Внесите некоторые изменения в окружающую среду
-
Здание 3, Wanyang Innovation City, улица Langxia, город Юйяо, провинция Чжэцзян
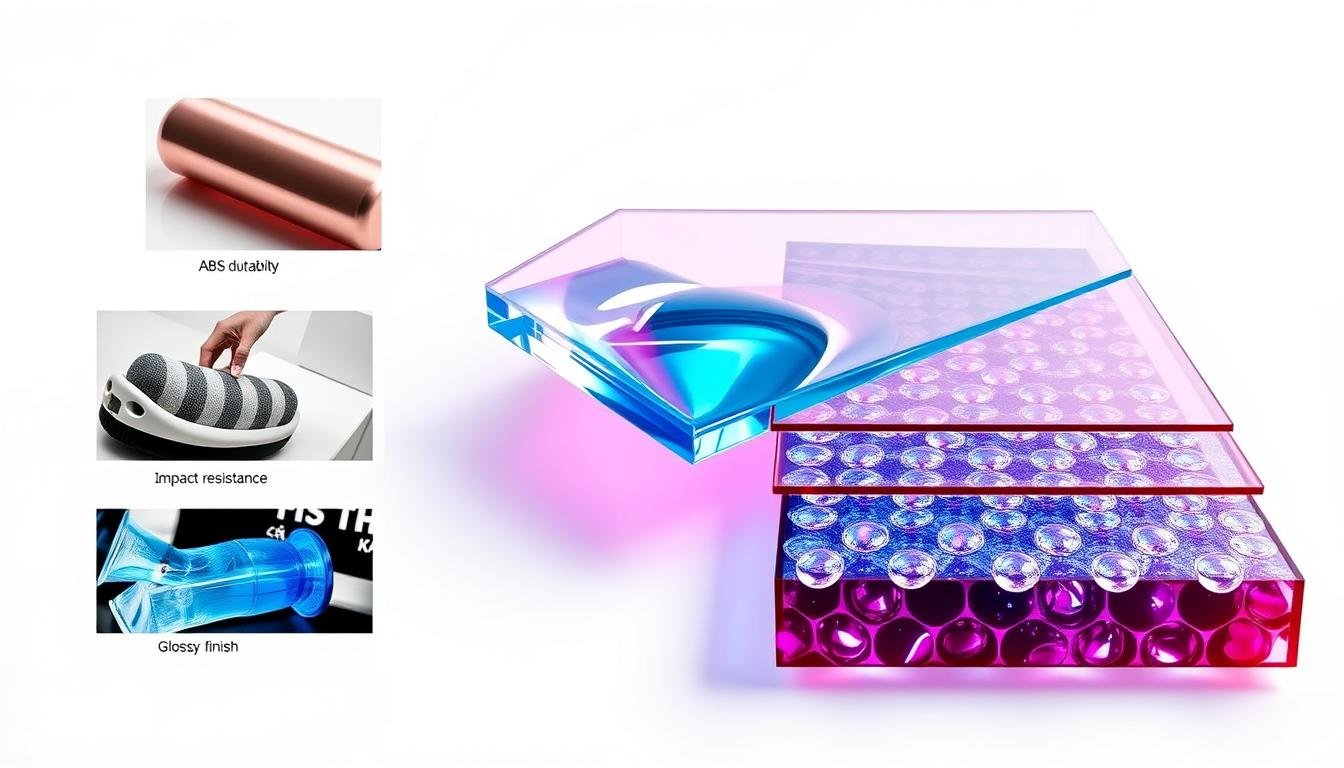
Понимание сущности материала ABS-пластика
Вы когда-нибудь задумывались, почему кирпичики LEGO идеально собираются, а приборная панель вашего автомобиля сияет? Секрет в том. Акрилонитрил Бутадиен Стирол (ABS). Этот полимер повсюду в нашем современном мире благодаря своим удивительным свойствам. Но что делает его таким особенным для таких отраслей промышленности, как 3D-печать и автомобилестроение?
Введение в АБС: Универсальный термопласт
АБС-пластик отличается сочетанием прочности и внешнего вида, меняя способы изготовления предметов. Он плавится при температуре всего 221 градус по Фаренгейту, что делает его отличным материалом для литья под давлением и 3D-печать1. Это открывает двери для творчества во многих областях.
