إجراء بعض التغييرات على البيئة العالمية
-
المبنى 3، مدينة وانيانغ للابتكار، شارع لانغشيا، مدينة يوياو، مقاطعة تشجيانغ
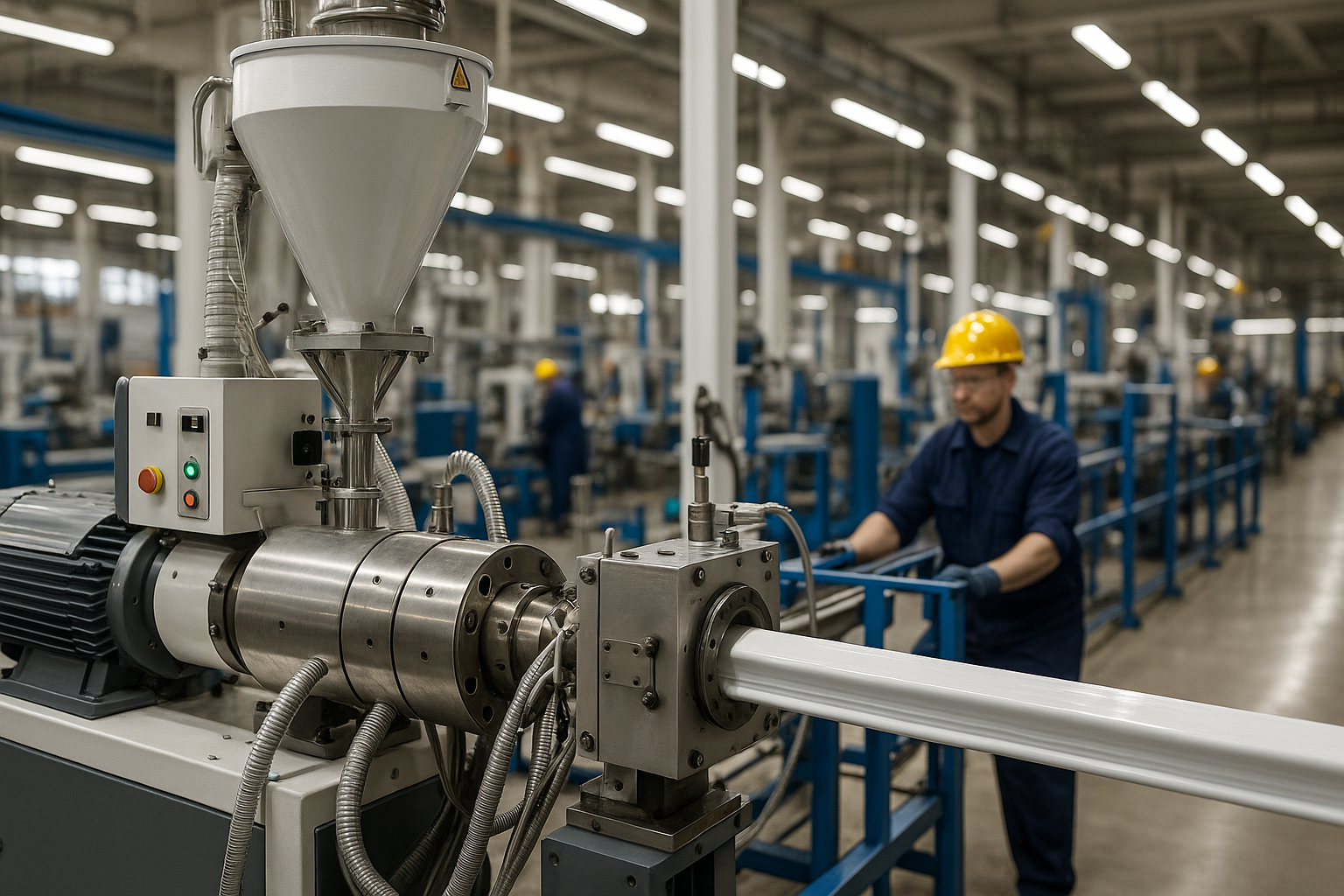
اصطفوا للنجاح مع اختيارات معدات بثق البلاستيك هذه
استكشف أفضل اختيارات معدات بثق البلاستيك لتحقيق الكفاءة والجودة. حسِّن عملية التصنيع لديك من خلال رؤى الخبراء.
