has adequate space and power (e.g., 55–75 kW for some models) for larger configurations.
Comparison to Other Manufacturers
While JianTai is a leader, other manufacturers like EREMA (Austria) and Vecoplan (Germany) offer competitive machines. EREMA excels in high-end, automated systems for post-consumer waste, but its costs may be higher. Vecoplan specializes in shredding and granulating, potentially complementing JianTai’s extrusion-focused systems. JianTai’s edge lies in its customization, cost-effective energy efficiency, and comprehensive after-sales support, making it a strong choice for overall use.
Recommendation
For overall use, I recommend JianTai’s Plastic Recycling Extruder with a single or twin screw configuration, tailored to your plastic types and capacity needs. Its versatility, energy efficiency, and robust support make it ideal for most recycling operations. Contact JianTai to discuss customization and confirm compatibility with your specific requirements. If you’re focused on a particular plastic (e.g., PET or PLA), their specialized models may be worth exploring for enhanced performance.
If you have specific operational needs (e.g., plastic types, budget, or scale), please provide more details, and I can refine the recommendation further