Его экономичность и способность принимать различные цвета и отделку привлекают многих производителей. Помимо прочности, ABS также безопасен для контакта с пищевыми продуктами, что свидетельствует о его широком применении за пределами того, что мы видим.2.
Основные выводы
- АБС-пластик низкая температура плавления улучшает способность к формованию для различных приложения1.
- Экономия средств, охрана окружающей среды устойчивое развитиеНетоксичность характеризует широкое применение АБС в различных отраслях промышленности1.
- Прочный, ударостойкий АБС может быть изменен в процессе производства, играя как функциональную, так и декоративную роль1.
- Оптимальный диапазон рабочих температур и низкий коэффициент усадки делают ABS достойным внимания при создании пресс-форм.3.
- Несмотря на преимущества, не поддающийся биологическому разложению ABS и энергоемкое производство ставят под сомнение его воздействие на окружающую среду3.
Введение в АБС: Универсальный термопласт
термопластик ABS не только потому, что хорошо выглядит, но и потому, что хорошо работает во многих областях. Он прочен и может использоваться при обработке на станках с ЧПУ, литье под давлением и 3D-печать. Это делает его востребованным материалом для многих производственных проектов.
ABS является лучшим выбором не только благодаря своей прочности, но и потому, что он бюджетный. Это очень удобно для компаний, следящих за своими расходами. Он пользуется популярностью в различных областях, таких как автомобили и гаджеты, поскольку хорошо сочетает в себе стоимость и качество.4.
Если говорить о долговечности, то ABS выдерживает температуру от 70 до 80 градусов Цельсия, не разрушаясь. Кроме того, он имеет прочность на разрыв от 35 до 50 мегапаскалей. Это означает, что он идеально подходит для мест, где требуется, чтобы материалы служили долго в сложных условиях.5.
Различные типы ABS, такие как General-Purpose или Flame-Retardant, демонстрируют его гибкость. Благодаря этому он отлично подходит для любых целей - от деталей самолетов до пищевого оборудования. Эти варианты помогают удовлетворить различные потребности, доказывая универсальность ABS5.
ABS также играет ключевую роль в производстве, когда речь идет о гальваническом покрытии. Он работает с такими металлами, как медь и золото, для нанесения гальванического покрытия. Это повышает его устойчивость к ржавчине и улучшает внешний вид. Этот шаг жизненно важен для изделий, которые должны оставаться красивыми и долговечными.
С точки зрения экологии ABS также является победителем. Его можно перерабатывать, а значит, он поддерживает экологически чистое производство. Эта особенность помогает промышленности быть более экологичной за счет повторного использования материалов для новых продуктов. Это говорит о том, что ABS - разумный и экологичный выбор материала.46.
термопластик ABS играет широкую и активную роль в промышленности. Он специально разработан для удовлетворения требований различных рабочих пространств. ABS продолжает доказывать, что является ключевым игроком в производстве.
Состав и полимеризация АБС
Акрилонитрил Бутадиен Стирол (ABS) обладает уникальными свойствами благодаря своим компонентам. Эти компоненты смешиваются между собой особым образом. Мы рассмотрим роли акрилонитрил, бутадиен, и стирол. Каждая деталь является ключевой для придания ABS прочности и гибкости.
Акрилонитрил: Обеспечение химической стойкости
Акрилонитрил придает АБС стабильность и устойчивость к химическим веществам. Его прочная структура противостоит различным химическим веществам. Это делает АБС идеальным материалом для изделий, которые должны оставаться прочными под воздействием тепла и давления. Примерно от 15% до 35% АБС состоит из акрилонитрила. Это помогает ему хорошо соединяться со стиролом и сохранять стабильность полимера.7.
Бутадиен: Повышение вязкости и ударной вязкости
Бутадиен, составляющий от 5% до 30% в ABS, делает его устойчивым к повреждениям. Он придает гибкость и прочность, позволяя ABS выдерживать удары и не ломаться7. Бутадиен помогает ABS хорошо работать при температурах от -20 до 80 °C (от -4 до 176 °F). Это качество важно для многих изделий7.
Стирол: Вклад в жесткость и эстетику
Стирол формирует от 40% до 60% из ABS, придавая жесткость и блестящий вид. Он позволяет создавать точные и детализированные конструкции7. При использовании стирола изделия получаются высококачественными, простыми в изготовлении и гладкими8.
