Make some changes to the world environment
-
Building 3, Wanyang Innovation City, Langxia Street, Yuyao City, Zhejiang Province
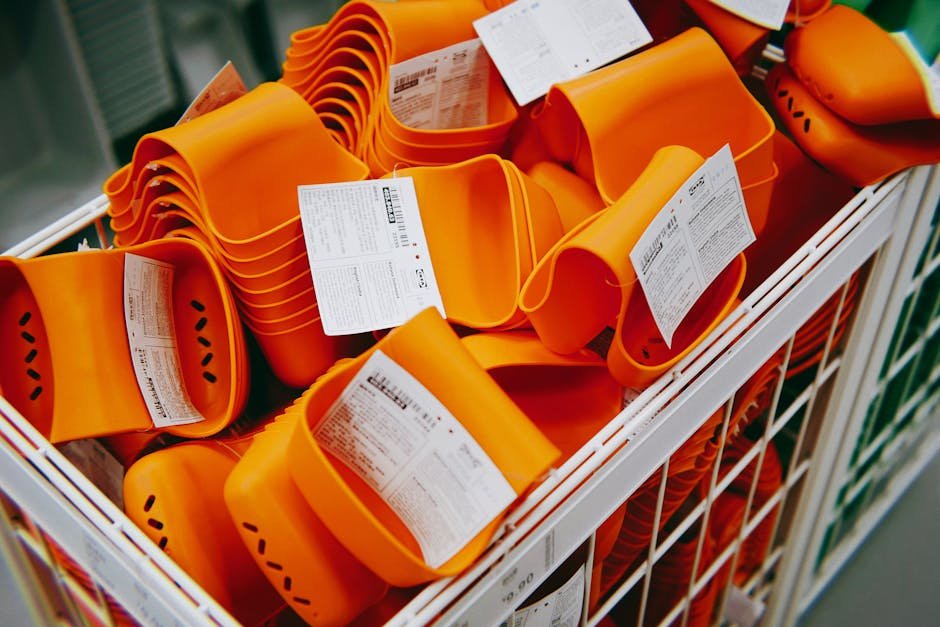
Surprising Plastic Extrusion Products You Use Daily
Discover plastic extrusion products in daily life, from pipes to sports gear, enhancing performance and sustainability.
The Surprising World of Plastic Extrusion Products
Plastic extrusion products are all around us, often going unnoticed despite playing crucial roles in our daily lives. If you’re wondering what these products are, here’s a quick overview:
Common Plastic Extrusion Products | Examples | Industry Applications |
---|---|---|
Pipes and Tubing | PVC pipes, medical tubes, drinking straws | Plumbing, healthcare, food service |
Films and Sheets | Shopping bags, food packaging, blister packs | Retail, food, pharmaceutical |
Profiles and Frames | Window frames, door seals, trim | Construction, automotive |
Wires and Cables | Electrical wire insulation, cable coatings | Electrical, telecommunications |
Solid Shapes | Decking, outdoor furniture, sports equipment | Construction, recreation |
Plastic extrusion is a high-volume manufacturing process where raw plastic is melted and formed into a continuous profile. This versatile process creates products with consistent wall thickness and can be custom to produce items of virtually any length.
When you turn on a faucet, flip a light switch, or open a window, you’re likely interacting with plastic extrusion products. From the pipes carrying water throughout your home to the insulation protecting electrical wires in your walls, these products are fundamental components of modern infrastructure.
What makes plastic extrusion so remarkable is its efficiency. As a continuous manufacturing method, it’s more economical than other plastic production processes, especially for high-volume output. This explains why extruded plastic has become ubiquitous in industries ranging from construction and automotive to healthcare and consumer goods.
“Plastic extrusion is unquestionably one of the most versatile manufacturing processes,” notes industry experts, highlighting how this single technology can create products ranging from microscopic medical tubing (less than 0.010 inches in diameter) to large sewer pipes several feet across.
At JianTai Plastic Machinery Company, we’ve witnessed how plastic extrusion technology continues to evolve, particularly with growing emphasis on recycling and sustainability. Modern extruders can now process various plastic waste streams, changing what might have been landfill material into durable new products.
Plastic Pipes and Tubing
Take a moment to look around your home. From the water flowing through your faucet to the drainage system beneath your sink, plastic extrusion products are silently supporting your daily life. Pipes and tubing represent some of the most common and valuable applications of plastic extrusion technology.
What makes extruded pipes so remarkable is their versatility. They can range from massive sewer pipes several feet in diameter to delicate capillary tubes smaller than a strand of spaghetti. PVC pipes have become the backbone of modern plumbing systems worldwide, replacing traditional materials in countless applications.
“We see pipes as the unsung heroes of infrastructure,” shares our engineering team at JianTai Plastic Machinery Company. “Most people never think about the complex network of extruded plastic pipes delivering clean water to their homes or carrying waste away—until something goes wrong!”
The beauty of the extrusion process lies in its consistency. Every foot of an extruded pipe maintains uniform wall thickness and material properties, creating reliable products that can withstand decades of use. This uniformity simply isn’t possible with many traditional manufacturing methods.