## The Essential Guide to Plastic Extrusion Equipment
Plastic extrusion equipment forms the backbone of modern manufacturing processes that transform raw plastic materials into countless products we use daily. If you’re exploring extrusion equipment options, here’s what you need to know:
Type of Equipment | Primary Function | الأفضل لـ | Typical Applications |
---|---|---|---|
Single Screw Extruders | General processing of thermoplastics | High-volume, standard applications | Pipes, profiles, sheets |
Twin Screw Extruders | Improved mixing and compound processing | Complex materials, sensitive applications | Specialty profiles, compounding |
Co-extrusion Systems | Multi-layer product creation | Products requiring multiple materials | Multi-layer films, composite pipes |
Downstream Equipment | Post-extrusion processing | Finishing and preparing final products | Cooling, cutting, winding |
The plastic extrusion process transforms raw plastic pellets into continuous shapes by melting and forming the material through specialized dies. This technology dates back over 75 years, with industry innovators pioneering advancements that continue to shape the sector today.
For manufacturing managers focused on sustainability, modern extrusion equipment offers significant advantages. As one equipment provider notes: “Our extruders are designed to process up to 100% recycled plastics,” addressing both environmental concerns and production efficiency.
The right extrusion equipment selection can dramatically impact your production quality, efficiency, and environmental footprint. With innovations like energy-efficient drives and advanced control systems, today’s equipment can reduce energy consumption by 10-15% while improving output by 20-30%.
When evaluating plastic extrusion equipment, consider:
- Material compatibility with your specific polymers
- Production volume requirements
- Energy efficiency ratings
- Customization options
- Downstream integration capabilities
By selecting equipment that aligns with both your production goals and sustainability objectives, you can significantly reduce waste while optimizing your manufacturing processes.
1. Single Screw Plastic Extrusion Equipment: The Workhorse of Manufacturing
If the plastic manufacturing world had a reliable best friend, it would be the single screw extruder. These trusty machines aren’t just popular—they account for about 70% of all معدات بثق البلاستيك installations worldwide. And this isn’t by accident!
Think of single screw extruders as the patient workhorses that keep production lines moving day after day. Their beauty lies in simplicity: a rotating screw inside a heated barrel moves plastic material through a fascinating journey. Raw plastic pellets enter through the hopper, then travel along the barrel where they’re gradually melted by a combination of friction (from the screw’s mechanical action) and external heat. This molten plastic is then pushed through a specially designed die to create continuous profiles with consistent dimensions.
Here at جيان تاي Plastic Machinery Company, our E-GO Series Single Screw Extruders showcase exactly what manufacturers love about this technology. They handle common thermoplastics with remarkable efficiency—everything from polyethylene (PE) and polypropylene (PP) to polyvinyl chloride (PVC), polystyrene (PS), and acrylonitrile butadiene styrene (ABS).
What can you make with these machines? Almost anything! Walk through your home and you’ll find countless products born from single screw extrusion: pipes carrying your water, window frames, siding, packaging films, containers, and even automotive components. Their versatility is truly impressive.
Advantages of Single Screw Extruders
The enduring popularity of single screw معدات بثق البلاستيك comes down to several key benefits that matter to manufacturers of all sizes.
First, these machines are productivity champions. They can run continuously for incredibly long periods—sometimes 24/7 for weeks or even months between maintenance breaks. Larger models can produce up to 2000kg of finished product per hour, making them ideal for high-volume production needs.
Energy efficiency is another major advantage. Modern single screw extruders have come a long way, incorporating direct drive systems with sophisticated energy control. These smart innovations typically reduce energy consumption by 10-15% compared to older models—savings that add up significantly over time.