Процесс изготовления ABS включает в себя тщательное перемешивание и сохранение целостности молекул. Плотность зерен ABS составляет от 1,060 до 1,080 г/см3. Такая плотность является ключевой для создания детализированных изделий, таких как 3D-печати.7.
АБС также легко обрабатывается, что делает его фаворитом в производстве. Такие методы, как литье под давлением и обработка на станках с ЧПУ, позволяют создавать из ABS детали для различных целей.8.
Сочетание акрилонитрила, бутадиена и стирола в ABS помогает ему сохранять прочность в различных условиях. Благодаря такой совместной работе ABS отлично подходит для многих изделий, сочетая в себе эксплуатационные характеристики и привлекательный внешний вид.9.
Отличительные свойства АБС-пластика
ABS-пластик широко используется во многих отраслях промышленности, таких как автомобильная и бытовая электроника. Это связано с его ключевыми физическими характеристиками. В частности, его низкая температура плавления и высокая прочность на разрыв выделяют его среди других. Эти качества подчеркивают его роль в качестве прочный полимер.
Низкая температура плавления для облегчения формовки
Известен своими низкая температура плавленияАБС-пластик плавится при температуре от 200 до 240 градусов Цельсия (392-464 градуса по Фаренгейту). Это свойство позволяет легко обращаться с ним в производственные технологии например, литье под давлением и 3D-печать10. Благодаря низкая температура плавленияABS может принимать замысловатые формы, сохраняя при этом свое качество и внешний вид.
Высокая прочность на разрыв и долговечность
АБС прочность на разрыв садится при давлении от 35 до 50 мегапаскалей (МПа)10, отмечая его как прочный полимер. Высокий прочность на разрыв Это означает, что ABS остается прочным даже при больших нагрузках. Он также сохраняет свои механические свойства при температуре от 70 до 80 градусов Цельсия (от 158 до 176 градусов по Фаренгейту) без каких-либо значительных изменений10что повышает его долговечность.
Отличная устойчивость к ударам и сотрясениям увеличивает срок службы ABS. Это означает, что изделия, изготовленные из ABS, прочны и долговечны даже в сложных ситуациях10.
С этими Свойства ABSПоэтому понятно, почему он незаменим во многих изделиях, которые мы используем каждый день. От автомобильных салонов до крышек электронных устройств - ABS сочетает в себе свойства, редко встречающиеся в других материалах. Его постоянный рост и универсальность в различных областях позволяют ему занимать важное место в производстве.
Промышленное применение ABS пластика
ABS-пластик невероятно универсален и долговечен. Он используется во многих областях, от повседневных предметов до специфических промышленных нужд. Он особенно распространен в автомобилестроении и бытовая электроника. ABS выбирают за его термостойкость, прочность и способность хорошо выглядеть. Эти качества делают его очень полезным во многих областях применения11.
Автомобили: От бамперов до компонентов приборной панели
В автомобилях ABS помогает сделать их легче, улучшая пробег. Он используется в бамперах, приборных панелях и внутренних деталях. Эти детали прочные, но легкие. Благодаря этому автомобили весят меньше, потребляют меньше бензина и меньше загрязняют окружающую среду.11.
Автомобильные детали, изготовленные из ABS, отвечают потребностям людей в прочных, но экономичных транспортных средствах. Это поддерживает движение в сторону создания автомобилей, более дружественных к планете11.
Бытовая электроника: Прочные корпуса и детали
Компании, производящие электронику, используют ABS, потому что он прочный и хорошо изолирует. Из него делают прочные корпуса, клавиатуры и другие детали. ABS не позволяет гаджетам легко ломаться. Они отлично выглядят и работают.11.
Его способность придавать точную форму и при этом быть прочным ценится очень высоко. Это делает его лучшим выбором для многих электронных товаров11.
Применение ABS в промышленности демонстрирует его гибкость и эффективность в различных условиях и при различных потребностях. Он играет важнейшую роль в производстве деталей автомобилей и электронных устройств. Его прочность и универсальность способствуют инновациям и эффективному производству продукции11.