Compared to metal alternatives, extruded plastic pipes offer tremendous advantages. They resist corrosion, weigh significantly less (making installation easier and less expensive), and provide smoother interior surfaces that improve flow efficiency. They also offer superior chemical resistance, better insulation properties, and often greater flexibility—all while typically costing less than metal alternatives.
From agricultural irrigation systems to gas distribution networks, plastic extrusion products in the form of pipes and tubing have revolutionized how we build infrastructure around the world.
Medical Tubing: Precision in Healthcare
When it comes to showcasing the precision capabilities of plastic extrusion, nothing compares to medical tubing. In hospitals and clinics worldwide, extruded plastic tubes perform life-saving functions where even the slightest imperfection could have serious consequences.
Medical professionals rely on extruded catheters for minimally invasive procedures, IV lines for medication delivery, and specialized tubing for everything from feeding to respiratory therapy. The most remarkable achievement in this field is the development of micro-miniature tubes with outer diameters thinner than human hair—some measuring less than 0.010 inches across!
These tiny marvels of engineering enable surgeons to access areas of the human body that would otherwise require major invasive surgery. Neurovascular interventions and pediatric procedures that once seemed impossible are now routine, thanks to precisely extruded medical tubing.
What makes extrusion particularly valuable for medical applications is its flexibility in design. Manufacturers can create multi-lumen tubing with several internal channels running through a single tube. They can precisely control wall thickness down to microscopic levels and even incorporate radiopaque materials that show up clearly under X-rays and other imaging techniques.
Perhaps most impressively, advanced extrusion techniques can produce tubing with variable stiffness along its length—rigid at one end for control and flexible at the other for patient comfort. And because extrusion creates seamless products, there are no weak points or connection sites that might fail.
At JianTai Plastic Machinery Company, we understand that while our focus is on recycling equipment, the fundamental principles of extrusion technology flow through all applications—from the massive pipes carrying water through cities to the delicate tubes used in the most sensitive medical procedures. Our commitment to precision engineering supports the broader ecosystem of plastic extrusion products that improve lives worldwide.
Plastic Films and Sheeting
When you reach for a shopping bag, unwrap food packaging, or open a blister pack containing a new product, you’re handling another category of plastic extrusion products: films and sheeting. These thin, flexible materials are omnipresent in our daily lives, often going unnoticed despite their crucial role in protecting and preserving countless items.
The magic behind these versatile materials happens through a process called blown film extrusion. Picture this: molten plastic is pushed through a circular die to form a tube, which is then inflated like a giant balloon, creating an incredibly thin film. If you’ve ever blown a bubble with gum, you’ve experienced a simplified version of this fascinating industrial process—though manufacturers control their “bubbles” with remarkable precision!
For thicker applications, sheet extrusion employs a flat die to create wider, more substantial sheets used in everything from yogurt containers to construction materials. Both processes showcase the incredible adaptability of extrusion technology.
What makes these films and sheets so useful is their customizability. Need something ultra-thin for delicate food wrapping? No problem. Looking for something sturdier for shipping materials? Extrusion has you covered. From gossamer-thin films measuring just a few microns (thinner than a human hair!) to robust sheets several millimeters thick, extrusion delivers consistent quality at any thickness.
The variety is equally impressive. Your shopping bags might be low-density polyethylene (LDPE), while that clear package showing off a new gadget could be rigid polypropylene (PP). That blister pack protecting your medications? Likely polyvinyl chloride (PVC). Each material brings specific benefits to its application, from clarity to strength to barrier properties.
Food Packaging: Preserving Freshness
Food packaging represents perhaps the most familiar application of extruded plastic films. That wrapper keeping your cheese fresh, the bag protecting your bread from going stale, the film sealing your ready-meal—all are likely products of plastic extrusion.
These aren’t simple wrappings. Modern food packaging films are engineering marvels designed to extend shelf life and maintain food quality. They create barriers against oxygen that would cause spoilage, block moisture that would lead to staleness, and prevent contamination that could cause illness. They do all this while remaining strong enough to withstand shipping and handling, transparent enough to showcase the product, and printable for branding and nutritional information.
The real breakthrough came with co-extrusion—a technique where multiple layers of different plastics are extruded simultaneously. This innovation allows packaging to combine the best properties of various materials. A single seemingly simple film might actually contain an oxygen barrier layer, a moisture barrier layer, and a food-safe contact layer, all bonded together during extrusion.
“Before multi-layer film extrusion, many foods had shelf lives measured in days,” note packaging experts. “Now they can last weeks or months, significantly reducing food waste across the entire food supply chain.”
While plastic packaging has faced environmental scrutiny, the industry continues evolving toward more sustainable solutions. At JianTai Plastic Machinery Company, we’re proud to be part of this evolution through our advanced plastic recycling equipment. Our machines help transform post-consumer films—the very packaging that once protected your groceries—into raw materials for new products, supporting the circular economy and reducing the environmental footprint of these essential materials.
The convenience we enjoy from plastic films and sheets—from grabbing pre-packaged foods to protecting important documents—stems directly from the versatility and efficiency of the extrusion process. As we look toward a more sustainable future, plastic extrusion products will continue evolving, balancing functionality with environmental responsibility.
