Realiza algunos cambios en el entorno mundial
-
Edificio 3, Ciudad de la Innovación Wanyang, Calle Langxia, Ciudad de Yuyao, Provincia de Zhejiang
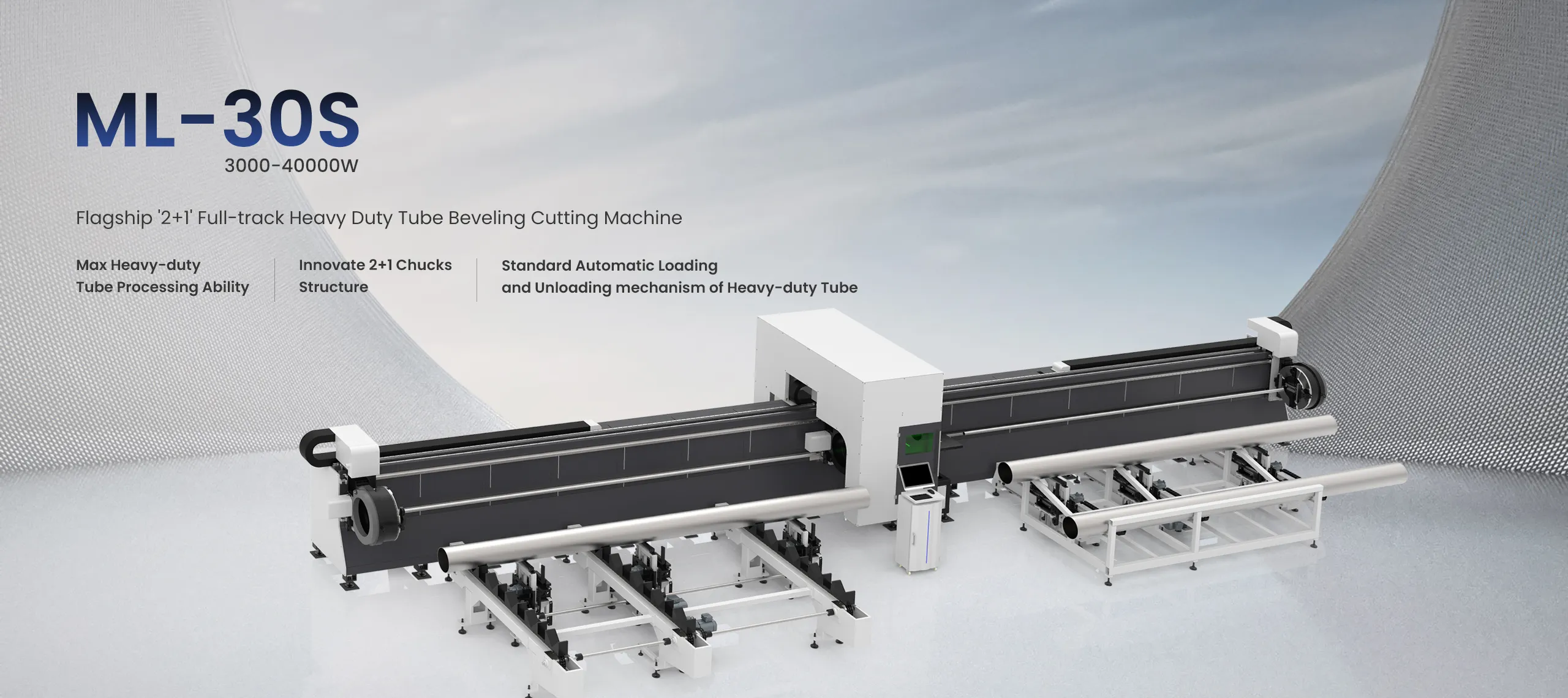
Laser Cutting Machines: Essential Guide for Beginners and Pros
Within precision manufacturing and creative design sectors, laser cutting technology has radically altered the process of converting raw materials into finished products. The world of laser cutting machines offers endless possibilities for both hobbyists entering the maker movement and seasoned professionals looking to enhance production workflows.
My extensive experience with diverse laser cutting systems has taught me that possessing the correct knowledge serves as the decisive factor between achieving ordinary outputs and stunning precision. The guide functions as a tool to close knowledge disparities for beginners while delivering advanced insights for seasoned users seeking to enhance their laser cutting skills. Prepare to navigate the intricate web of information as we delve into all essential aspects of these intriguing machines.