Что такое ABS пластик материал
Акрилонитрил-бутадиен-стирол, известный как ABS, представляет собой термопластик ABS. Это непросто полимерная смесь который повышает производственное оборудование. Этот материал сочетает в себе прочность полибутадиенового каучука с прочностью и жесткостью акрилонитрила и стирола. ABS создается путем полимеризации стирола и акрилонитрила с полибутадиеном12.
ABS обладает такими особыми свойствами, как высокая ударопрочность и прочность. Эти качества делают его идеальным для многих областей применения. Его можно встретить в автомобилях, электронике и музыкальных инструментах. Его гибкость широко распространена во многих областях1213.
Также, термопластик ABS Хорошо переносит экстремальные температуры. Это делает его идеальным для изделий, используемых в различных условиях. Его долговечность и производительность делают его лучшим выбором для производителей12.
Однако ABS не идеален. Он плохо переносит атмосферные воздействия и некоторые химические вещества. Эти недостатки ограничивают его применение в некоторых областях12.
Недвижимость | Деталь | Приложения |
---|---|---|
Прочность на разрыв | Высокий | Автомобильные запчасти, защитное снаряжение |
Устойчивость к ударам | Превосходно | Спортивное оборудование, защитные шлемы |
Температурные характеристики | Высокие и низкие | Приборы, подвергающиеся воздействию переменных температур |
Формоустойчивость | Высокий | 3D-печать, изготовление корпусов на заказ |
Устойчивость к коррозии | Хорошо противостоит распространенным химическим веществам | Трубы, фитинги в строительстве |
Хотя ABS стоит дороже, чем такие материалы, как полистирол или полиэтилен, его лучшие качества уравновешивают цену. Его выбирают для задач, требующих прочности, жесткости и внешнего вида. Кроме того, его переработка и возможность формования обеспечивают экологические и экономические преимущества1214.
Преимущества АБС-пластика в производстве
АБС-пластик отлично подходит для производства благодаря своим уникальным свойствам. Это инъекционный полимер Это хорошо работает во многих отраслях.
Подходит для литья под давлением и 3D-печати
АБС-пластик плавится при температуре 204-238°C (400-460°F), идеально подходящей для точного формования15. Его превосходная текучесть позволяет изготавливать детальные и сложные детали. АБС можно плавить и изменять форму много раз без потери качества, что очень удобно для 3D-печати.15.
Этот полимер прочен и гибок, что позволяет создавать новые конструкции и индивидуальные решения в производстве. Он позволяет создавать действительно индивидуальную отделку.
Адаптация к различным цветам и отделкам
Производители любят ABS-пластик за его настраиваемая отделка. Он может быть выполнен в разных цветах без потери прочности и долговечности. Это очень важно для потребительских товаров, для которых внешний вид так же важен, как и функциональность. АБС также хорошо противостоит истиранию и образованию пятен, сохраняя товарный вид на протяжении долгого времени.16.
Недвижимость | Значение | Влияние на производство |
---|---|---|
Температура литья под давлением | 204 - 238 °C (400 - 460 °F) | Обеспечивает высокую точность и повторяемость15. |
Устойчивость к ударам | 46 МПа (6600 PSI) | Идеально подходит для высоких нагрузок приложения16. |
Настраиваемая отделка | Высокий | Обеспечивает универсальность дизайна и привлекательность на рынке. |
Температура теплового отклонения | 98 °C (208 °F) при 0,46 МПа (66 PSI) | Сохраняет целостность структуры при умеренном нагреве16. |
Понимание поведения ABS при плавлении
Способ плавления ABS играет ключевую роль в его производстве и переработке. Он размягчается при температуре от 105 до 115°C (221-239°F), но не плавится резко. Это упрощает несколько этапов производства17.
Влияние на технологии производства
ABS плавится при температуре от 200 до 250°C, что делает его популярным на заводах18. Его низкая температура плавления облегчает обработку и снижает энергопотребление в таких технологиях, как литье под давлением и 3D-печать. Для литья под давлением температура АБС в бочке составляет 220-250°C, в то время как форма остается более холодной при температуре 40-60°C.1719.
Последствия для переработки и повторного использования ABS
ABS можно нагревать и придавать новую форму без потери прочности при температуре около 85°C, что очень удобно для повторного использования17. Это свойство помогает при переработке ABS, обеспечивая его длительное использование. Это не только полезно для планеты, но и сокращает расходы, вписываясь в цикл повторного использования пластмасс.