Window Frames and Doors
Ever walked past a modern home and admired those sleek, low-maintenance windows? Chances are, you were looking at one of the most impressive plastic extrusion products in our everyday environment.
The humble window frame might not seem exciting at first glance, but it represents a genuine revolution in building technology. Before PVC windows became mainstream, homeowners faced a frustrating choice: wooden frames that looked beautiful but needed constant maintenance and could warp or rot, or aluminum frames that conducted heat and cold like a metal popsicle stick.
Enter the extruded PVC profile – a game-changer for the construction industry. The extrusion process creates complex, hollow profiles with internal chambers that trap air and create natural insulation barriers. These aren’t just simple plastic tubes; they’re engineering marvels designed to keep your home comfortable while standing up to decades of weather exposure.
“I installed PVC windows in my home fifteen years ago,” shares one homeowner, “and they still look brand new. No painting, no rot, no problems – just clean them occasionally and they’re good to go.”
The benefits go well beyond just convenience. These extruded frames resist weathering and corrosion, never need painting, reduce outside noise, and cost less than many alternatives. Plus, the design flexibility means architects and homeowners can choose from various styles to match any aesthetic.
Perhaps most telling is this fact: extruded vinyl siding and windows now feature in over half of all new home construction. That’s not just a trend – it’s a fundamental shift in how we build.
Energy-Saving Building Materials
If you’ve ever stood near an old, poorly insulated window during winter, you know exactly why energy efficiency matters. The cold radiates inward, creating that uncomfortable “cold zone” that forces your heating system to work overtime.
PVC window frames made through extrusion solve this problem brilliantly. These frames can reduce heat transfer by up to 70% compared to standard aluminum frames without thermal breaks. When you consider that buildings account for roughly 40% of energy consumption in developed countries (with heating and cooling being the biggest energy hogs), the impact becomes clear.
Modern extrusion technology has taken window design to new levels of sophistication. Today’s profiles feature multi-chamber designs that maximize thermal performance, co-extruded gaskets built right into the frame, hidden drainage systems to manage rainwater, and reinforcement channels that ensure structural stability for decades.
At JianTai Plastic Machinery Company, we’re particularly excited about how these building products contribute to the circular economy we support through our recycling equipment. Many PVC window frames are designed with their end-of-life in mind – after serving for 30+ years, they can be processed through recycling equipment like ours and transformed into raw material for new construction products.
“The combination of durability and recyclability makes extruded PVC building materials increasingly sustainable,” as construction experts often note. When products last longer and can be recycled rather than discarded, we reduce the environmental footprint of our buildings dramatically.
This sustainability aspect, coupled with the immediate energy savings from better insulation, makes these seemingly simple plastic extrusion products powerful allies in building a more efficient, comfortable, and environmentally responsible world – one window frame at a time.
Insulated Electrical Wires
Behind the walls of every modern building runs a network of plastic extrusion products that we rarely see but depend on constantly: insulated electrical wires. The plastic coating surrounding electrical conductors represents one of the most critical applications of extrusion technology, directly impacting safety and reliability in power distribution.
Ever wonder how those electrical wires get their colorful protective coatings? It happens through a fascinating process called “over jacketing extrusion.” Picture this: a bare metal wire zips through an extruder die while molten plastic envelops it like a warm blanket, creating a seamless, continuous coating that hardens as it cools. It’s like dipping a strawberry in chocolate, except at industrial speeds sometimes exceeding 3,000 feet per minute!
What makes this process remarkable is the precision required. Even tiny inconsistencies in the insulation thickness could create weak points or compromise electrical properties. Modern wire coating lines maintain incredibly tight tolerances while operating at these breakneck speeds.
The world of wire insulation is surprisingly diverse. PVC serves as the workhorse for general-purpose applications in your home, while cross-linked polyethylene handles higher temperatures in demanding environments. Need flexibility and durability? Thermoplastic elastomers have you covered. Working in extreme conditions? Fluoropolymers like PTFE step up to the challenge. And for spaces where fire safety is paramount, halogen-free compounds reduce smoke and toxicity risks.
Each material brings unique properties to the table, making them suitable for everything from the wiring in your bedside lamp to specialized industrial equipment or the complex electrical systems in your car.
Wire Insulation: Safety First
The primary function of wire insulation isn’t complicated – it keeps electricity where it belongs and away from people and other conductive materials. This simple function prevents countless short circuits, fire hazards, and electrical shocks every day.
But good insulation does much more than basic electrical isolation. It protects wires from environmental enemies like moisture and harsh chemicals. It provides a shield against physical damage from abrasion and impact. Many insulation materials include flame retardant properties to stop fires from spreading along wires. The colorful coatings also serve as a practical color-coding system that helps electricians identify wires quickly and safely.
“The evolution of extruded wire insulation has enabled the miniaturization of electronics and the development of increasingly complex electrical systems,” notes electrical engineering experts. “Without advances in extrusion technology, many modern devices would simply be impossible to produce.”
The extrusion process gives manufacturers remarkable control over insulation thickness and composition. This precision ensures compliance with rigorous safety standards established by organizations like Underwriters Laboratories (UL) and the International Electrotechnical Commission (IEC).
