إجراء بعض التغييرات على البيئة العالمية
-
المبنى 3، مدينة وانيانغ للابتكار، شارع لانغشيا، مدينة يوياو، مقاطعة تشجيانغ
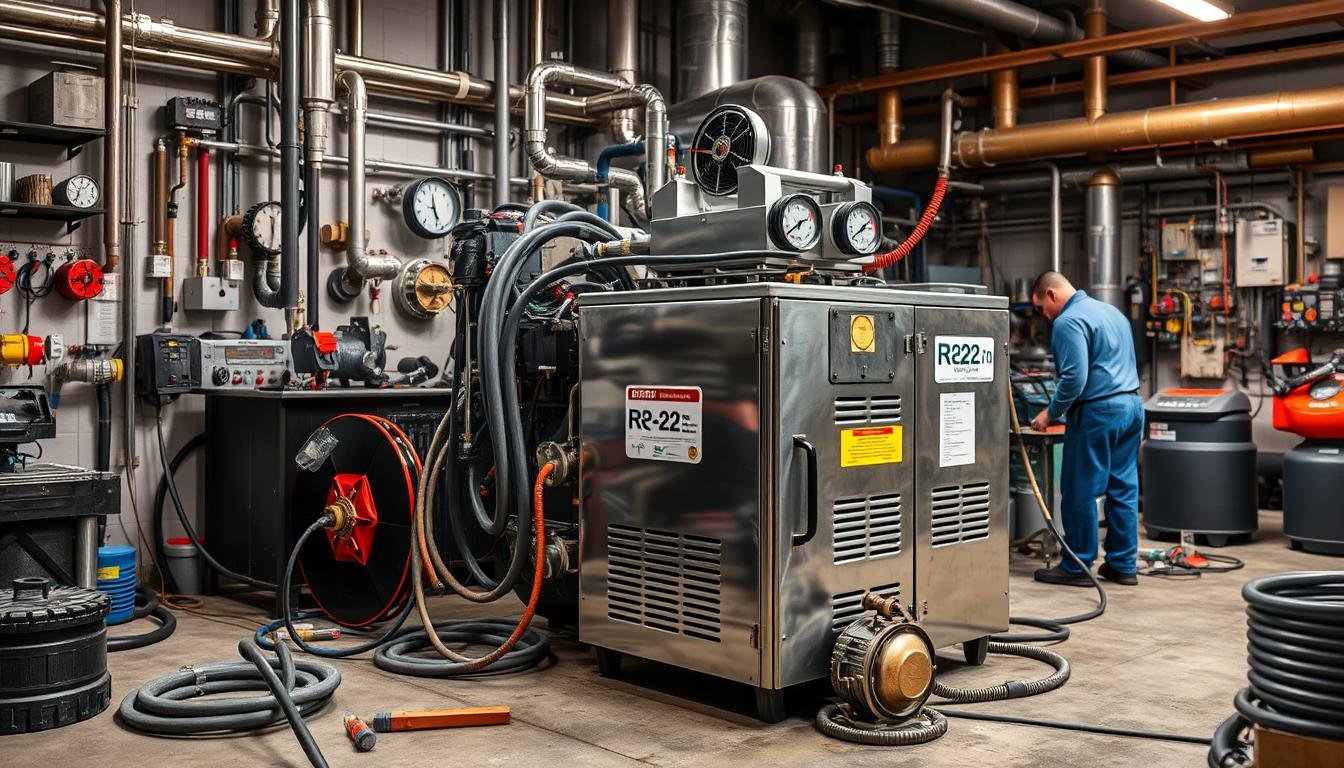
استعادة المبردات R-22 R-22: دليل صيانة الماكينة
Have you ever wondered why maintaining your R-22 refrigerant recovery machine is crucial for both efficiency and environmental compliance? As we transition to more eco-friendly refrigerants, it’s essential to understand the importance of keeping your HVAC system in top shape. This guide will offer practical tips on ensuring your machine’s longevity and adherence to the latest environmental and safety standards.
R-22, commonly known as Freon, is a hydrochlorofluorocarbon (HCFC) that significantly contributes to ozone layer depletion. Consequently, its production has been phased out in many countries, compelling homeowners to pivot towards more sustainable alternatives.R-410A is one such hydrofluorocarbon (HFC) characterized by its efficient cooling properties, making it a preferable choice over R-221. Adapting to these changes is not just an option but a responsibility we all share1.
