Realiza algunos cambios en el entorno mundial
-
Edificio 3, Ciudad de la Innovación Wanyang, Calle Langxia, Ciudad de Yuyao, Provincia de Zhejiang
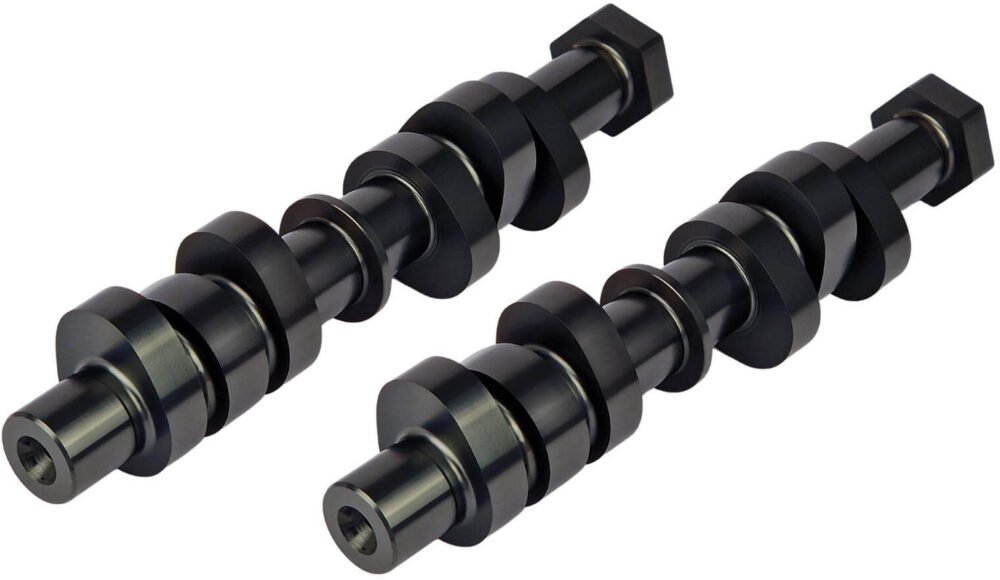
Guía completa de servicios de revestimiento DLC
Diamond-Like Carbon (DLC) coating services have gained significant traction across various industries due to their remarkable properties, such as high hardness, low friction, and excellent wear resistance. These coatings, which mimic some of the characteristics of natural diamond, are applied to a wide range of materials to enhance performance, durability, and longevity. This article explores the fundamentals of DLC coatings, the processes involved in DLC coating service, their benefits, applications, and key considerations for choosing a service provider.
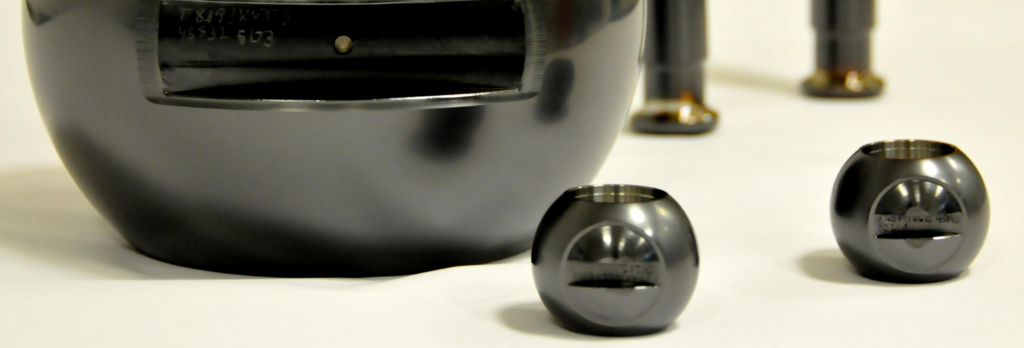
What Are DLC Coatings?
DLC coatings are a class of amorphous carbon materials that exhibit properties similar to those of diamond, including exceptional hardness and a low coefficient of friction. The term “diamond-like” refers to the presence of sp3 carbon bonds (typical of diamond) alongside sp2 bonds (characteristic of graphite), creating a unique hybrid structure. Depending on the deposition method and composition, DLC coatings can vary in hydrogen content, hardness, and other properties, making them highly customizable for specific applications.
These coatings are typically applied as thin films, ranging from 1 to 5 microns in thickness, using advanced techniques like Physical Vapor Deposition (PVD) or Plasma-Assisted Chemical Vapor Deposition (PACVD). The result is a durable, slick surface that enhances the performance of the substrate material, whether it’s metal, plastic, or even glass.

The DLC Coating Process
DLC coating services utilize sophisticated technologies to deposit these thin films onto substrates. The two primary methods are:
- Physical Vapor Deposition (PVD): In this process, carbon is vaporized in a vacuum chamber and deposited onto the substrate. Variants like arc-PVD and sputtering are commonly used, with arc-PVD producing hydrogen-free tetrahedral amorphous carbon (ta-C) coatings known for their extreme hardness (up to 5000-9000 HV). PVD is ideal for applications requiring high wear resistance, such as cutting tools and automotive components.