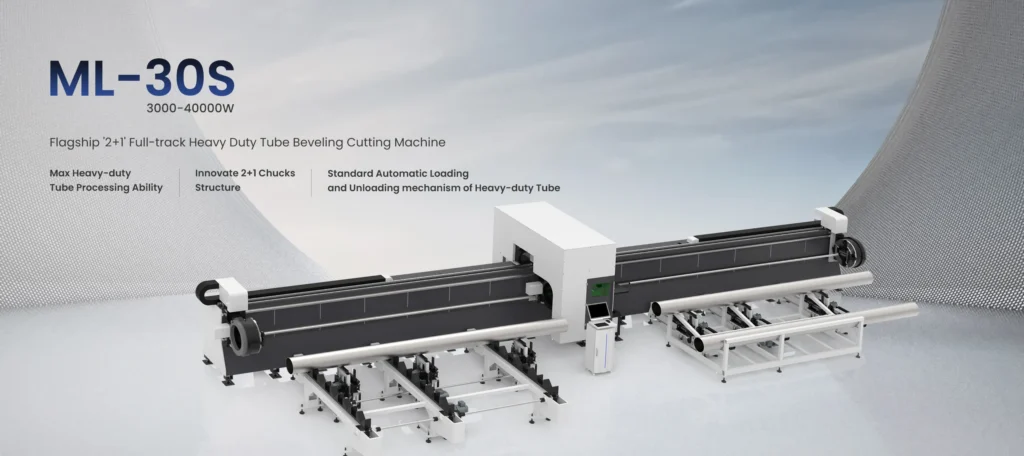
What Exactly Is a Laser Cutting Machine?
A laser cutting machine fundamentally operates as a technology that employs a concentrated light beam to achieve material cutting with remarkable accuracy. The term “laser” emerges as an acronym representing “Light Amplification by Stimulated Emission of Radiation. ” Sounds complicated, right? Upon detailed examination the concept reveals its fundamental simplicity.
A high-powered laser beam targets the material in these machines causing it to melt, burn, or vaporize away to produce edges with exceptional finish quality. Through computer numerical control (CNC) systems the beam follows a set path to produce intricate cutting patterns which traditional methods find challenging or unattainable.
The inaugural commercial laser cutting machine emerged in 1967 specifically to create perforations in diamond dies. These machines have evolved into essential instruments for a wide range of sectors including automotive manufacturing and fashion design. Technology advancement has reached new heights where it now stands as more accessible, precise and versatile than ever before.
Types of Laser Cutting Machines
Not all laser cutters are created equal. Depending on your needs, budget, and the materials you plan to work with, different types of laser systems might be more suitable. Here’s a breakdown of the main types you’ll encounter:
CO2 Laser Cutters
CO2 lasers are perhaps the most common type for general applications. They use a gas mixture (primarily carbon dioxide) that’s electrically stimulated to produce the laser beam.
- Best for: Non-metal materials like wood, acrylic, paper, fabric, leather, and some plastics
- Power range: Typically 30W to 150W for hobbyist/small business machines, up to several kilowatts for industrial models
- Pros: Relatively affordable, versatile for non-metals, widely available
- Cons: Limited metal-cutting capability (can only cut very thin metals)
I remember my first project on a CO2 laser—cutting intricate patterns into a wooden jewelry box. The smell of burning wood filled my workshop, but the precision of those cuts made it all worthwhile.
Fiber Laser Cutters
Fiber lasers represent the newer generation of laser cutting technology. They generate the laser beam by channeling light through optical fibers, resulting in a more concentrated beam.
- Best for: Metals including stainless steel, carbon steel, aluminum, brass, and copper
- Power range: 500W to 12kW+ for industrial applications
- Pros: Extremely precise, faster cutting speeds, lower operating costs, minimal maintenance
- Cons: Higher initial investment, less effective for non-metal materials
Crystal Lasers (Nd:YAG, Nd:YVO)
These solid-state lasers use crystals as the lasing medium, typically neodymium-doped yttrium aluminum garnet (Nd:YAG) or neodymium-doped yttrium orthovanadate (Nd:YVO).
- Best for: Precision cutting and marking of metals and some plastics
- Power range: Typically 5W to 500W
- Pros: High peak power, good for marking and engraving
- Cons: Higher maintenance requirements, shorter lifespan than fiber lasers
Direct Diode Lasers
The newest entrants in the field, direct diode lasers offer some compelling advantages:
- Best for: Various metals, especially reflective ones like copper and brass
- Power range: 1kW to 20kW
- Pros: Higher efficiency, compact size, lower operating costs
- Cons: Still developing technology, higher initial cost
During a recent manufacturing conference, I was blown away by a demonstration of a 15kW direct diode laser slicing through 1-inch stainless steel like it was butter. The technology has come so far in just the past few years!