At JianTai Plastic Machinery Company, we understand the importance of material quality in safety-critical applications like wire insulation. Our Ultimate Guide to Plastic Extruder Screw Selection highlights how proper screw design affects material processing quality—a crucial consideration for manufacturers of insulated wires and cables.
From the tiniest circuits in your smartphone to massive power transmission cables spanning miles, extruded wire insulation exemplifies how plastic extrusion products quietly enable the technological infrastructure we rely on daily. These humble plastic coatings might not be visible most of the time, but they’re working around the clock to keep our modern world powered safely and reliably.
Plastic Bottles and Drinking Straws
That water bottle in your gym bag or the straw in your favorite smoothie? They’re both plastic extrusion products that touch our lives daily. While we often take these items for granted, the journey from raw plastic pellets to finished products showcases the incredible versatility of extrusion technology.
The humble plastic bottle begins its life as an extruded tube called a “parison” or “preform.” Think of it as the bottle’s embryonic stage – a thick-walled tube created through extrusion. These preforms then move to blow molding equipment where they’re stretched and inflated inside a mold, much like a glassblower would shape molten glass, but with precision engineering controlling every aspect. This combined process, extrusion blow molding, marries the efficiency of continuous extrusion with the detailed shaping capabilities of blow molding.
Drinking straws follow a more straightforward path. They emerge from the extruder as continuous tubes that are simply cut to length after cooling. Have you ever wondered how straws get that bendy section? During extrusion, manufacturers insert a special tool called a mandrel that creates those accordion-like ridges in a specific segment of the straw. This simple innovation makes the straw flexible while maintaining its hollow channel.
The materials chosen for these products are as specialized as their uses. Crystal-clear PET (polyethylene terephthalate) gives water bottles their transparency and excellent barrier properties. Your milk jug’s distinctive cloudy appearance comes from HDPE (high-density polyethylene), selected for its strength and food safety. Bottle caps and most straws use polypropylene (PP) for its flexibility and resistance to cracking, while some disposable cups and straws are made from polystyrene (PS).
Sustainable Choices with Plastic Extrusion Products
The convenience of plastic bottles and straws has undeniably changed how we consume beverages, but this convenience has environmental consequences that have sparked important conversations and innovations throughout the industry.
Today’s plastic extrusion products are evolving to address these environmental concerns. Manufacturers have dramatically reduced material usage by designing bottles with thinner walls that maintain strength while using less plastic. Many water bottles now contain significant percentages of recycled PET (often called rPET), sometimes up to 100%, giving new life to previously used plastic.
The innovation doesn’t stop there. Biobased plastics derived from renewable resources like sugarcane are entering the mainstream, offering alternatives to petroleum-based plastics. Products are increasingly designed with their end-of-life in mind, making recycling easier and more effective. And of course, the rise of reusable water bottles and straws offers consumers ways to reduce single-use plastic consumption altogether.
At JianTai Plastic Machinery Company, we’re passionate about the recycling side of sustainability. Our technical team often explains that “the challenge with plastic bottles isn’t the material itself, but how we manage it after use. With proper collection and recycling infrastructure, PET bottles can be recycled multiple times, significantly reducing their environmental impact.”
Our plastic recycling machines are specifically engineered to transform post-consumer bottles and other plastic waste into high-quality recycled material for new products. This supports a circular economy where plastics are continuously reused rather than discarded after a single use.
The extrusion process is crucial to this recycling loop. When plastic bottles are collected and processed, they’re typically shredded into flakes. These flakes must be re-extruded to create uniform pellets suitable for manufacturing new products. Our advanced extrusion technology ensures that these recycled materials maintain the quality and consistency needed for high-performance applications.
While environmental concerns about single-use plastics remain valid, the combination of thoughtful design, material innovation, and effective recycling offers a path forward. These approaches can significantly reduce environmental impact while preserving the convenience, safety, and affordability that made these plastic extrusion products so widespread in the first place.
Automotive Components Made with Plastic Extrusion Products
Open the hood of any modern car, peek underneath the dashboard, or run your hand along the door frame—you’ll find plastic extrusion products everywhere. Today’s vehicles contain dozens of extruded plastic components that you might never notice but would certainly miss if they weren’t there.
That sleek weather stripping around your car doors? Extruded plastic. The channels your windows slide in? Extruded plastic. Even the decorative trim that gives your vehicle its finished look comes from the same manufacturing process. Less visible but equally important are fuel lines, wire harness protectors, air conditioning ducts, and windshield wiper components—all made possible through plastic extrusion.
What makes extrusion perfect for automotive applications is its ability to produce continuous profiles with consistent properties. Imagine creating a rubber seal that needs to be exactly the same along the entire perimeter of a door—extrusion delivers this consistency beautifully. Even more impressive is co-extrusion, where multiple materials combine in a single process. Your car’s weather stripping, for instance, might feature a rigid base for mounting with a flexible lip for sealing, all created in one seamless operation.
Automakers choose from a variety of materials for these components. Flexible seals often use thermoplastic elastomers (TPE), while rigid components might be made from polypropylene (PP). Wire insulation typically relies on PVC, and fluid-handling tubes are commonly polyethylene (PE). For parts that need to withstand extreme conditions, engineering plastics like nylon offer exceptional performance.