From a business perspective, the cost-effectiveness is hard to ignore. The relatively straightforward design means lower purchase prices, simpler operation, and more affordable maintenance compared to more complex systems. Your team won’t need extensive specialized training to operate them effectively, either.
Reliability is perhaps their most cherished quality. With fewer moving parts than twin screw systems, single screw extruders experience fewer mechanical issues and often enjoy impressively long service lives. It’s not uncommon to see these machines still performing beautifully after decades of service with proper care.
Once properly set up, they provide remarkable process stability. This means consistent product quality and minimal waste—music to the ears of any production manager focused on quality control.
As one of our engineers recently put it: “Single screw extruders are like that reliable family car that starts every morning without fail. They may not be the flashiest option, but they’ll get you where you need to go day after day, year after year.”
2. Twin Screw Extruders: Improved Mixing and Quality
When your production needs demand more than what single screw technology can deliver, twin screw extruders become your best allies. These remarkable machines represent the next evolution in معدات بثق البلاستيك, featuring two intermeshing screws that work together inside the barrel. This creates a fascinating flow pattern that dramatically improves mixing, compounding, and overall processing capabilities.
Here at JianTai Plastic Machinery Company, we’ve noticed something interesting – more and more customers are asking about our twin screw systems. It’s not surprising, really. These machines excel when precision matters and when you’re dealing with materials that would give standard extruders a headache. The twin screws create a self-wiping action that prevents material from getting stuck and degrading – absolutely crucial when you’re working with polymers that don’t like too much heat.
You’ll find twin screw extruders in two main flavors. Co-rotating twin screw extruders have both screws spinning in the same direction, creating excellent mixing and self-cleaning properties. These are the workhorses of compounding operations and technical polymer processing. Then there are the counter-rotating twin screw extruders, where the screws rotate in opposite directions. This creates strong shear forces and pressure control, making them perfect for PVC processing and applications where precise pressure matters.
Our MD Series of Twin Screw Extruders shows just how far this technology has come. With screw diameters ranging from a modest Φ20mm all the way up to an impressive Φ500mm, and lengths that can stretch up to 10000mm, we can tailor these machines precisely to what your production line needs.
When to Choose Twin Screw Plastic Extrusion Equipment
Wondering if a twin screw extruder is right for your operation? There are several scenarios where investing in twin screw plastic extrusion equipment makes perfect sense.
Processing sensitive materials is where these machines truly shine. Some polymers and additives just don’t handle prolonged heating well – they’ll degrade and cause all sorts of problems. Twin screw extruders offer more controlled residence time, meaning your material spends less time exposed to heat. Your heat-sensitive materials will thank you!
عندما يتعلق الأمر ب complex compounding, nothing beats a twin screw extruder. Need to thoroughly mix polymers with additives, fillers, reinforcements, or colorants? These machines ensure everything gets distributed evenly throughout your material. The result? Consistent product properties batch after batch.
For products with higher quality demands, twin screw extruders deliver superior results. Their improved mixing and degassing capabilities mean fewer defects and higher quality output. If you’re producing technical parts with strict requirements, this advantage alone can justify the investment.
Twin screw extruders also excel at reactive extrusion – processes where chemical reactions need to happen during extrusion. They provide the precise mixing and residence time control needed to make these reactions happen effectively.
In today’s sustainability-focused world, material recycling capabilities matter more than ever. Twin screw extruders handle recycled plastics beautifully, even when those materials contain contaminants or have varying compositions. As one of our customers who processes post-consumer waste puts it: “Our twin screw system handles variations in recycled material that would completely jam our old single screw setup.”
As Zhang Wei, our lead engineer with over two decades of experience customizing extrusion equipment, often tells customers: “Twin screw extruders give you precision control over every aspect of the extrusion process. When you’re working with challenging materials or need exceptional quality, they’re often worth the additional investment.”
3. Customizable Extrusion Lines for Specific Industry Needs
No two manufacturing operations face identical challenges—that’s why at JianTai Plastic Machinery Company, we’ve seen how معدات بثق البلاستيك must adapt to widely varying needs. Whether you’re producing delicate medical tubing or robust agricultural pipes, your production line needs to be as unique as your products.