Сайт поведение при плавлении АБС влияет на способ его производства и переработки, что позволяет производителям использовать его в качестве экологически безопасного варианта.
Сравнение АБС с другими пластиками: Аналитический подход
В мире пластмасс знание различий между ABS, PC и PP имеет ключевое значение. Эти знания помогают принимать лучшие решения для проектов. Кроме того, оно помогает выбрать пластик для конкретного применения.
Прочность ABS варьируется в пределах 68-118 МПа. Он подходит для различных целей, например, для изготовления деталей автомобилей и гаджетов.20. Диапазон прочности ПК составляет 58,6-154 МПа. Его выбирают для изделий, которые должны быть прозрачными и выдерживать сильные удары, например, для безопасного стекла.20.
Когда речь заходит об экономии денег, ABS имеет преимущество. Его гранулы стоят около $0,90 за килограмм. По сравнению с гранулами из ПК по цене $1,52 за килограмм и гранулами из ПП по цене $1,20 за килограмм.20. Для любителей 3D-печати ABS также является более бюджетным вариантом. Цена на его катушку составляет около $20 за килограмм.20.
Если рассматривать экологичность, то ABS и PC относятся к RIC 7. Это означает, что их сложнее перерабатывать. Но их можно многократно перерабатывать без потери качества. Это свидетельствует о стремлении быть более экологичными20.
Недвижимость | ABS | ПК | PP |
---|---|---|---|
Температура теплового прогиба (°C) | 100 | 140 | 100 |
Стоимость за килограмм ($) | 0.90 | 1.52 | 1.20 |
Категория утилизации | RIC 7 | RIC 7 | RIC 5 |
Несмотря на то, что ABS может лидировать не во всех областях, его доступная цена, высокая прочность и способность к переработке. Эти качества позволяют использовать его для создания прототипов и других целей.2021.
Решение проблем с помощью материала ABS
Материал ABS популярен во многих отраслях промышленности. Однако он сталкивается с такими проблемами, как чувствительность к ультрафиолету и слабая устойчивость к растворителям. Чтобы улучшить его, специалисты в области химической инженерии и дизайна работают не покладая рук. Они стремятся сделать АБС еще более совершенным для новых применений.
Преодоление чувствительности к ультрафиолету
Пластик ABS плохо переносит воздействие ультрафиолетовых лучей. Такое воздействие может ослабить его, привести к изменению цвета и потере прочности. Чтобы исправить ситуацию, производители добавляют УФ-стабилизаторы во время создания22. Эти добавки защищают ABS от ультрафиолетового излучения22.
Это умное решение позволяет сохранить прочность ABS надолго. Кроме того, оно позволяет без опасений использовать изделия из ABS на улице.
Устранение плохой устойчивости к растворителям
Слабая защита ABS от растворителей является проблемой. Его нельзя использовать там, где часто встречаются химические вещества. Но есть решение: специальные покрытия22. Они защищают ABS от агрессивных растворителей, делая его более универсальным.
Вызов | Вмешательство | Выгода |
---|---|---|
Чувствительность к ультрафиолету | УФ-стабилизаторы | Возможность использования на открытом воздухе и сохранение цвета |
Бедный Устойчивость к растворителям | Химически стойкие покрытия | Повышенная долговечность в химических средах |
Эти изменения помогут ABS удовлетворить потребности современных отраслей промышленности22. Он также открывает двери для новых применений, благодаря своим улучшенным характеристикам22.
Будущее ABS в инновациях 3D-печати
ABS постоянно развивается в мире 3D-печати. Известный своей прочностью и способностью противостоять ударам, он становится еще лучше. Инновации повышают его универсальность в 3D-печати23. Такие свойства, как прочность и стабильность, улучшаются за счет добавления таких веществ, как графен.23. Это открывает новые возможности для использования ABS благодаря его улучшенным качествам23.
3D-печать позволяет легко изготавливать изделия из ABS. Сюда входят сложные детали автомобилей и медицинские инструменты, изготовленные на заказ23. Автомобильный сектор использует ABS благодаря его легким, но прочным свойствам для создания таких инновационных вещей, как держатели аккумуляторов.23. Здравоохранение также получает преимущества, поскольку ABS используется для изготовления протезов.23.