- Plasma-Assisted Chemical Vapor Deposition (PACVD): This method involves the use of a plasma to decompose a carbon-containing gas, depositing a hydrogenated amorphous carbon (a-C:H) layer onto the substrate. PACVD coatings typically range from 1200 to 2200 HV in hardness and are applied at lower temperatures (below 300°C), making them suitable for heat-sensitive materials like aluminum or low-tempered steels.
Some DLC coating services also offer hybrid processes, combining PVD and PACVD to create multi-layered coatings with tailored properties, such as enhanced adhesion or specific friction characteristics. The choice of method depends on the substrate material, desired coating properties, and intended application.
Benefits of DLC Coating Services
DLC coatings offer a plethora of advantages, making them a preferred choice for industries seeking to improve component performance. Here are some key benefits:
- High Hardness: With hardness levels rivaling or exceeding that of natural diamond, DLC coatings protect surfaces from abrasion and wear, significantly extending the lifespan of components.
- Low Friction: The smooth, lubricious surface of DLC coatings reduces friction (coefficients as low as 0.05-0.2), minimizing energy loss and wear in moving parts, even under dry conditions.
- Corrosion Resistance: DLC coatings act as a barrier against chemical attack and oxidation, making them ideal for harsh environments.
- Biocompatibility: Certain DLC formulations are safe for medical and food-contact applications, offering a non-reactive, bio-friendly surface.
- Versatility: These coatings can be applied to a wide range of substrates, including steel, titanium, aluminum, and ceramics, and can be customized with dopants (e.g., silicon or metals) to enhance specific properties.
- Aesthetic Appeal: DLC coatings often provide a sleek, dark finish, enhancing the visual appeal of products like watches, firearms, and automotive trim.
Applications of DLC Coating Services
The versatility of DLC coatings has led to their adoption across numerous industries. Some prominent applications include:
- Industria del automóvil: DLC coatings are widely used on engine components like piston rings, camshafts, and fuel injectors to reduce friction, improve fuel efficiency, and extend service life. Racing teams also rely on DLC to enhance the performance of lightweight alloys.
- Medical Devices: Biocompatible DLC coatings are applied to surgical tools, implants, and dental instruments to reduce wear, prevent galling, and ensure a hygienic surface.
- Cutting Tools and Molds: In manufacturing, DLC-coated drills, end mills, and injection molds benefit from increased hardness and reduced sticking, leading to higher efficiency and lower maintenance costs.
- Aerospace and Defense: Optical systems and mechanical components in harsh environments use DLC coatings for their durability and infrared transparency, as seen in thermal imaging systems.
- Bienes de consumo: From razor blades to luxury watches, DLC coatings enhance durability and provide an attractive, scratch-resistant finish.
- Industrial Equipment: Packaging knives, hydraulic pumps, and wear surfaces in industrial machinery benefit from the wear resistance and low friction of DLC coatings.
Choosing a DLC Coating Service Provider
Selecting the right DLC coating service provider is critical to achieving optimal results. Here are some factors to consider:
- Expertise and Experience: Look for a provider with a proven track record in DLC coating applications. Positive customer reviews and case studies can indicate reliability and quality.
- Technical Capabilities: Ensure the provider offers the specific deposition method (PVD, PACVD, or hybrid) and coating type (e.g., ta-C or a-C:H) suited to your needs. Advanced equipment and customization options are also a plus.
- Substrate Compatibility: Verify that the provider can coat your material of choice, as some substrates (e.g., soft metals like brass) may require special preparation to ensure adhesion.
- Turnaround Time and Scalability: For industrial applications, assess the provider’s capacity to handle your volume and meet deadlines. Lead times can vary from days to months depending on batch sizes and third-party involvement.
- Cost and ROI: While DLC coating services can range from $20 per part (for small batches) to higher costs for custom projects, evaluate the return on investment based on improved performance and reduced maintenance expenses.
- Customer Support: A responsive, knowledgeable team can help tailor the coating to your application and address any post-service concerns.
Future Trends in DLC Coating Services
The future of DLC coating services looks promising, driven by advancements in materials science and growing industrial demand. Researchers are exploring new doping techniques to enhance electrical conductivity or thermal properties, expanding DLC’s utility in electronics and energy storage. Additionally, integrating DLC coatings into manufacturing processes (e.g., directly onto molds) rather than post-production application could streamline production and reduce costs. As industries like automotive and healthcare prioritize durability and sustainability, the demand for eco-friendly, high-performance coatings like DLC is expected to rise.
Conclusión
DLC coating services offer a transformative solution for enhancing the performance and longevity of components across diverse applications. By combining diamond-like hardness with graphite-like lubricity, these coatings address challenges like wear, friction, and corrosion in ways that traditional treatments cannot. Whether you’re an automotive engineer seeking better fuel efficiency, a medical device manufacturer aiming for biocompatibility, or a consumer goods producer looking for durability and aesthetics, DLC coatings provide a versatile, reliable option. By partnering with a skilled service provider, businesses can unlock the full potential of this advanced technology, ensuring their products thrive in even the most demanding conditions. As innovation continues to propel DLC coatings forward, their role in modern industry is set to grow, making them an essential tool for the future.