The beauty of modern extrusion technology lies in its adaptability. Consider the manufacturer producing window frames in Michigan versus the one making irrigation pipes in Arizona—both use extrusion processes, but their equipment requirements couldn’t be more different. This diversity is why customization has become not just beneficial but essential.
With over 75 years in the industry, innovators have found that tailoring equipment to specific applications directly impacts both quality and output. When we customize a screw design for a particular polymer, we’re not just changing a component—we’re optimizing your entire production process. A perfectly matched screw geometry might improve your melting efficiency by 15-20% while reducing energy consumption and enhancing product consistency.
Barrel configurations represent another crucial customization point. For materials that release gases during processing, strategic degassing ports prevent bubble formation and product defects. Similarly, custom die designs ensure your final product achieves the exact dimensions and surface finish your customers expect.
Modern control systems add another layer of customization. Today’s smart extruders can be programmed with material-specific processing parameters that automatically adjust when conditions change, maintaining consistent quality even when facing variables like humidity or raw material variations.
For specialized applications like rigid PVC profiles used in construction, these customizations become even more critical. Our معدات بثق مقاطع البولي فينيل كلوريد الفينيل الصلبة incorporates specific features that address the unique challenges of processing PVC, including precise temperature control to prevent degradation and specialized cooling systems that minimize warping.
Key Components of Plastic Extrusion Equipment Lines
Behind every successful extrusion operation stands a harmonious system of components working together. Understanding how these elements interact helps you build the ideal system for your specific needs.
إن extruder serves as the heart of your line, where raw plastic transforms into a homogeneous melt. Its performance depends on factors like screw design, length-to-diameter ratio, and drive power. For abrasive materials, we might recommend wear-resistant barrel linings that extend equipment life from months to years.
Next comes the die head, which gives your product its shape. Die design is both science and art—getting it right means achieving perfect material flow while maintaining precise dimensions. A well-designed die reduces pressure requirements and improves surface finish, directly enhancing product quality.
إن نظام التبريد might seem straightforward, but it’s actually where many quality issues originate. Uneven cooling causes warping and dimensional inconsistencies. For thin-walled products, we often recommend multi-stage cooling that gradually reduces temperature, preventing internal stresses that lead to product failure.
Your sizing equipment ensures the product maintains correct dimensions as it cools. Vacuum calibration systems can be custom-designed for specific profiles, maintaining tight tolerances even for complex shapes.
إن puller draws extrudate from the die at precisely controlled rates. Modern pullers feature synchronization with the extruder, automatically adjusting to maintain dimensional consistency even when processing conditions fluctuate.
For finished products, cutters و take-off equipment complete your line. High-precision cutters deliver clean cuts at exact lengths, while specialized handling systems stack, coil, or package your products according to your specific requirements.
One industry specialist with over 20 years of customization experience explains it best: “A truly optimized extrusion line isn’t just a collection of components—it’s an integrated system where each element complements the others.” This holistic approach delivers the consistency manufacturers need batch after batch.
At JianTai, we’ve found that adjustable components make all the difference in meeting specific industry needs. Whether you’re processing virgin materials or recyclables, producing simple or complex shapes, a thoughtfully customized extrusion line transforms challenging materials into profitable products.
4. Advanced Downstream Equipment to Optimize the Extrusion Process
When we talk about plastic extrusion, it’s easy to focus all our attention on the extruder itself. However, at JianTai Plastic Machinery Company, we’ve learned through years of experience that what happens after the plastic leaves the die is just as crucial to your final product quality. This is where downstream equipment enters the picture – the unsung heroes of the extrusion process.
Think of downstream equipment as the supporting cast that ensures your star performer (the extruder) can truly shine. Without properly synchronized downstream components, even the most advanced extruder in the world would struggle to produce consistent, high-quality products.
