Make some changes to the world environment
-
Building 3, Wanyang Innovation City, Langxia Street, Yuyao City, Zhejiang Province
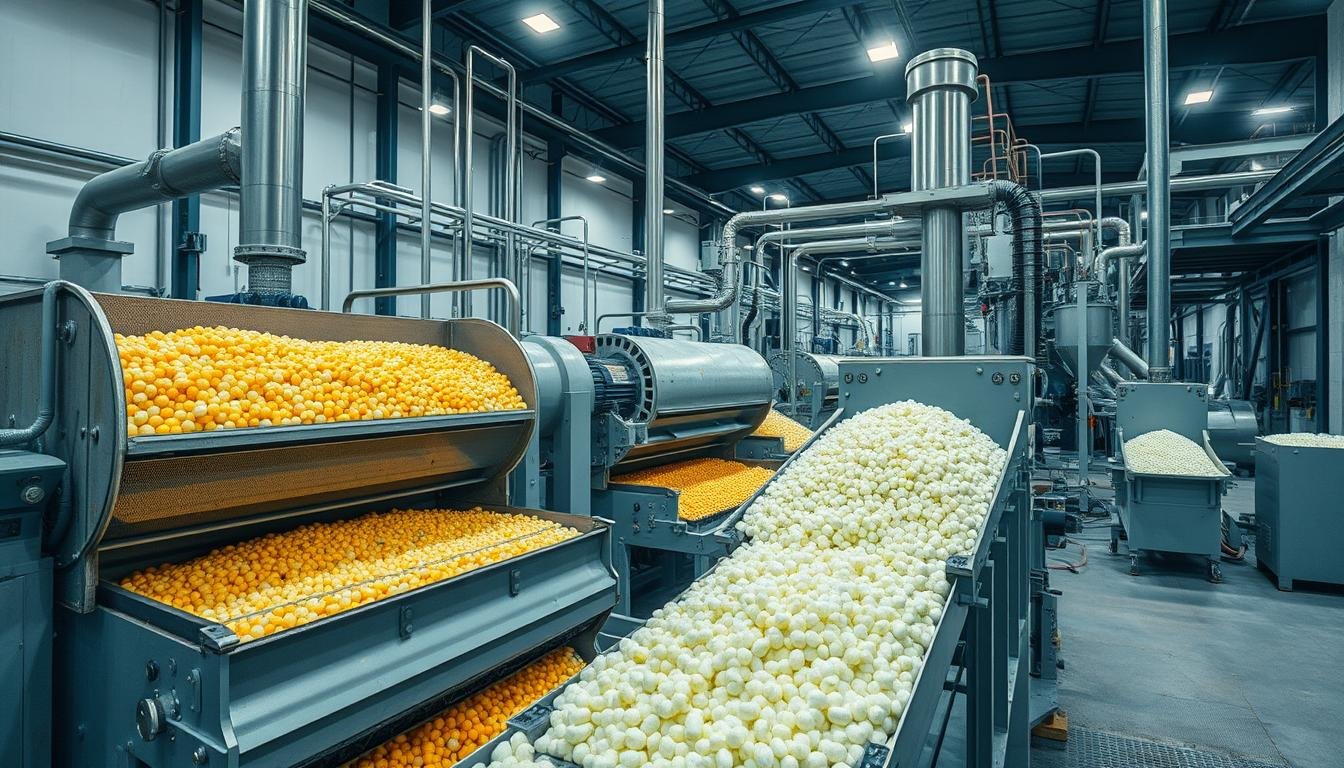
LDPE (Low-Density Polyethylene) Pelletizing
At Birch Plastics, we’re fully committed to leading the way in LDPE pelletizing. We offer top-notch low-density polyethylene production options. These have made a big impact on the market for plastic resin pellets. Our deep know-how in LDPE manufacturing means we get how vital these pellets are. They’re key for many production lines and offer essential features for an array of products.
LDPE granules are very handy because they’re light. This makes them perfect for making different kinds of bags1. Their low melting point also makes them easy to mold and shape, plus they’re strong when pulled1. LDPE is also great because it can handle chemicals well. This makes it ideal for packaging different products1.