How Laser Cutting Machines Work
Understanding the basic principles behind laser cutting can help you make better decisions about machine selection and operation. The process involves several key components working in harmony:
1. Laser Generation: The laser beam is created in the resonator, which contains the lasing medium (gas, fiber, or crystal).
2. Beam Delivery: The laser beam is directed through a series of mirrors or fiber optic cables.
3. Focusing Optics: The beam passes through a focusing lens that concentrates it into a small, intense spot.
4. Motion System: A CNC-controlled motion system moves either the cutting head or the workpiece (depending on machine design).
5. Assist Gas: In many applications, a gas (like oxygen or nitrogen) is blown coaxially with the laser beam to help with the cutting process and blow away molten material.
6. Sistema de control: Software translates your designs into machine instructions, controlling beam power, cutting speed, and motion.
The actual cutting happens when the focused laser beam heats the material to its melting or vaporization point. The material is then ejected from the kerf (the width of the cut) by the pressure of the assist gas.
Choosing the Right Laser Cutter for Your Needs
This is where things get personal. Your specific requirements should drive your decision-making process. Here are some key factors to consider:
Compatibilidad de materiales
What will you be cutting most frequently? This should be your primary consideration.
- For primarily wood, acrylic, and fabric: CO2 laser
- For primarily metals: Fiber laser
- For both: Consider a dual-source machine or prioritize based on your main application
Power Requirements
More power generally means faster cutting and the ability to cut thicker materials. However, it also means higher cost.
- Hobby/small business: 30W-100W CO2 or 20W-50W fiber
- Small to medium production: 100W-500W CO2 or 500W-2kW fiber
- Industrial production: 1kW+ CO2 or 2kW+ fiber
Work Area Size
Consider the largest piece you’ll need to cut:
- Small projects (jewelry, small parts): 12″ × 12″ or smaller
- Medium projects (signs, small furniture): 24″ × 36″
- Large projects (furniture, large signs): 48″ × 96″ or larger
Budget Considerations
Be realistic about your budget, but also consider the total cost of ownership:
- Entry-level machines: $2,000-$10,000
- Mid-range machines: $10,000-$50,000
- Industrial machines: $50,000-$500,000+
Remember that cheaper machines often have higher long-term costs in terms of maintenance, reliability, and limitations. I’ve seen too many small businesses struggle after buying the cheapest option available, only to spend more on repairs and eventually replacements than if they’d invested in quality from the start.
Space and Infrastructure Requirements
Don’t forget about:
- Physical space requirements (including safety clearances)
- Ventilation needs (all laser cutters produce fumes)
- Electrical requirements (especially for high-powered machines)
- Cooling systems (water chillers for higher-powered lasers)
Setting Up Your Laser Cutting Workspace
Creating an efficient and safe workspace is crucial for successful laser cutting operations. Here’s what you need to consider:
Safety First
Laser cutting involves high-powered beams, potentially harmful fumes, and sometimes flammable materials. Safety should never be an afterthought.
- Always use machines with proper enclosures to prevent direct exposure to laser radiation
- Install adequate ventilation systems to remove fumes and smoke
- Keep a suitable fire extinguisher nearby
- Never leave a running laser cutter unattended
- Consider installing smoke detectors and automatic fire suppression systems
Ventilation Requirements
This cannot be emphasized enough. Proper ventilation is absolutely essential:
- For small machines: A dedicated exhaust duct to the outside
- For larger operations: Industrial extraction systems with filtration
- For certain materials: Specialized filtration to handle toxic fumes
I once visited a small shop that had their laser cutter venting into the workspace through a standard carbon filter. The owner complained about constant headaches and respiratory issues—no surprise there. We immediately set up proper external ventilation, and his symptoms disappeared within days.