The journey of your plastic product doesn’t end at the die – it’s just beginning. As the hot, malleable plastic emerges, it needs proper handling to become the finished product you envision. Cooling tanks and sizing equipment immediately take over, using carefully controlled water or air to solidify your product while maintaining precise dimensions. Our advanced tanks feature temperature control systems that can be adjusted to within 1°C, ensuring your products cool at the optimal rate.
Once cooled and sized, your product moves to the belt pullers – perhaps the most critical synchronization point in the entire line. These devices maintain the perfect tension and speed, with modern digital controls achieving accuracy within ±0.1%. As one of our customers recently told us, “The consistency we get from JianTai’s pullers has reduced our dimensional variation by nearly 50%.”
For products that need to be cut to specific lengths, our servo-driven cutters deliver impressive precision at speeds ranging from 200 to 1,000 cuts per minute. We’ve designed our cutting systems with quick blade-change features that can reduce changeover time from hours to minutes – a small detail that makes a big difference in your production schedule.
Some applications benefit from combination puller/cutter units that save valuable floor space while improving synchronization. These integrated systems are particularly valuable for smaller facilities or when working with challenging materials that require precise tension control during cutting.
For flexible products like tubing or cables, our coiling machines automatically wind your product onto reels with consistent tension – a task that would be virtually impossible to achieve manually with any consistency. And at the end of the line, take-away conveyors and dump tables ensure your finished products are handled gently and efficiently.
Enhancing Efficiency with Downstream Equipment
The right downstream equipment doesn’t just improve product quality – it transforms your entire operation. When we work with clients to optimize their معدات بثق البلاستيك, we focus on several key benefits:
Improved quality comes from precision at every step. When your cooling is consistent and your cuts are clean, your products simply look and perform better. One of our customers in the medical tubing industry reported that after upgrading their downstream equipment, their tolerance compliance improved from 92% to 99.2% – a difference that matters tremendously in critical applications.
Productivity gains often surprise our clients. By eliminating bottlenecks in the downstream process, your entire line can operate at its optimal speed. Modern automated handling systems reduce labor requirements while increasing throughput – sometimes by as much as 30-40% compared to older systems.
Energy efficiency has become increasingly important, and modern downstream equipment addresses this need. Variable frequency drives, insulated cooling tanks, and optimized motor sizing can reduce energy consumption by 10-15% compared to previous generation equipment. These savings add up quickly, often paying for the equipment upgrades within just a few years.
إن المرونة of today’s downstream equipment is remarkable. Digital controls and quick-change features allow you to switch products in minutes rather than hours. This means you can profitably run smaller batches and respond quickly to customer demands – a competitive advantage in today’s market.
Perhaps most importantly, well-designed downstream equipment dramatically reduces waste. Precise control systems minimize start-up scrap and maintain consistent quality throughout production runs. In an era of rising material costs and environmental consciousness, this benefit alone can justify investing in quality downstream equipment.
Integration is the key to making all these components work together seamlessly. Modern extrusion lines feature centralized control systems that synchronize every component, automatically adjusting speeds and parameters to maintain optimal production conditions. When your extruder speeds up, every downstream component responds in perfect harmony – maintaining product quality and reducing waste.
As we often tell our customers at JianTai: “An extrusion line is only as strong as its weakest component.” By investing in quality downstream equipment that matches your extruder’s capabilities, you’re ensuring that every part of your production process contributes to your success. The result? Better products, happier customers, and a healthier bottom line.
5. The Latest Technological Advancements in Plastic Extrusion Machinery
Walk through any modern plastic manufacturing facility today, and you’ll find it’s a far cry from the factories of even a decade ago. The world of معدات بثق البلاستيك has transformed dramatically, with innovations that make yesterday’s machinery look like relics from another era.
At JianTai Plastic Machinery Company, we’ve witnessed this evolution firsthand, staying at the cutting edge to ensure our customers benefit from every technological leap forward. These advancements aren’t just impressive on paper – they’re changing the economics and environmental impact of plastic manufacturing in profound ways.
Take energy efficiency, for instance. Modern extruders now incorporate direct drive systems that eliminate traditional gearboxes entirely. This seemingly simple change reduces energy losses, cuts maintenance headaches, and can slash energy consumption by 10-15%. For a 24/7 operation, those savings add up quickly on both your utility bills and carbon footprint.
