Make some changes to the world environment
-
Building 3, Wanyang Innovation City, Langxia Street, Yuyao City, Zhejiang Province
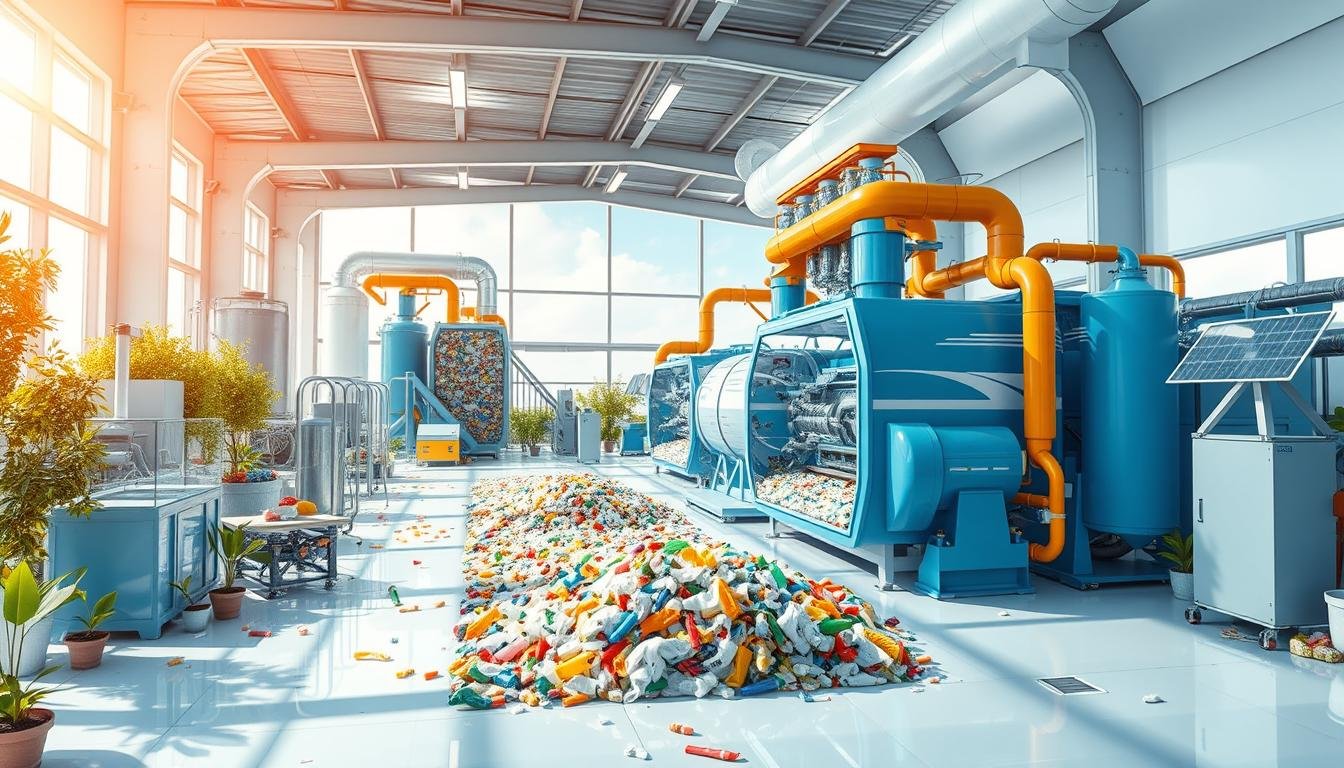
PP Plastic Recycling Machine Case Study
Managing plastic waste effectively is urgently needed today. This case study focuses on recycling PP plastic, especially from drink bottle caps. It’s a major move towards better waste management and sustainability. With the help of Linz Institute of Technology (LIT) Factory, Engel Austria GmbH, and the R-Cycle initiative, we see a big step forward. They are pushing recycling technology and aiming for a circular economy.
This effort shows how serious we are about protecting our planet. It blends technical knowledge with a strong environmental commitment.
Recycling materials like polypropylene (PP) and high-density polyethylene (PE-HD) is complex. This study shows the challenges and changes these materials go through. Adding a Digital Product Passport (DPP) is a big leap in recycling. It ensures every step is well-documented. This makes our journey to sustainability stronger.
Key Takeaways
- Understanding the symbiosis between post-consumer waste management and technological advancements in PP plastic recycling.