Benefits of Plastic Extrusion Products in Automotive
The shift toward plastic components in cars isn’t just a manufacturing preference—it delivers real benefits that drivers experience every day.
First and foremost is weight reduction. Plastic parts typically weigh 50-70% less than their metal counterparts. This lightweighting isn’t just about making cars easier to move; it directly impacts fuel economy. For every 10% reduction in vehicle weight, fuel efficiency improves by about 5-7%. In our eco-conscious world, that’s a significant advantage.
The design flexibility of extrusion allows automakers to create complex shapes that would be impossible with metal. This creative freedom leads to innovative solutions for everything from water management to noise reduction. Speaking of noise, plastic components excel at absorbing vibrations and reducing sound transmission, contributing to those whisper-quiet interiors we’ve come to expect in modern vehicles.
Unlike metal parts that rust and corrode, plastic extrusions resist environmental damage, extending the life of critical components. This durability is especially valuable in regions with harsh winters where road salt wreaks havoc on metal parts.
Cost efficiency is another compelling advantage. The continuous nature of extrusion, combined with lower material costs, often makes plastic components more economical than metal alternatives. This savings helps manufacturers deliver better vehicles at competitive prices.
Perhaps most importantly, many extruded plastic components improve safety. Certain plastic profiles are designed to absorb energy during a collision, helping protect passengers in an accident.
At JianTai Plastic Machinery Company, we appreciate how automotive plastic components contribute to sustainability. Many of these parts can be recycled at the end of a vehicle’s life, creating a circular economy where today’s car components become tomorrow’s raw materials. Our recycling equipment helps make this possible, turning automotive plastic waste into valuable resources for new manufacturing.
“Without plastic extrusion technology, meeting modern efficiency and emissions targets would be nearly impossible,” automotive experts often note. As the industry continues its evolution toward electric vehicles and greater sustainability, plastic extrusion products will play an increasingly vital role in automotive innovation.
Decking and Outdoor Furniture
One of the most visible applications of plastic extrusion products in our daily environment is outdoor living spaces. Extruded plastic decking, fencing, and furniture have revolutionized outdoor construction by offering durable, low-maintenance alternatives to traditional wood products.
When you step onto a modern deck that looks like wood but hasn’t faded, warped, or splintered after years in the sun and rain, you’re likely standing on extruded plastic decking. These materials typically combine plastic (often recycled polyethylene) with wood fibers to create what’s known as wood-plastic composite (WPC). The result mimics the warm appearance of natural wood while offering significantly better durability against the elements.
What makes these extruded decking materials so clever is their internal structure. Rather than being solid throughout, most feature hollow or cellular designs that serve multiple purposes. These innovative structures make the boards lighter and easier to handle while providing better insulation against heat and cold. They also dampen sound (no more hollow footsteps!), use less material, and actually improve the overall rigidity of the product.
The versatility of extrusion technology extends far beyond just deck boards. Take a look around any well-appointed backyard, and you’ll likely spot numerous plastic extrusion products – from the fencing panels providing privacy to the pergola offering shade. The railing systems, garden edging, planters, and even components of playground equipment often begin their life in an extruder.
Outdoor furniture frames made from extruded plastic offer the look of painted wood or metal without the maintenance headaches. These pieces can withstand summer thunderstorms and winter snow without deteriorating, making them practical investments for homeowners tired of replacing weather-damaged furniture every few seasons.
Durable and Low-Maintenance Solutions
The magic of extruded plastic outdoor products lies in their exceptional durability and minimal maintenance requirements. While your neighbor might spend weekends staining and sealing their wooden deck, you can simply enjoy yours with just an occasional cleaning.
Weather resistance is perhaps the most appreciated quality of these materials. Rain, snow, intense sunlight, and temperature swings that would cause wood to deteriorate over time barely affect quality extruded products. The plastic components resist moisture that would otherwise lead to rot, and many incorporate UV stabilizers that prevent the fading and degradation that sun exposure typically causes.
Say goodbye to insect problems too. Unlike wood decking that can become an all-you-can-eat buffet for termites and other wood-boring pests, plastic materials hold no appeal for these destructive critters. This elimination of a major cause of structural deterioration adds years to the lifespan of your outdoor installations.
Parents and pet owners particularly appreciate the safety benefits of plastic decking. No more splinters in little hands or paws! The smooth, consistent surface created through the extrusion process eliminates this common hazard of traditional wood decking.
The impressive longevity of these products speaks volumes – many quality extruded decking products carry warranties of 25 years or more. When a manufacturer is willing to stand behind their product for a quarter-century, you know it’s built to last.
At JianTai Plastic Machinery Company, we see outdoor applications as a perfect example of the circular economy in action. Many decking and outdoor furniture products incorporate recycled plastic, giving new purpose to materials that might otherwise end up in landfills. These applications are particularly well-suited for recycled content because they can use mixed plastic streams that might be challenging to recycle into more demanding applications.
The sustainability story gets even better when you consider the end-of-life scenario. After decades of service, when your extruded plastic deck or furniture eventually needs replacement, the material can often be recycled again. This further extends the lifecycle of the plastic and reduces environmental impact, creating a truly circular solution.