The materials you can process have expanded dramatically too. New screw and barrel designs have open uped the ability to work with everything from high-temperature engineering polymers to the latest bioplastics. Most exciting for sustainability-minded manufacturers is the ability to process up to 100% recycled materials – including PET-flakes and rHDPE – without sacrificing quality or efficiency.
“Five years ago, running high percentages of recycled content meant accepting significant production slowdowns,” explains one of our senior engineers. “Today’s equipment has completely changed that equation. You can be green and profitable at the same time.”
The brains behind these machines have gotten remarkably smarter as well. Modern control systems don’t just monitor your process – they actively anticipate and prevent problems before they affect your product. Real-time adjustments happen automatically, maintaining perfect consistency even when input materials vary. Some systems even incorporate artificial intelligence to continuously optimize your process parameters, finding efficiencies human operators might miss.
Maintenance has become simpler too, thanks to modular designs that allow quick component swaps. When a part needs replacement or you want to configure for a different application, downtime is minimized. This modularity also means your investment is more future-proof, as individual components can be upgraded as technology advances.
Innovations Shaping the Future of the Extrusion Industry
The true game-changers in the industry go beyond incremental improvements to fundamentally reshape how extrusion lines operate and integrate with the broader manufacturing ecosystem.
Automation and Industry 4.0 integration has perhaps the most visible impact on daily operations. Modern lines handle everything from material feeding to final packaging with minimal human intervention. More importantly, they communicate seamlessly with your factory management systems, providing real-time data on production rates, quality metrics, and resource utilization. This connectivity transforms how you manage your operation, enabling data-driven decisions that boost both quality and efficiency.
إن user interfaces of today’s equipment would be unrecognizable to operators from previous generations. Intuitive touchscreens with clear graphics have replaced complicated control panels, reducing training time and operator errors. Even more is the ability to monitor and adjust your production line remotely. When issues arise, experts can troubleshoot from anywhere in the world, often resolving problems without ever setting foot in your facility.
On the sustainability front, innovations continue at a rapid pace. Energy recovery systems now capture and repurpose heat that would previously have been wasted. Variable frequency drives adjust motor speeds to match actual production needs rather than running at full power continuously. Some manufacturers are even incorporating induction heating systems that provide more precise temperature control while further reducing energy consumption.
Perhaps most exciting is the equipment specifically designed for the الاقتصاد الدائري. Advanced filtration systems can now remove contaminants from recycled materials that would previously have rendered them unusable. Co-extrusion technology allows strategic use of recycled content in non-critical layers, maximizing resource utilization while maintaining product performance.
“The extrusion industry is undergoing a technological revolution,” notes a veteran with over 20 years in the field. “Today’s equipment not only produces higher quality products more efficiently but also addresses critical sustainability challenges by enabling the effective processing of recycled materials.”
At JianTai Plastic Machinery Company, we don’t just follow these trends – we help create them. Our commitment to technological advancement ensures our customers stay ahead in an increasingly competitive and environmentally conscious marketplace. By incorporating these innovations into our equipment designs, we provide solutions that address both immediate production needs and long-term sustainability goals.
For more information on how these technological advancements are being implemented in the industry, you can visit the Plastics Technology resource center, which provides in-depth coverage of extrusion innovations.
The plastic extrusion equipment of today bears little resemblance to its predecessors, and tomorrow’s innovations promise even greater advances. For manufacturers looking to remain competitive, understanding and embracing these technological developments isn’t just advantageous – it’s essential.
Frequently Asked Questions about Plastic Extrusion Equipment
What Materials Can Be Used in Plastic Extrusion?
When manufacturers approach us at JianTai Plastic Machinery Company about معدات بثق البلاستيك, one of their first questions is often about material compatibility. The beauty of plastic extrusion is its versatility across a wide range of thermoplastics, though each material brings its own unique processing requirements.