ABS хорошо сочетается с технологиями 3D-печати. Для оптимальной печати ему требуется температура от 220 до 250 °C.24. Такой диапазон температур помогает создавать прочные и гладкие отпечатки, подходящие для прототипов и конечных продуктов.24. Более того, новые технологии переработки позволяют не только повторно использовать ABS, но и модернизировать его для различных производственных нужд.23.
В Северной Америке использование ABS в 3D-печати растет. Такие компании, как BASF и GE Plastics, добиваются успехов в использовании этого материала.25. Они расширяют границы применения ABS для различных целей.25. Инновации, представленные здесь, свидетельствуют об изменениях на рынке, вызванных технологиями, которые делают ABS еще более универсальным в 3D-печати.25.
В будущем ABS будет усовершенствована для повышения пожарной безопасности, электропроводности и экологичности.23. Эти усовершенствования закрепят его роль в будущем 3D-печати и в более широком применении. По мере роста спроса на АБС все большее внимание будет уделяться тому, как его можно адаптировать и сделать более экологичным. Это выведет АБС в лидеры передовых материалов.
Переработка и воздействие на окружающую среду ABS-пластика
Переработка и охрана окружающей среды имеют большое значение, когда речь идет о пластике ABS. Когда срок службы изделий из ABS подходит к концу, их переработка становится жизненно важной. Технологии усовершенствовались, что позволило Переработка АБС лучше для окружающей среды.
Пластик ABS обозначается номером 7. В его состав входят стирол 50%, бутадиен 25% и акрилонитрил 25%. Эти компоненты делают АБС прочным, особенно на холоде, и идеальным для использования в автомобилях и электронике.2627.
Учет окончания срока службы изделий из ABS
Когда изделия из ABS перестают быть полезными, их воздействие на окружающую среду можно устранить с помощью правильной переработки. Хотя АБС имеет низкая температура плавления и может загореться, его можно перерабатывать без потери качества26. Переработка ABS имеет решающее значение для устойчивого повторного использования и снижает его воздействие на окружающую среду.
Экологически безопасные инициативы в переработке АБС
Во всем мире предпринимаются усилия по переработке ABS, чтобы уменьшить вред, наносимый окружающей среде. Такие организации, как Plastic Collectors, стремятся очистить окружающую среду, уделяя особое внимание таким пластикам, как ABS.26. Sulapac Luxe - еще один экологичный вариант, обладающий такими преимуществами, как биоразлагаемость и меньший углеродный след.27.
Экологические законы определяют способы использования и утилизации АБС. Франция намерена запретить одноразовую упаковку из стирольных полимеров к 2025 году. Это отражает переход к материалам, которые одновременно функциональны и лучше для планеты27.
Узнайте больше об устойчивой переработке и как это влияет на ABS.
Материал | Возможность вторичной переработки | Экологичные характеристики |
---|---|---|
ABS | Высокая степень переработки | Может подвергаться механической обработке |
Sulapac Luxe | Биоразлагаемые, до 70% переработанных биополимеров | Минимизирует опасность для окружающей среды |
Заключение
АБС-пластик отличается высокими эксплуатационными характеристиками во многих отраслях промышленности. Его способность выдерживать низкие температуры и сильные удары является ключевой2829. Это делает его идеальным для таких деталей автомобиля, как бамперы и приборные панели.2829. Он используется повсеместно, от электроники до автомобилей, что свидетельствует о его важнейшей роли в современном производстве.
ABS также отлично подходит для изделий, которым необходимо противостоять высоким температурам и нагрузкам. Он хорошо работает при температуре от -20°C до 80°C.29. Низкая теплопроводность делает его идеальным материалом для изоляции изделий28. Однако при 3D-печати и обработке на станках с ЧПУ могут возникать такие проблемы, как деформация и растрескивание.
Сегодня многие ставят перед собой задачу сделать ABS более пригодным для вторичной переработки. Он обладает низким водопоглощением и хорошей поверхностной твердостью30. Это повышает возможность его переработки и повторного использования. Прочные и термостойкие варианты вы можете найти на сайте Цзянтай машина. Этот выбор поддерживает эффективность и заботу об окружающей среде в производстве282930.