For homeowners looking to create beautiful, functional outdoor spaces that stand the test of time while minimizing maintenance headaches, extruded plastic decking and furniture represent one of the smartest investments available today.
Sports Equipment Components
The sporting goods industry has acceptd plastic extrusion products in ways that touch virtually every athlete and weekend warrior. Look closely at your favorite sports gear, and you’ll likely find extruded plastic components that improve your performance, comfort, and safety without calling attention to themselves.
From the comfortable grip on your tennis racket to the lightweight frame of your snowshoes, extruded plastic components work silently behind the scenes. These components might not get the glory, but they’re often what makes modern sports equipment so much better than what athletes used decades ago.
Tennis players benefit from racket handles with precisely designed ergonomics. Skiers and snowboarders rely on protective edge guards that shield their equipment from damage. Hikers appreciate the lightweight yet incredibly durable framework of modern snowshoes. Even fishing enthusiasts depend on rod components made through extrusion processes.
The magic of extrusion technology for sports equipment lies in its versatility. Manufacturers can create complex cross-sections that vary in thickness exactly where needed for optimal performance. The consistency of the extrusion process ensures that every piece has identical properties – critical when athletes depend on predictable equipment performance.
Plastic extrusion products shine in sports applications because they can be precisely engineered for specific needs. Need a grip that remains tacky when wet? A thermoplastic elastomer with specific additives can be extruded to create just that. Looking for a structural component that flexes in one direction but remains rigid in another? A carefully designed extrusion profile can deliver exactly those properties.
The materials chosen for sports equipment are as specialized as the athletes who use them. Soft, grippy thermoplastic elastomers provide secure handling on rackets and exercise equipment. Durable polyethylene creates structural elements that withstand years of abuse. Rigid polypropylene delivers consistent performance in components where flexibility would be a drawback. Engineering plastics stand up to extreme conditions in high-performance applications.
Sports Gear Improved by Plastic Extrusion Products
When you pick up a modern tennis racket or golf club, the comfortable grip that feels like it was made for your hand represents a significant advance in equipment design. Extruded plastic grips with complex profiles fit the human hand naturally, reducing fatigue and improving control. Many feature co-extruded materials that combine a firm inner layer for structural integrity with a soft outer layer for comfort – all created in a single manufacturing process.
“The grip is where the athlete connects with the equipment,” notes sports equipment designers. “Getting that interface right can make the difference between equipment that feels like an extension of the body and equipment that fights against the user.”
Weight reduction represents another major contribution of plastic extrusion to sports performance. Hollow extruded profiles can replace solid materials, dramatically reducing equipment weight while maintaining strength. For endurance athletes, every gram matters – lighter equipment means less fatigue and better performance over time.
The customization possibilities with extruded components have democratized high-performance sports equipment. Manufacturers can create specialized profiles for different sports, skill levels, or even body types. A beginner might use equipment with more forgiving characteristics, while professionals can choose gear optimized for maximum performance at the limits of human capability.
Durability in challenging conditions is another hallmark of modern extruded sports components. Whether facing the relentless sun on a tennis court, salt spray on a fishing boat, or subfreezing temperatures on a ski slope, well-designed extruded plastics maintain their performance characteristics. This environmental resistance translates to equipment that lasts longer and performs more consistently throughout its lifespan.
Safety improvements might be the most important, if least visible, contribution of extruded plastics to sports. Extruded padding and protective elements absorb impact energy more effectively than traditional materials, reducing injury risk in contact sports and during inevitable falls or collisions.
At JianTai Plastic Machinery Company, we understand how material quality affects performance in demanding applications like sports equipment. While our focus remains on recycling technologies, we take pride in knowing that our machines help produce materials that can meet the exacting standards required for performance sports gear. The consistency and purity of recycled materials becomes especially important when they’ll be used in applications where athletes push both themselves and their equipment to the limits.
As sports technology continues to evolve, plastic extrusion products will undoubtedly play an expanding role. New materials, improved processing techniques, and innovative designs will enable the next generation of equipment to be lighter, stronger, more comfortable, and more sustainable – helping athletes at all levels achieve their personal best.
Custom Plastic Profiles in Furniture Design
When you run your hand along the smooth edge of a modern desk or notice the sleek trim on your kitchen cabinets, you’re likely touching plastic extrusion products that have quietly revolutionized furniture design. These custom profiles have become essential components in contemporary furniture, blending seamlessly into designs while offering practical benefits that traditional materials simply can’t match.
Furniture manufacturers have acceptd extruded plastic profiles for countless applications throughout the home and office. Edge banding and trim pieces protect vulnerable particleboard or MDF surfaces, extending furniture life while adding a finished look. Protective corner guards shield furniture from damage in high-traffic areas, while drawer slides created through extrusion ensure smooth operation year after year.
“What makes extruded profiles so valuable in furniture design is their incredible versatility,” explains a senior designer at a leading furniture manufacturer. “We can create virtually any cross-section imaginable, combining different materials and properties in ways that would be impossible with wood or metal alone.”