- Insight into the collaborative efforts necessary to enforce change in recycling practices, with a focus on caps made from PP and PE-HD materials.
- The importance of innovative documentation, such as the Digital Product Passport, in enhancing traceability within the recycling chain.
- Recognition of the need for comprehensive solutions to meet EU directives aimed at improving recyclability in packaging.
- Reiteration of the significance of case studies in providing empirical evidence to support progress in the recycling industry.
The Imperative for Plastic Recycling in the Circular Economy
As the world moves towards sustainability, the plastics industry is key. This is especially true with the push from Europe’s Green Deal. With plastic production over 390 million tons a year, shifting to a circular economy is crucial. Plastic recycling plays a big part in reducing environmental harm and saving resources.
Understanding how plastics impact our planet and economy is vital. Plastics make up 12.9% of US solid waste, half from packaging and single-use items. Cutting down waste helps our environment greatly. It also means less ends up in landfills.
Our push for a circular economy is due to alarming waste issues. For example, only 14% of plastic packaging is recycled. Yet, it could save us USD 80-120 billion yearly. Every minute, a truckload of plastic ends up in our oceans. We need strong waste reduction plans now.
Improving plastic recycling and resource conservation needs new ideas and designs. Using reusable packaging could bring in USD 10 billion. The reuse model could change 20% of plastic packaging, bringing huge benefits for both the planet and our economy.
We must invest heavily in plastic recycling technologies. This investment improves recycled plastic quality, making it suitable for more uses. It also cuts down carbon emissions by 30% to 80% compared to new plastic.
Here is our goal: to make the plastics industry a leader in the circular economy. This change is vital for our world’s future and safeguarding our environment for the next generations.
Advancing Towards Sustainability: The Role of Plastics
The plastic industry is pushing towards sustainability, and polyolefins are at the heart of this change. Thanks to eco-design, these materials are key in creating durable packaging and products. They help shape a sustainable future for production.
For plastics to truly fit into a circular economy, focusing on sustainability in production is critical. We’re improving recycling methods and making the whole lifecycle of products greener. This starts from getting the raw materials to the disposal of the products.
The Pure Cycle technology is a game-changer in recycling polypropylene. It produces high-quality plastics that are as good as new ones. This means plastics can be recycled over and over, cutting down on waste and boosting sustainability.
- Integration of sustainability in production practices, including the reduction of resource usage and minimization of waste
- Adoption of eco-design principles to ensure that products are designed with end-of-life recycling in mind
- Advanced recycling processes, such as pyrolysis and gasification, facilitate the transformation of disposed plastics into valuable secondary raw materials.
These methods are being used by industry leaders worldwide. The market for such recycling technologies is expected to hit over $9 billion by 2031. This growth shows the financial benefits of sustainable production methods.
Still, we face challenges with collecting and processing waste properly. This is a big hurdle for adopting new recycling methods. But the gains from a circular plastic use strategy are huge. It helps the environment, meets legal and consumer demands for sustainability.
As we enhance our recycling skills and make production more sustainable, we must also push for better recycling systems. This will change how plastics are seen in our society, making them a force for good in sustainability goals.
European Union’s Strategic Framework for Plastic Recycling
We are dedicated to fighting plastic pollution worldwide. We follow the EU strategy that addresses different aspects of plastic pollution. It includes laws and initiatives that promote a circular economy. Directive (EU) 2019/904 shows how the EU plans to cut down on single-use plastics and waste.
Transition Plan for a Circular Economy
The European Union has a strong plan to change how plastics are made, used, and recycled. At the heart of this plan is the goal to have all plastic packaging reusable or recyclable by 2030. This is outlined in the EU Plastics Strategy.
This strategy will move us from a linear to a circular economy. It is expected to prevent around 80% of the plastic waste that was once created.
Product Design and Mandatory Requirements
New EU rules will soon make sure products are designed to be more sustainable. They will require less packaging space, set high reuse targets, and use more recycled material. By 2030, we expect a big drop in single-use plastic production. This is thanks to these new rules and bans on certain plastic packages.
Digital Product Passport and Transparency
The Digital Product Passport is a big step towards making product lifecycles transparent. It will keep detailed records from when a product is made until it’s thrown away. This will help with sorting, tracing, and recycling. It’s a way to make recycling more efficient and help manufacturers join the circular economy.