Key Takeaways
- LDPE pellets are vital for many types of products because of their unique and cost-saving features.
- LDPE granules are chosen for packaging. They protect products from water and chemicals.
- Knowing how to pelletize LDPE well is key to making the most of LDPE production.
- It’s crucial to focus on being green, as LDPE materials don’t biodegrade easily.
- New technology helps with recycling LDPE. This lowers environmental harm and boosts efficiency.
Understanding LDPE and Its Properties
As part of the plastic industry, we deeply understand Low-Density Polyethylene (LDPE). It has unique features that are key in many applications, helping different sectors.
The Basics of Low-Density Polyethylene
LDPE is almost see-through with a density of 0.910–0.940 g/cm32. It’s light yet strong, with a tensile strength of 7.60-14.0 MPa3. This makes it suitable for tough uses. It can stretch a lot before it breaks, showing how flexible it is3. Also, LDPE melts at 102-113 oC, which means it stays tough at different temperatures that range from 145 to 340 °C3.
Advantages of LDPE Over Other Plastics
LDPE is more flexible than other plastics like LLDPE and HDPE. This flexibility makes it perfect for bendable products. It also handles temperatures well, up to 80 °C regularly and 95 °C for short times2. This makes it a strong choice for many industrial uses.
Common Uses for LDPE Resins
LDPE is versatile, safe for food, and meets high safety standards. It’s used in items like bottles, tumblers, and lids because it doesn’t break easily. LDPE is also in electrical cable coatings and household goods for its insulating traits2.
We use LDPE’s key features to make innovative, safe, and long-lasting products. These meet the changing needs of our customers.
The Role of LDPE in Packaging and Containers
There’s a growing need for both flexible and earth-friendly packaging. This need puts low-density polyethylene (LDPE) in the spotlight of the packaging world. With its mix of being strong, safe for food, and flexible, LDPE has become key in many sectors.
LDPE for Food Contact and Safety
When packaging touches food, it must be very safe. LDPE is tested well to make sure it’s safe and doesn’t harm food. You can find LDPE in things like wrap films, juice boxes, and caps4. It keeps food fresh and safe to eat without adding any risks to your health4.
Creating Unbreakable and Flexible Products
LDPE is used to make strong plastic containers. They can handle drops and pressure which is good for shipping and use. Items like reusable bottles, shopping bags, and food containers are often made from LDPE. Its ability to take many shapes and resist water is handy in many uses at home and work5. With LDPE, containers stay whole even when treated roughly. This highlights its use in making products that won’t break and can bend5.
Property | Advantage |
---|---|
Flexibility | Enables the creation of products that conform to various shapes and sizes. |
Durability | Products are resistant to tearing and deformation. |
Food-Safe Quality | Maintains food integrity and safety for consumer health. |
Recyclability | Contributes to environmental sustainability by being recyclable. |
Using LDPE in packaging helps with safety and works well. It also supports taking care of our planet. By choosing LDPE for strong plastic containers, businesses meet the needs for safe and green products. They also keep up with worldwide goals for taking care of the environment4.
LDPE (Low-Density Polyethylene) Pelletizing
In the realm of plastic recycling, LDPE is a star. It’s essential in turning polyethylene resin into pellets. These pellets are used in many products because of our focus on sustainability and technology.
LDPE pelletizing makes LDPE granules useful and lightweight1.They are perfect for things like carry bags and packing films. These pellets melt at a low temperature, which means they are easy to shape1.This is great for making stretchy things like grocery bags1.Also, LDPE pellets don’t let water, some acids, or bases through. This helps keep various products safe1.
However, LDPE granules aren’t perfect. They don’t break down in nature, so they can stay in landfills for a very long time1.Sunlight can also make them weak and crack. This is why working on better recycling methods is so important for the environment.
We aim to make LDPE pelletizing better. Not just by changing its physical aspects, but by making it more eco-friendly. We work to meet industry needs and help the planet. Our goal is to create durable LDPE pellets for various uses, improving our environmental footprint.