Power and Cooling
Ensure your electrical system can handle the requirements of your machine:
- Most hobby machines run on standard 110V/220V
- Industrial machines may require three-phase power
- UPS (uninterruptible power supply) for preventing data loss during power fluctuations
For cooling:
- Small CO2 lasers: Often air-cooled
- Larger CO2 and most fiber lasers: Require water chillers
- Maintain water cooling systems regularly to prevent algae growth
Material Storage
Organize your materials efficiently:
- Store sheet materials vertically to save space and prevent warping
- Label materials clearly with type and thickness
- Keep flammable materials away from potential ignition sources
- Consider humidity control for hygroscopic materials like wood and paper
Software and Design for Laser Cutting
The software side of laser cutting is just as important as the hardware. You’ll typically work with two types of software:
Design Software
This is where you create or prepare your designs:
- Vector programs like Adobe Illustrator, CorelDRAW, or Inkscape for cutting paths
- Raster programs like Photoshop for engraving images
- CAD software like Fusion 360 or SolidWorks for technical designs
- Specialized laser design software like LightBurn
Machine Control Software
This software takes your designs and controls the laser:
- Proprietary software that comes with your machine
- Third-party options like LaserWeb, LightBurn, or RDWorks
- Industrial solutions like CypCut for fiber lasers
Design Tips for Effective Laser Cutting
Creating designs optimized for laser cutting will save you time, materials, and frustration:
- Use the right colors/layers to distinguish between cutting, engraving, and marking operations
- Account for kerf width in precision assemblies (typically 0.1-0.3mm)
- Design with material properties in mind—some materials can’t achieve sharp interior corners
- For efficiency, nest parts closely to minimize material waste
- Test critical designs on scrap material before cutting expensive stock
Operating Your Laser Cutter: Best Practices
Once you’ve selected and set up your machine, mastering its operation will help you achieve the best results:
Material-Specific Settings
Different materials require different settings for optimal results:
- Laser power: Higher for thicker and denser materials
- Cutting speed: Slower for thicker materials, faster for thin ones
- Focus position: Critical for clean cuts (some materials cut better with the focus set slightly above or below the surface)
- Assist gas: Oxygen for carbon steel, nitrogen for stainless steel and aluminum
- Clean lens and mirrors (if accessible)
- Check alignment (for CO2 lasers)
- Clean cutting bed of debris
- Inspect exhaust system for blockages
- Deep clean optical components
- Check and clean air assist systems
- Inspect belts and moving parts for wear
- Clean filter systems
- Check laser tube condition (CO2 lasers)
- Lubricate moving parts according to manufacturer specifications
- Verify alignment throughout the entire beam path
- Check coolant levels and condition
- Professional inspection and servicing
- Replace worn components
- Complete realignment if necessary
- Electrical safety checks
Keep a “settings library” for materials you use frequently. I maintain a spreadsheet with proven settings for different materials and thicknesses—it’s saved me countless hours of trial and error.
Maintenance Routines
Regular maintenance is crucial for consistent performance and longevity:
Daily Maintenance
Weekly Maintenance
Monthly Maintenance
Annual Maintenance
Solución de problemas comunes
Even with proper maintenance, issues can arise. Here are some common problems and solutions:
- Poor cut quality: Check focus, clean optics, adjust speed/power, verify material quality
- Inconsistent cutting: Check for reflections from the cutting bed, ensure material is flat, verify cooling system operation
- Burning or excessive charring: Reduce power, increase speed, check air assist function
- Machine not firing: Check interlocks, water flow sensors, power supply
Advanced Techniques and Applications
Once you’ve mastered the basics, you can explore more advanced applications:
3D Laser Cutting
By controlling the Z-axis, some machines can cut at angles or variable depths:
- Creating beveled edges
- Cutting 3D forms from flat stock
- Producing interlocking components
Laser Engraving and Marking
Beyond cutting, most laser machines can also:
- Create detailed engravings by varying power levels
- Mark metals through annealing or etching
- Create photorealistic images through grayscale engraving
Multi-Material Processing
Developing expertise in cutting different materials opens new possibilities:
- Creating composite products combining wood, acrylic, and metal
- Understanding the limitations and advantages of each material
- Developing material-specific techniques for optimal results
Environmental and Safety Considerations
Responsible operation includes considering environmental impacts:
Emissions and Waste Management
- Filter and properly dispose of particulates from extraction systems
- Be aware of specific hazards from different materials (e.g., PVC produces chlorine gas)
- Consider recycling or reusing cut-off materials
Eficiencia energética
- Modern fiber lasers are significantly more energy-efficient than older CO2 systems
- Optimize cutting paths to reduce operation time
- Consider renewable energy sources for powering your equipment
The Future of Laser Cutting Technology
The field continues to evolve rapidly:
- Higher power densities enabling faster cutting of thicker materials
- AI-assisted path optimization and defect detection
- Integration with other manufacturing processes in smart factories
- More affordable, higher-quality options for small businesses and hobbyists
During the recent FABTECH expo, I was fascinated by demonstrations of hybrid laser-waterjet systems that combine the speed of laser cutting with the versatility of waterjet for difficult materials. This kind of innovation shows how the industry continues to push boundaries.
Conclusión
Whether you’re just starting your laser cutting journey or looking to refine your existing processes, understanding the fundamentals of this technology is essential for success. From choosing the right machine to mastering advanced techniques, each step in your laser cutting education builds toward greater capability and creativity.
The learning curve might seem steep at first—I certainly made my share of mistakes when I was starting out—but the precision and possibilities offered by laser cutting technology make it well worth the effort. Keep experimenting, stay safe, and don’t be afraid to push the boundaries of what’s possible.
What will you create with your laser cutter?