Recently, the EU has made big moves to cut down on plastic waste. The new laws set clear goals:
Action | Goal | Deadline |
---|---|---|
Reduction in plastic packaging | 5% reduction | 2030 |
Ban certain single-use plastics | Eliminate specific packaging types | 2030 |
Implement Digital Product Passport | Enhance transparency and lifecycle management | Ongoing implementation |
Separate collection targets | 90% of single-use plastic beverage containers | 2029 |
With these actions, we aim to greatly improve how we handle plastic waste. We want a more sustainable world. The world is recognizing we need real change, and we are ready to help make that happen.
Capabilities and Challenges in Plastic Recycling Technologies
To make our future sustainable, we need to be good at recycling plastic. This includes separating plastics like HDPE and PP, which are mainly used in packaging. Understanding these technologies is key because they can do a lot but also face big challenges.
Separating materials for recycling is tough. Plastics often look and feel the same, making it hard to tell them apart for recycling. But, we are getting better with new sorting technologies. These improvements help a lot.
Statistic | Data | Implication |
---|---|---|
Plastic packaging waste in the UK (2000) | 37% | Signifies a major share of plastic waste, underlying the need for efficient packaging recycling solutions such as improved polyolefin separation techniques. |
Average MSW generated per person in the EU per year (2020 projection) | 680 kg | Indicates escalating waste generation, escalating the urgency for robust mechanical recycling systems. |
Plastics used in UK packaging per person per year | 40 kg | Substantiates the substantial use of plastics in packaging, necessitating focused recycling methods. |
Finding good ways to separate plastics in recycling is crucial. New methods that identify and split these plastics can change things big time. This will not only help the planet but also turn waste into something valuable.
We are dedicated to better recycling technology. Our goal is to face and beat these challenges. We aim to make recycling more effective and sustainable for everyone.
Impact of Packaging Applications on Recycling Needs
In the world of sustainable plastic use, plastic packaging applications play a key role in recycling. The way we manage these applications impacts our efforts in resource conservation and handling materials wisely.
Market Demand for Plastics in Packaging
The market demand for plastics in packaging shows why recycling is so important. Packaging makes up about 40% of all plastic used, making it the biggest use case. This high demand means we have both a chance and a duty to adopt sustainable methods and better recycling technologies.
Single-Use Plastics and Post-Consumer Waste
Handling the recycling of single-use plastics is key to lessening environmental harm. Shockingly, only 8% of plastic waste gets recycled worldwide. This is a big challenge. Most of these materials are used once then discarded, calling for complex sorting systems to recycle them efficiently.
Right now, recycled post-consumer PP packaging can cover only 3% of the PP need. This shows a huge gap that must be filled. With the European Union planning to require more recycled content in packaging, the call for effective recycling solutions is louder than ever.
Today, recycling centers focus on separating PP by type and color. This separation is mostly done by hand, making it expensive and effort-heavy. This highlights the need for technological advances in recycling. Such innovation could make recycling processes both cheaper and more efficient.
Wrapping up, the high demand for plastic packaging means we must commit to improving recycling. By focusing on the key issues of market demand, the role of packaging, and the challenges of handling waste, we step toward a greener future. This future is better for both our planet and our pockets.
Innovations in Recycling Plastic Bottles and Caps
We at [Your Company] know how vital it is to innovate plastic recycling, especially for PET bottles. It’s important for keeping the environment safe and enhancing recycling worldwide. Developing recycling systems that reuse materials fully is key for our planet’s future.
PET Bottle Recycling Schemes: A Model for PP
PET bottles are well-known in recycling efforts. Their recycling success can help us improve how we recycle polypropylene (PP) materials, like bottle caps. Using proven recycling methods, we can make PP recycling better. This is key for items used daily by people everywhere.
PET plastic is one of the most recycled materials, with a strong system for collection and recycling. Contrastingly, only 1 percent of PP is recycled around the world. By using PET’s recycling steps for PP, we aim to greatly increase this percentage. This is especially true for recycling bottle caps and similar items.
Complexities of Post-Consumer Waste Sorting
Sorting out waste after it’s been used is a big challenge. This is due to the mix of plastics used in packaging. For example, a PET bottle might have a PP cap and a different material for the label. These mixes make recycling more complex, as each part needs to be treated differently.