LDPE granules are super versatile. Here’s how different industries use them:
Industry | Applications |
---|---|
Packaging | Film, sheet production, bags, pouches, wrapping, lamination |
Building and Construction | Insulation materials, geomembranes, pond liners, pipes, fittings |
Agriculture | Mulching films, greenhouse coverings, irrigation systems |
Consumer Goods | Toys, bottles, containers, household products, medical equipment |
We are always looking for new ways to make LDPE pelletizing even better. We aim for high-quality products that are also good for the planet. Every step we take brings us closer to reusing materials and saving resources.
Industrial Pelletizing Process of LDPE
We are dedicated to refining the pelletizing process, focusing on producing LDPE. This section will cover the key steps in making LDPE pellets and how we aim to make the process more efficient.
Steps in LDPE Pelletizing
We start making LDPE by picking top-quality raw materials. We use over 1200 types of plastic materials. Our hot die face and water-ring systems produce less dust, making better quality pellets6. Each step is managed well to keep the pellets’ quality high, making them durable and versatile.
Maximizing Efficiency in Production
To make our production more efficient, we use GENIUS cutter compactor recycling machines. They use up to 20% less energy6. These machines help us make more pellets faster than old-school machines, putting us ahead in efficient pellet making.
Our underwater and strand systems are dustier but cut costs, great for big operations6. We also use the latest technology to make pellets. This includes different methods like extrusion and injection molding, backed by USEON’s experience with over 2500 machines delivered around the world7.
System Type | Investment Cost | Pellet Dusting | Output Capacity | Energy Saving |
---|---|---|---|---|
Hot Die Face and Water-Ring | Higher | Less | High | — |
Underwater and Strand | Lower | More | Average | — |
Cutter Compactor | — | Less | Higher | Up to 20% |
We keep improving the LDPE making process to lead the industry. Our investment in new machines and attention to detail shows our quality commitment. Our global network ensures fast delivery, often within 48 hours, proving our dedication to efficiency and customer happiness8.
The Importance of Melt-Flow Value in Pelletizing
In the plastic resin world, we know how much melt-flow value matters. It shapes LDPE quality and the features of plastic resins. By studying this value, we make sure our LDPE resins are perfect for their roles. This ensures products of high quality that meet expectations.
How Melt-Flow Affects LDPE Quality
The melt-flow rate (MFR) or melt index (MI) is key in shaping our pellets. A good melt-flow value makes processing smooth and keeps quality high. It shows how the resin will act when heated, which is crucial for making products work well and last long.
Melt-flow value doesn’t just affect how well processing goes9.It also changes the final traits of LDPE pellets. For example, high melt-flow rates might cause extra waste or issues like flashing. On the other hand, low rates could lead to mold not being filled right. So, getting this value just right is very important.
We pick our LDPE based on how molecular weight and melt-flow value connect. Often, more molecular weight means a lower melt index. This gives stronger connections and more strength. But, a lower molecular weight means a higher melt index. This can make the material flow better but not as strong. These factors directly influence the quality of LDPE, affecting how it’s processed and how strong the end product is.
Choosing the right polymer, with the proper density and melt index, is critical for different uses. The density of polyethylene affects its strength, stiffness, and how well it resists impact. These features are important for everything from packaging to tough industrial parts10.
By paying close attention to melt-flow value, we make our manufacturing better and improve our LDPE pellets10.Knowing all these details helps us find precise solutions for our customers. This way, we can match our products to the unique needs of different manufacturing processes.
Melt-flow Value | Processing Ease | Final Product Application |
---|---|---|
Low | Difficult Processing | High-Strength Applications |
High | Easy Processing | General Purpose / Low-Strength Applications |
Polyethylene Pellet Quality Control
We always aim to make the best polyethylene pellets. That’s why we use strict checks on quality. This is key because the tools we use in making pellets like strand pelletizers and die-face cutters are very advanced. They need us to be very careful in checking the quality. Strand pelletizers are great for working with many types of plastics because they are simple to use and many people use them11.