الوجبات الرئيسية
- Understanding the phase-out of R-22 refrigerants and their environmental impact
- Importance of maintaining and properly handling R-22 HVAC systems
- Introduction to R-410A as a more eco-friendly and efficient refrigerant
- Practical guidelines for maintaining R-22 refrigerant recovery machines
- Ensuring compliance with environmental safety standards
Let’s dive deep into the intricacies of R-22 refrigerant recovery and how we can responsibly manage our HVAC systems amid these transitions.
Safety Precautions for R-22 Refrigerant Recovery
Ensuring safety during R-22 refrigerant recovery is crucial due to the potential hazards involved. From utilizing proper safety equipment for HVAC to strict adherence to protocols for handling pressurized refrigerants, every step must be meticulously followed to prevent accidents and avoid hefty penalties. With the decreasing supply of R-22 and the increasing demand, proper safety measures become even more critical2.
Importance of Safety Equipment
When dealing with refrigerants, using the appropriate safety equipment for HVAC is non-negotiable. This includes protective gear such as goggles, gloves, and respirators to safeguard against chemical exposure and potential injuries. Licensed technicians are mandated by Section 608 of the Clean Air Act to use AHRI-certified equipment, ensuring compliance with federal safety regulations2. Neglecting these protocols can lead to license suspension, fines of up to $37,500 per day, and severe health risks3.
Handling Pressurized Components
Handling pressurized refrigerants safely is another critical aspect during the recovery process. Mishandling these components can result in dangerous explosions or leaks. Only about 5% of R-22 refrigerant is currently being recovered and recycled, highlighting significant gaps in proper recovery and handling practices4. Regular maintenance is required for refrigeration equipment with a refrigerant charge over 50 pounds to prevent leaks and ensure safe operation3.
Fire Risks and Electrical Safety
HVAC fire risks must be addressed through vigilant adherence to electrical safety standards. Using equipment that is certified by the AHRI and UL ensures that the machinery meets stringent safety requirements set by the EPA3. The Clean Air Act mandates proper disposal of refrigerants to reduce harmful emissions and prevent fire hazards, emphasizing the need for meticulous attention to safety measures during every recovery procedure4. Failure to comply can lead to environmental contamination, costly fines, and severe health consequences2.
Operating Guidelines for Efficient Refrigerant Recovery
To ensure maximum R-22 recovery efficiency, it is urgent that we follow well-defined HVAC system setup procedures before initiating any recovery processes. The complexities involved demand attention to detail and adherence to standard operating protocols designed to optimize performance and operational longevity.
Initial Setup and Preparation
Starting with a precise HVAC system setup is fundamental. This involves connecting hoses and configuring service valves correctly. Ensuring that the hoses are leak-proof is a critical step in refrigerant recovery procedures. Proper evacuation of air and non-condensables from the system to 1,000 microns or less, as recommended by Honeywell, is essential5. Similarly, the integration of synthetic or POE oil in retrofit systems, such as those utilizing HFC-based refrigerants like Genetron 422D, enhances efficiency by ensuring adequate oil return5.
Optimal Operating Conditions
The efficiency of operating HVAC machinery is influenced by various environmental and mechanical factors. Ambient temperature and system pressure are pivotal in determining recovery speed and efficacy. Recovery units must be operated under optimal conditions to mitigate the impact on ozone depletion potential (ODP) and reduce global warming potential (GWP)6. For instance, R-22 has a GWP of 1,700 and an ODP of 0.034, necessitating precise control measures to minimize environmental harm6.
For effective refrigerant recovery procedures, it is beneficial to maintain system pressures and temperatures within recommended thresholds. By doing so, we not only enhance the R-22 recovery efficiency but also adhere to environmentally friendly practices. Moreover, Honeywell suggests starting with 85% of the original charge for newly charged systems and then incrementally adding refrigerant, optimizing the operational conditions for achieving maximum performance5.
Adhering to these guidelines not only ensures compliance with regulatory standards but also significantly amplifies the R-22 recovery efficiency. مناسب HVAC system setup and adherence to these operating guidelines is vital for the longevity and performance of recovery units, ensuring sustainable environmental practices.
تحتوي ماكينة إعادة التدوير المسترجعة الخاصة بك على غاز تبريد R 22
مناسب refrigerant recycling و R-22 management are vital due to the environmental impact of R-22 and the necessity for HVAC compliance. Managing R-22 refrigerant effectively begins with understanding the regulatory landscape. For instance, major repairs under EPA regulations include the replacement of an evaporator coil7. It’s crucial to use certified recovery and recycling machines to prevent any unlawful release of refrigerants into the atmosphere, ensuring compliance with refrigerant recovery licensing requirements.