To better manage these challenges, we need improved sorting and recycling technology. With advancements in technology, especially through digital means and automation, we can sort waste more effectively. This makes it easier to recycle materials like PP, boosting recycling rates.
In conclusion, learning from PET bottle recycling can help us get better at recycling PP. By solving sorting challenges and using successful PET recycling strategies, we can make big advancements in PP recycling. These actions help the environment and encourage everyone to take part in a sustainable lifestyle.
PP Plastic Recycling Machine Case
We work hard to make recycling better and more sustainable. This case study looks at how material changes and new technology are changing recycling’s future. We show how our advanced machines process waste well, saving energy and increasing output.
Objective and Methodology of the Study
We wanted to see how well we can recycle plastics like bottle caps. We also looked at how changes in materials affect recycling. We used a waste stream analysis and a Digital Product Passport. This helps us track and show data on how materials are processed.
Practical Implementation of Inclusive Recycling Projects
We used digital tools to make recycling more inclusive and efficient. With the Digital Product Passport, we tracked material quality throughout recycling. This helped us manage different types of waste better. It also helped us support recycling in communities.
Model | Capacity (kg/h) | Features |
---|---|---|
Repro-Flex 120 | 500 | Designed for 95% printed surface recycling, higher output efficiency, 100% pellet re-usability |
Repro-Flex 100 | 350 | 20% higher efficiency, quick and straightforward installation |
LY-F220 | 300 | High efficiency with a 97% dehydration rate in the dewatering machine |
These improvements show how far we’ve come in recycling technology. We’ve cut down on energy use and increased output. This helps us reach our goal of sustainable recycling worldwide. By sharing these findings, we hope to encourage using new materials and tech for the environment.
Overcoming the Collection and Sorting Challenges
Understanding the role of innovative collection strategies in plastic recycling is crucial. These strategies are transformative for enhancing recyclability. They use both formal and informal methods, improving the quality and amount of plastics for recycling.
Innovative Collection Strategies
We combine advanced tech solutions and community initiatives to optimize collection. Using near-infrared (NIR) cameras helps identify and sort twelve polymer types. Also, digital watermarking, like projects such as HolyGrail, improves sorting of packaging materials.
This mix of technology and manual sorting boosts recyclability and increases waste collection. Partnerships with global brands, like Unilever’s work with Alibaba, use AI for smart recycling in cities. This makes recycling easier and more effective.
Framework of Informal vs. Formal Waste Collection
Informal and formal waste collection systems are vital in emerging economies. Formal systems use official recycling processes, while informal systems use local communities without oversight. This approach promotes inclusiveness and increases the capture rate of recyclables.
In places like India and Indonesia, informal collectors are key to the recycling process. Recognizing and integrating these workers improves economic and environmental outcomes.
These strategies are important for tackling waste management challenges. They pave the way for a cleaner and more sustainable future.
Revolutionizing Mechanical Recycling with Digitalization
In the world of sustainability, digitalization is changing mechanical recycling in a big way. With new digital tech, we’re making recycling processes better, faster, and smarter. This helps us use resources well and makes recycled materials of better quality and easier to trace.
At the heart of this change, digital tools are being used in new ways. Companies like Schneider Electric are working with tech partners such as GR3N. Together, they’re using advanced systems to improve how recycling plants work. Their goal is to make processes like turning PET plastic into its basic parts using microwaves more reliable and scalable.
- Advanced sorting technologies allow for more precise separation of plastics.
- Integrated software solutions enhance data collection and process monitoring.
- AI and machine learning algorithms predict and optimize recycling outcomes.
This combination of mechanical recycling and digitalization is about more than just new tech. It’s also creating a recycling system that’s better for the environment and makes financial sense. By using these new methods, recycling plants, like the one GR3N is building in Spain, will be able to handle 40,000 tons of plastic a year. This shows how applying these technologies can make recycling more effective at a large scale.
Technology | Description | Impact |
---|---|---|
Digital Product Passport | Traceability and quality assurance tool | Ensures the quality of recycled materials and facilitates market compliance |
AI-enabled Sorting | Automated waste sorting solutions by startups like Recycleye | Increases operational efficiency by minimizing manual sorting |
Thermal Scanning | Used for analyzing material composition at Veridis and Wecycle | Enhances the sorting accuracy, resulting in higher purity of recyclates |
We’re at a crucial moment where digitalization is key to improving mechanical recycling. As we innovate in recycling enhancements, our goal is clear. We aim to reduce environmental harm while recovering more resources.