The material choices for furniture extrusions are just as diverse as their applications. PVC remains popular for edge banding and trim due to its durability and ease of coloring. For structural components that need to withstand heavy use, ABS provides excellent impact resistance. When lightweight, chemical-resistant parts are needed, polypropylene delivers, while thermoplastic elastomers create soft-touch elements that improve comfort and user experience.
Perhaps most exciting for designers is the ability to incorporate transparent or translucent acrylic elements, opening up new possibilities for furniture that plays with light and creates visual interest. These material options can be precisely color-matched to complement any design scheme, ensuring a cohesive look across furniture collections.
Aesthetic and Functional Benefits
The beauty of extruded profiles in furniture goes far beyond simple decoration. These components solve practical problems while enhancing visual appeal – a rare combination in the design world.
From a design perspective, extrusion technology has broken down barriers that once limited furniture aesthetics. Complex cross-sections that would require extensive machining in wood or metal can be produced consistently and economically through extrusion. This design freedom allows furniture makers to create distinctive visual signatures that set their products apart in a competitive market.
Material efficiency represents another significant advantage. Hollow profiles reduce weight and material usage while maintaining structural integrity – a win for both sustainability and the bottom line. This efficiency extends to manufacturing processes as well, with extruded components often eliminating multiple assembly steps.
Smart furniture designs now incorporate profiles with integrated functionality – channels that neatly manage cables in office furniture, mounting features that simplify hardware installation, or interlocking elements that make assembly intuitive. These thoughtful details improve the user experience while differentiating premium furniture from basic alternatives.
The durability of plastic profiles addresses practical concerns that have long plagued furniture owners. Unlike wood edges that can chip or peel, quality extruded trim resists moisture damage, chemical exposure, and the inevitable bumps that occur in active homes and workplaces. This resilience helps furniture maintain its appearance and functionality for years longer than traditional alternatives.
For manufacturers, the consistency of extruded components provides a significant advantage. Each profile emerges from the extrusion process with identical dimensions and properties, eliminating the variations inherent in natural materials. This precision facilitates quality control and ensures that furniture assembles correctly every time.
At JianTai Plastic Machinery Company, we see the furniture industry as an excellent example of how plastic extrusion contributes to both innovation and sustainability. Many furniture profiles now incorporate recycled content, creating beautiful, functional pieces that support environmental goals while meeting exacting design standards.
As furniture continues evolving toward modular designs, personalization options, and sustainable materials, plastic extrusion products will play an increasingly important role. The flexibility of extrusion technology perfectly complements these trends, enabling furniture that adapts to changing lifestyles while maintaining the quality and aesthetics consumers demand.
Frequently Asked Questions about Plastic Extrusion Products
What is plastic extrusion and how does it work?
Ever wondered how that perfect plastic pipe in your bathroom or the window frame in your living room came to be? It’s all thanks to plastic extrusion – a fascinating manufacturing process that transforms raw plastic into the countless products we use daily.
Think of plastic extrusion like a sophisticated play-dough machine for grown-ups. The process begins with plastic material – usually tiny pellets or granules – being fed into a machine called an extruder. These pellets might be mixed with special additives like colorants or UV stabilizers to give the final product specific properties.
Once inside the extruder, magic happens! A powerful rotating screw pushes the plastic forward through a heated barrel. As it moves, the plastic melts into a smooth, flowing material – imagine butter melting in a hot pan, but with much more precision. The heat comes both from the friction created by the screw and from external heaters wrapped around the barrel.
“The change of solid plastic pellets into a perfectly formed profile is really a marvel of modern manufacturing,” notes our engineering team at JianTai Plastic Machinery Company. “It’s a perfect balance of heat, pressure, and precision timing.”
As the molten plastic continues its journey, it passes through filters that remove any unwanted particles – because nobody wants contamination in their final product! Then comes the crucial moment: the plastic enters a specially designed die, which is essentially a metal plate with an opening shaped exactly like the cross-section of the product being made.
When the plastic exits the die, it needs to cool quickly to maintain its new shape. This typically happens in a water bath or with cooling rolls. As it cools, the now-solid plastic is gently pulled along at a controlled speed to ensure it maintains the perfect dimensions. Finally, depending on the product, the continuous extrusion is either cut to specific lengths (like pipes) or wound onto large reels (like wire insulation).
The beauty of this process is that it never stops – it’s continuous manufacturing at its finest, making it incredibly efficient for producing large volumes of plastic extrusion products.
What materials are commonly used in plastic extrusion?
Not all plastics are created equal, especially when it comes to extrusion. The process primarily uses thermoplastics – materials that can be repeatedly melted and solidified without breaking down, unlike that casserole dish that would crack if you tried to melt it.
The most versatile player in the extrusion world is polyethylene (PE). Available in different densities from low (LDPE) to high (HDPE), this plastic superstar creates everything from grocery bags to sturdy water pipes. Its flexibility and resistance to chemicals make it perfect for countless applications.
When durability and weather resistance are priorities, polyvinyl chloride (PVC) steps into the spotlight. Those white pipes under your sink? Likely PVC. Your home’s window frames and siding? Often PVC too. It’s the tough, long-lasting choice that stands up to the elements.
For products that need to resist chemicals and maintain their shape, polypropylene (PP) is the go-to material. From food containers to automotive parts, PP delivers reliability with a lighter weight than many alternatives.