When recovering refrigerant in the vapor phase, the loss of oil is minimized, enhancing the efficacy of your refrigerant recycling الجهود المبذولة7. For systems containing R-410A, it’s essential to evacuate before changing the compressor and use nitrogen for leak checks8. More importantly, certified equipment should be employed to manage refrigerants like R-410A and R-22.
EPA regulations do not mandate the reporting of purchases related to recycling and recovery equipment7. Nevertheless, using specific EPA-certified tools ensures HVAC compliance. Especially in scenarios involving large appliances or systems, such as those containing over 200 pounds of refrigerant, major repairs demand exacting standards for evacuation and recovery78. Hence, refrigerant recovery licensing becomes indispensable, safeguarding both the environment and regulatory adherence.
الانخراط في R-22 management includes routine tasks like ensuring that post-repair leak verification tests are completed within stipulated time frames. For instance, after a rack repair involving 3000lbs of R-22, a follow-up leak verification must be conducted within 10 days post initial repair7. Implementing these checks emphasizes our commitment to responsible refrigerant recycling الممارسات.
Recycling and recovery machines must be EPA-certified and designed to handle specific refrigerants, including R-410A and R-22, aligning with HVAC compliance norms. Notably, systems should be evacuated to appropriate levels before any major repairs78. Following these protocols not only ensures efficiency but also fortifies our stance on environmental responsibility.
To summarily emphasize, refrigerant recycling and R-22 management are non-negotiable aspects of our industry, demanding precise adherence to HVAC compliance and refrigerant recovery licensing standards. Even the smallest deviations can lead to significant environmental repercussions, highlighting the indispensability of stringent management practices.
Proper Care and Maintenance of 25176B Machine
Performing regular care and maintenance of HVAC equipment, specifically the 25176B machine, is critical to ensure its longevity and operational efficiency. Let’s delve into the key practices for maintaining this essential piece of equipment.
Regular Inspection and Cleaning
Routine inspections are vital for identifying any potential leaks or defects in the 25176B machine. By regularly examining the unit, we can address small issues before they escalate. Additionally, cleaning recovery machines prevents contamination and ensures optimal performance. It is recommended to clean and inspect the machine after each use to prevent debris buildup, which could hinder its operation.
Use of Filters and Dryers
Using HVAC filters and dryers significantly enhances the operation of the 25176B machine. High-acid capacity filters, like the Alco type EK-162-F or Sporlan type C-162-F, are recommended for systems recovering from burnout conditions9. Incorporating these filters ensures the machine runs smoothly and mitigates the risk of system contamination.
Storage and Handling Tips
Proper storage of HVAC tools is crucial for maintaining their integrity and functionality. When storing the 25176B machine, keep it in a clean, dry environment to prevent any moisture damage. Ensure that all accessories and hoses are kept in a designated area to avoid misplacement. Proper handling during usage and storage will significantly extend the machine’s service life and maintain its operational efficacy.
Tank Size | Maximum Net Weight | الاستخدام الموصى به |
---|---|---|
30 lb. | 24 lbs | Use for moderate volume tasks to avoid overfilling10 |
50 lb. | 40 lbs | Ideal for larger recovery tasks to maximize efficiency without exceeding capacity10 |
Following these guidelines for the maintenance of HVAC equipment ensures optimal performance and longevity of the 25176B machine. Regular inspection, using the right filters and dryers, and proper storage and handling are key to maintaining this essential tool in peak condition10.
Tank Management and Capacity Guidelines
الفعالية refrigerant tank safety measures are crucial in ensuring smooth operations within any HVAC system capacity. The Clean Air Act of 1990 and the Montreal Protocol Treaty underline the mandate for the industrial refrigeration industry to recover, recycle, and reclaim refrigerants, helping operators avoid government fines11.
Recovery tank management is paramount for both safety and efficiency. To comply with legal requirements, a refrigerant tank can only be filled to 80% capacity and must remain below 122°F12. For instance, a 30 lb cylinder is legally restricted to holding 22 lbs of refrigerant, while a 50 lb cylinder can accommodate up to 38 lbs12.
Refrigerant storage protocols also emphasize that different types of refrigerants must never be mixed or stored together to prevent unexpected chemical reactions11. Furthermore, the recovery tank’s capacity must be calculated accurately to confirm it safely receives the amount of refrigerant being unloaded12.