A Case for Commercial Viability: The Midwest Extrusion Line
In the recycling world, finding affordable ways to help the environment and make money is key. We looked at a Midwest plastics recycler to see how it’s done. They updated their operations with a refurbished extrusion line. This machine turns PS regrind into high-quality pellets.
Strategic Budgeting and Line Setup
Choosing to invest wisely was crucial for success. They spent less by buying refurbished machinery from Arlington Machinery. This smart move saved money upfront and stuck to our cost-effective solutions plan. It made sure setup costs were within budget.
ROI Analysis and Equipment Optimization
We looked closely at the numbers to show the financial worth of the extrusion line. Even though it cost less at first, the machine worked as well as new ones. It saved a lot of money and proved spending wisely on equipment pays off.
Our financial plan included financing for the equipment, too. It showed that money spent could be made back quickly from selling the recycled pellets. Our plan pushed for more recycling and showed how smart investing can work well financially.
Parameter | Data Before | Data After |
---|---|---|
Initial Setup Cost | $1.2M (New Equipment) | $600K (Refurbished) |
Throughput | 450 tpy (New Equipment) | 450 tpy (Refurbished) |
Quality Output | High-grade pellets (New) | High-grade pellets (Refurbished) |
Return on Investment | 4 years (New Equipment) | 2 years (Refurbished) |
Our focus on smart investing matches our strategic goals. These wise choices help us build a recycling business that’s not just sustainable but also profitable. By showing clear benefits and making it easier to start recycling projects, we support our mission for cost-effective solutions and sustainable progress.
Implementation of Flake Sorting Technology by Greenpath
We at Greenpath lead in sustainable practices. We’ve adopted flake sorting technology for better polyolefin separation and innovative recycling methods. With over 25 years in recycling and operations across California, Nevada, and Texas, our commitment to using advanced technology for the environment is solid.
Sorting Mixed Polyolefins: Challenges and Solutions
Mixed polyolefins, like LDPE, HDPE, and PP, are tough to separate because they look and feel similar. But, our teamwork with TOMRA Recycling Sorting has changed the game. Their INNOSORT FLAKE technology helps us separate HDPE from PP with over 98% purity. This is a big step towards meeting the 2025 and 2030 circularity goals.
Advanced Sensor-Based Sorting for Caps
With TOMRA’s sensor-based sorting, we’ve revolutionized cap-to-cap recycling. The INNOSORT FLAKE, equipped with color cameras, can detect 16.8 million color variations for precise sorting. The FLYING BEAM™ lighting system saves energy and ensures reliable detection, improving our efficiency.
Feature | Benefit |
---|---|
Purity levels of 98%+ | Ensures high-quality recycled materials |
FLYING BEAM™ lighting system | Up to 80% energy savings and enhanced detection capabilities |
Identification of 16.8 million color variations | Higher accuracy in sorting processes |
Configuration flexibility | Adaptable to various operational scales and needs |
Global installation base (TOMRA) | Proven success with over 105,000 units in 100 markets |
Our partnership with TOMRA Recycling Sorting shows our commitment to leading-edge recycling technology. We focus on enhancing polyolefin separation with flake sorting technology. Our goal is to create more advanced and eco-friendly recycling processes worldwide.
Conclusion
We’re making real progress in our mission to boost plastic recycling success. Each step forward shows that a circular economy can work. This is especially true as we see PP plastic get recycled over and over. This recycling enriches our industrial lifecycle.
We have solid proof, not just theory. Our solutions like Repro-Flex, Repro-One, and Repro-Direct show how we’re changing polypropylene reuse. These tools help plastic recycling places work towards a circular economy every day.
We tackle big recycling challenges, like stopping plastics from ending up in landfills. Around 30% of all PP made is for packaging, with over 2 billion kilograms produced each year. This is shocking compared to the UK’s 1-3% recycling rate. Companies like GME Recycling are improving this by better collecting and sorting waste. This stops harmful substances like cadmium and lead from polluting through landfill PP waste.
By recycling more, we save money and use resources better. This also helps the planet in many ways. Recycling machines are key to this, boosting what we can save and use again. We aim to cut pollution and start using more sustainable methods for our planet’s future.
Indeed, we’re entering a new era for plastic recycling. Our creativity, technology, and environmental care are coming together. We’re building the base for a stable, successful circular economy.