Ensuring High-Quality LDPE Pellet Output
Quality control means more than just following the rules. It’s about mastering the way we make pellets. The underwater pelletizer, getting better over the last 30 years, helps us make pellets of different sizes and shapes well. This method is top choice for very important tasks like finishing polymers, but there can be issues like fines that change how heavy the pellets are and make further steps hard11.
Also, problems like tails on pellets and other flaws don’t just look bad. They also make the pellets work less well, leading to issues when people use them later on11. These issues often happen if the strands of plastic aren’t cooled right before they’re cut, which is crucial11.
To avoid these problems, we follow the best quality control steps. We work like the best places in India that make LD plastic granules. These places, from Mumbai to Ahmedabad, use top-notch machines and the strictest quality checks. This way, we make sure every batch of LDPE pellets is the best it can be12.
We promise to make LDPE pellets that do more than just meet standards. They’re made to fit what our customers need perfectly. By using the latest technology and keeping a close watch, we keep our LDPE pellets top-quality. We work hard to make our pellets accurate, dependable, and consistent. This shows our commitment to being the best in making plastic recycling machines.
Application of LDPE Pellets in Injection Molding
Manufacturing moves from raw materials to finished goods with top-notch technology. LDPE pellets are vital in making many plastic parts through plastic parts production. They define progress in various LDPE uses.
From LDPE Pellets to Practical Parts
LDPE injection molding changes pellets into strong, versatile parts. This method is great for making many items quickly. It also keeps designs accurate. This is important for creating goods for cars, everyday items, and medical tools.
Choosing LDPE for its flexibility and how it behaves at low temperatures is smart. It helps make high-quality items13.
Getting machines and LDPE to work well together matters a lot1413. Also, drying LDPE pellets the right way before starting helps avoid mistakes. This makes the products better and more reliable14.
Benchmarking LDPE in Home Shops and Small Businesses
For small operations like home shops, LDPE molding is very helpful. It offers a way to be more flexible and save money. This is good for new businesses and hobbyists who want to make unique plastic parts easily. The Model 150A Plastic Injection Molding Machine is an example of an affordable machine for LDPE13.
LDPE’s qualities mean you can change the injection process to fit what you need. This ensures your final product is high-quality and meets tough standards1415.
Property | Significance in Injection Molding | LDPE Application Example |
---|---|---|
Melt Flow Rate | Ensures consistent melt and flow, critical for complex shapes | Container lids, toys |
Softening Temperature | Lower energy requirement for melting | Flexible tubes, textile packaging |
Flexibility and Strength | Aids in producing resilient and durable parts | Industrial buckets, automotive parts |
Businesses get ahead by smartly using LDPE pellets and tech. They handle both technical details and actual molding of LDPE well. This strategy leads to innovation and eco-friendly making. This way, they stay sustainable in what they make and do.
Choosing the Right Machinery for LDPE Pelletizing
Choosing the right equipment is crucial in LDPE pelletizing success. It’s about understanding various tech and features of plastic molding machines. It’s essential that the equipment fits your work needs and goals perfectly.
Comparing Injection Molding Machines
When deciding, comparing injection machines is key. The hot die face cutting system stands out for its efficient, quality pellet production16. It also has hopper feeding systems. This makes it flexible in processing hard plastic scraps, like crushed HDPE bottles16.
For a complete solution, consider compacting and pelletizing systems. Such systems make cutting, crushing, compacting, plasticizing, and pelletizing work together. This optimizes production for things like HDPE bags and zipper materials16. Genius customizes pelletizing systems. They provide everything from sorting units to efficient degassing units, setting them apart with their support, especially with remote installation help during the pandemic16.
Looking at specific machines, the RCDJ Series is great for processing LDPE and HDPE films, from scrap to packaging films17. Its strong motor handles HDPE films’ low flow well17. And, it has safety features like metal detectors on conveyors, protecting the machine and the product17.
Feature | Description |
---|---|
Extrusion/Film Melt Process | Uses an electric heated screw to melt film with a degassing station for printed materials17. |
Granules Cooling System | Has a water ring die face cutting system for cooling granules before drying17. |
Drying Options | Features include a vibrating screen and centrifuge force dryer for top drying performance17. |
In conclusion, detailed assessment is key when selecting LDPE machinery. Choose a system that fits a wide range of materials and includes crucial safety and efficiency features. This will boost your operations and overall productivity.