Other common extrusion materials include polystyrene (PS) for packaging and disposable items, acrylonitrile butadiene styrene (ABS) for products needing impact resistance, and polyethylene terephthalate (PET) – the clear plastic used for water bottles and food packaging.
For applications requiring both plastic-like processing and rubber-like flexibility, thermoplastic elastomers (TPEs) bridge the gap. These materials create comfortable grips on tools, flexible seals on containers, and soft-touch surfaces on countless products.
When extreme performance is needed, engineering plastics like nylon, polycarbonate, and PEEK enter the picture. Though they require higher processing temperatures, these materials deliver exceptional strength and heat resistance for demanding applications.
For more detailed information about plastic materials and their specific properties, the Plastic Materials resource provides excellent insights.
At JianTai Plastic Machinery Company, we’re particularly interested in how these materials can be recycled and reused. Our recycling equipment helps transform used plastic extrusion products back into raw materials, supporting a more sustainable future for the plastics industry.
How can plastic extrusion be customized to meet specific product requirements?
The remarkable versatility of plastic extrusion comes from its almost endless customization possibilities. It’s like having a blank canvas where manufacturers can create products perfectly suited to specific needs.
The most fundamental customization starts with the die – the metal plate that shapes the molten plastic. Die designs can range from simple circles for pipes to incredibly complex shapes with multiple hollow sections, varying wall thicknesses, and intricate details. With modern CNC manufacturing, the possibilities are virtually limitless.
Material selection offers another powerful customization avenue. Need a product that won’t fade in sunlight? Add UV stabilizers to the plastic mix. Looking for fire resistance? Incorporate flame retardant additives. Want to improve strength? Mix in glass fibers or other reinforcing materials. Even the color, texture, and flexibility can be precisely custom through material choices.
“What makes extrusion truly special is how we can fine-tune every aspect of the process to achieve exactly what our customers need,” explains our technical team. “From the molecular structure of the plastic to the final dimensions of the product, everything can be optimized.”
One of the most impressive customization techniques is co-extrusion, where multiple extruders feed different materials into a single die. This creates products with multiple layers or sections, each with different properties. Imagine a window seal with a rigid base for mounting and a soft, flexible edge for weather protection – all created in a single pass through the extruder. Co-extrusion makes this possible.
Even after the basic extrusion process, plastic extrusion products can be further customized through secondary operations. These might include printing information directly onto the surface, cutting to precise lengths, drilling holes, adding texture, or bending into specific shapes.
For some applications, the extrusion process deliberately stretches the plastic as it exits the die. This orientation aligns the polymer molecules in specific directions, significantly enhancing strength – similar to how pulling taffy aligns its structure and changes its properties.
At JianTai Plastic Machinery Company, we understand that customization extends to the recycling process as well. Our equipment is designed to handle diverse plastic waste streams and produce recycled materials that meet exacting specifications – from basic applications to demanding technical products that require consistent, high-quality raw materials.
This incredible flexibility explains why extrusion remains the preferred manufacturing method for countless plastic extrusion products that surround us daily – from the simplest drinking straw to complex automotive components with multiple materials and precise tolerances.
Conclusion
The world of plastic extrusion products surrounds us in ways most of us never notice. From the pipes delivering clean water to our homes to the tiny medical tubes saving lives in hospitals, these products quietly support our modern lifestyle.
What makes plastic extrusion truly special is its incredible versatility. Think about it – the same basic process of melting plastic and pushing it through a shaped opening creates everything from paper-thin food wrap to sturdy window frames. This simple yet ingenious manufacturing method has become the backbone of countless industries because it combines precision with efficiency.
Throughout our journey exploring these products, we’ve seen how extruded plastics offer remarkable advantages in our everyday lives. They maintain consistent quality across thousands of identical pieces. They can be formed into complex shapes that would be impossible with other materials. Many use hollow designs that save material while maintaining strength. They resist weather, chemicals, and time better than many alternatives. And perhaps most importantly for manufacturers, they can be produced continuously at high volumes, keeping costs reasonable.
At JianTai Plastic Machinery Company, we’re particularly passionate about the sustainability aspect of plastic extrusion. Our home in Yuyao City, Zhejiang Province, has become a hub for developing technologies that give plastic a second life. Our Plastic Recycling Machines transform what might have been waste into valuable raw materials for new products, completing the circle of plastic’s lifecycle.
The future looks bright for plastic extrusion products as the industry accepts sustainability challenges. We’re seeing exciting developments like decking made from recycled shopping bags, pipes incorporating plant-based materials, and product designs specifically engineered for easy recycling at the end of their useful life. Manufacturers are also finding ways to use less energy during production and create products that last longer before needing replacement.
Next time you notice a plastic window frame, garden hose, or food container, take a second to appreciate the remarkable journey it took from raw material to finished product. These everyday items represent the perfect marriage of scientific innovation and practical engineering – small miracles of modern manufacturing that make our lives better in countless ways.
The world of plastic extrusion products may not be glamorous, but it’s certainly worth understanding. After all, these products touch almost every aspect of our daily lives, quietly providing solutions we’ve come to depend on without a second thought.