We must highlight the importance of monitoring the condition of our tanks vigilantly. Cylinders displaying signs of rust, damage, or heat should be depressurized and disposed of properly, ensuring they do not pose any safety risks12. Adhering to these practices not only enhances refrigerant tank safety but also contributes to a more efficient HVAC system capacity.
Moreover, keeping detailed records of recovered refrigerant is mandatory for mid-sized appliances containing between 5-50 pounds of refrigerant12. When a recovery cylinder reaches full capacity, it must be sent for proper reclamation; under no circumstances should it be discarded in the trash12.
Refrigerant Capacity | Percentage Fill | Max Capacity (lbs) |
---|---|---|
30 lb Cylinder | 80% | 22 lbs12 |
50 lb Cylinder | 80% | 38 lbs12 |
By maintaining stringent management practices, our approach to recovery tank management reinforces the safe operation of our systems. Proper care during refrigerant storage and accurate record-keeping ensure sustainable and compliant practices in our industry.
Advanced Techniques for Faster Refrigerant Recovery
التنفيذ advanced refrigerant recovery techniques ensures efficient and quick recovery processes, especially for large HVAC systems. Two significant methods are the push/pull recovery method و cooling techniques, both pivotal in enhancing HVAC efficiency.
Using the Push/Pull Method
إن push/pull recovery method leverages pressure differentials to accelerate refrigerant recovery times. This method is particularly useful when dealing with systems that contain large amounts of refrigerant. When applied correctly, it can substantially reduce recovery times by using the high-side pressure to push liquid refrigerant into the recovery cylinder while pulling vapor from the low side through the recovery machine.
In modern HVAC practice, it’s essential to use recovery machines that are compatible with various refrigerants like R-22 and R-410A, ensuring flexibility and efficiency13. The 25175B recovery unit, for example, is capable of handling multiple refrigerants, making it an excellent choice for facilities that encounter different refrigerant needs14. This adaptability is beneficial, as dedicated recovery units may be necessary to avoid cross-contamination of oils and refrigerants, especially given the phase-out of R-22 and the increased cost associated with its recovery15.
Cooling Methods for Efficiency
Cooling techniques are an effective way to enhance HVAC efficiency during refrigerant recovery. Lowering the temperature of the recovery tank reduces pressure, facilitating a faster refrigerant transfer. Using a recovery machine fitted with proper filters and dryers can further boost the efficiency of this process14. Ensuring that components like hoses and seals are in optimal condition can prevent flow restrictions and enhance overall performance by up to 90%14.
Recovery rates can be maximized by using shorter hoses of larger diameters, as this minimizes flow resistance14. It’s crucial to follow recommended practices, such as using filter/dryers and maintaining hose integrity, to achieve the best recovery results. These measures not only expedite the recovery process but also contribute to the longevity and efficiency of HVAC systems.
Given the increased demand for advanced refrigerant recovery techniques, adopting these methods can lead to significant improvements in operational efficiency and compliance with environmental regulations. Transitioning from R-22 to alternative refrigerants like R-410A requires understanding the implications for recovery equipment and practice1315. By integrating the push/pull method and cooling techniques, HVAC professionals can achieve faster, more efficient refrigerant recovery while ensuring system longevity and reliability.
الخاتمة
In wrapping up our comprehensive guide, we hope to have provided a clear understanding of the critical aspects surrounding R-22 refrigerant recovery and machine maintenance. From initial safety precautions and handling pressurized components to advanced techniques for optimizing the efficiency of recovery processes, each step is essential for summarizing HVAC maintenance.
The importance of using proper equipment, such as the Model 17800B/17801B Recovery/Recycling/Recharging Unit, cannot be understated. Its advanced features, including a built-in 6 cfm vacuum pump and electronic scale, ensure accurate and efficient operation for various refrigerants, all the while adhering to legal and environmental standards16. Furthermore, managing refrigerants responsibly is not merely a recommendation but a legal obligation to minimize environmental impact and avoid significant fines17.
As we face the ongoing phase-out of R-22 due to its high GWP, it becomes ever more critical for technicians to stay informed on regulatory changes and advancements in environmentally friendly alternatives such as R-410A. This knowledge is fundamental to ensuring HVAC compliance and promoting sustainability. We highly recommend visiting resources like Eco Home Solutions to stay updated on best practices in refrigerant recovery and disposal17. By doing so, we contribute not only to our professional growth but also to the collective effort of protecting our environment.