Advancements in Low-Density Polyethylene Technologies
We’re leading the way in crafting new LDPE tech, transforming how polyethylene is made. We’re also focusing on better LDPE recycling to tackle pollution caused by plastics.
Innovations in LDPE Manufacturing and Recycling
We’re stepping into a new manufacturing era by adopting methods that improve LDPE’s making and its eco-friendliness. Thanks to new reactor designs and catalysts, we can make better quality LDPE more accurately.
On the recycling side, we’ve made big leaps towards recycling LDPE more cleanly and efficiently. This supports the idea of a circular economy, where we use recycled LDPE without losing quality.
Statistic | Global Impact | Recycling Rates |
---|---|---|
Plastic Production | 350 million tons annually18 | 41% recycled or incinerated for energy18 |
PET Usage in Packaging | 56 million tons annually18 | 25% in the US, up to 52% in Europe1819 |
EU Plastic Packaging Recycling | 39.9% of plastic use19 | Nearly 50% in countries like Czechia, the Netherlands, Spain19 |
These stats show why recycling and making LDPE better is so crucial for our planet. By advancing recycling methods, we’re helping reduce plastic waste and pollution.
We’re committed to greener practices in making and recycling LDPE. By leading in tech innovations, we not only stay ahead in the market but also care for our planet.
Sustainability and Recycling of LDPE Pellets
In our journey towards LDPE sustainability, it’s crucial to grasp the environmental effects of its production. Globally, we produce about 19 megatons of LDPE every year20. This massive production highlights the urgent need for better recycling to cut down on plastic waste.
Our main goal is to lessen LDPE waste by enhancing our recycling efforts. Recycling LDPE helps reduce commercial waste. It also lowers the costs related to landfill taxes and waste disposal for businesses20.
The Environmental Impact of LDPE Production
The creation of LDPE is necessary for many uses but it comes with big environmental challenges. In the UK alone, people use over 564 million plastic bags yearly, and only 20% of these are LDPE bags that can be recycled20. Unfortunately, LDPE can take up to a thousand years to break down in nature20. This fact makes it clear we need better recycling solutions fast.
Strategies for Reducing LDPE Waste
- Strengthening Recycling Initiatives: Most home recycling programs take LDPE, listed under plastic code number 420. We plan to build on this.
- Advancing Technological Integration: The market for recycled LDPE pellets is growing fast. It’s expected to hit around USD 2.5 billion by the end of 202421, with a growth rate of 6% over the next five years21.
- Collaboration with Leading Enterprises: Working with top players in the LDPE recycling market like Jayplas and Fortum is key for better recycling21.
By following these plans, we aim to greatly influence LDPE sustainability. We hope to link LDPE production more closely with sustainable development and lower environmental harm.
Conclusion
In the world of industrial plastic making, we’ve carefully explored LDPE (Low-Density Polyethylene) pelletizing. We highlighted LDPE granules’ strong points, like their good stretchiness for items such as grocery bags, and their low melting point that makes manufacturing easier1. Plus, LDPE is cheap to make, which means more affordable products for various uses1.
However, we can’t overlook the environmental downsides of LDPE granules. They don’t break down and can last in landfills for hundreds of years, pushing us towards sustainable practices1. There’s a growing need for reused materials and using recycled LDPE in products like composites shows we’re moving to greener manufacturing22. The success of recycled LDPE depends on it being clean and uniform in size, which is crucial for the quality and life span of the final products22. Keeping recycled material consistent and improving the mixing process are key for making products last longer and resist water better22.
Ending our discussion on LDPE pelletizing, we stand by our goal to lead in this area with an eye on new ideas and eco-friendly methods. We aim to provide top-notch plastic recycling equipment that meets the industry’s changing needs while helping the planet. With LDPE pellets, we answer the demand for in-depth knowledge of polyethylene resin, backed by commitment to the environment and manufacturing excellence.