البولي إيثيلين (PE) remains one of the most commonly processed materials in our extruders. Available in different densities like LDPE, HDPE, and LLDPE, polyethylene is wonderfully forgiving during processing. It flows nicely at relatively low temperatures between 160-240°C, making it perfect for everything from water pipes to shopping bags.
البولي بروبلين (PP) requires a bit more attention during processing. With its narrower processing window (typically 200-270°C), it demands more precise temperature control. However, the extra care pays off in the form of durable automotive components, robust packaging, and even textiles with excellent chemical resistance.
Many of our customers work extensively with كلوريد البوليفينيل المتعدد الفينيل (PVC), particularly in construction applications. PVC can be a bit temperamental – process it too hot and it’ll degrade, potentially releasing corrosive byproducts. We typically recommend specialized barrel materials and careful temperature control in the 160-200°C range to keep PVC happy during extrusion.
For packaging and consumer products, البوليسترين (PS) offers excellent clarity and rigidity. Processing between 180-280°C, it requires good temperature control to prevent degradation that can affect both appearance and properties.
When impact resistance and tough surface finish matter, أكريلونيتريل بوتادين ستايرين (ABS) shines. This engineering plastic processes at 200-260°C and has become a staple in automotive components and consumer electronics.
بولي إيثيلين تيريفثالات البولي إيثيلين (PET) presents unique challenges that our more advanced extruders are designed to handle. Used primarily for bottles and fibers, PET absolutely must be thoroughly dried before processing to prevent hydrolytic degradation. Its higher processing temperatures (260-300°C) and sensitivity to moisture make specialized equipment a wise investment.
We’re seeing growing interest in البلاستيك القابل للتحلل الحيوي like PLA, PBAT, and PBS. These materials often require specific processing conditions and screw designs, but the environmental benefits make the extra consideration worthwhile.
Perhaps most exciting is the increasing focus on recycled plastics. While these materials present challenges due to potential contamination and variable properties, our advanced filtration systems and robust screw designs help manufacturers successfully incorporate recycled content into their products.
As one of our engineers likes to say, “The secret to successful extrusion isn’t just having good equipment – it’s having the right equipment for your specific material. What works beautifully for polyethylene might be completely wrong for PET.”
How Does the Choice of Extrusion Equipment Affect Product Quality?
The selection of معدات بثق البلاستيك influences nearly every aspect of your final product quality. This relationship between equipment and output quality is something we take very seriously at JianTai.
Dimensional accuracy stands as perhaps the most obvious quality factor. The precision of your extruder, die, and downstream equipment directly determines whether your products meet specification. We’ve seen manufacturers struggle with inconsistent wall thickness in pipes or irregular profiles simply because their equipment lacked the necessary control systems to maintain consistent output rates and temperatures.
Your product’s surface finish tells the story of your extrusion process. A properly designed die with even flow paths produces smooth, consistent surfaces, while issues like shark skin or orange peel textures often signal temperature control problems. Even your cooling method matters – too fast and you’ll see stress marks, too uneven and warping becomes inevitable.
Less visible but equally important are the mechanical properties of your extruded products. The processing conditions created by your equipment directly influence molecular orientation and crystallinity within the polymer. This microscopic structure determines strength, flexibility, and impact resistance. Consistent processing ensures uniform properties throughout your product – something particularly critical for applications where failure isn’t an option.
For transparent products, equipment quality becomes immediately apparent. Proper optical properties depend on consistent melting, contamination-free processing, and appropriate cooling – all factors determined by your extrusion line design.
Many manufacturers overlook how equipment choice affects long-term performance. Processing conditions can significantly impact environmental stress crack resistance, UV stability, and aging characteristics. Proper degassing capabilities remove volatile components that might otherwise cause bubbles or voids that compromise performance over time.
Perhaps most valuable to production managers is the batch-to-batch consistency that comes with advanced equipment. Modern control systems ensure processing conditions remain stable over time, resulting in uniform quality across production runs. This consistency is particularly crucial for critical applications in medical, automotive, or construction sectors where specifications leave little room for variation.
“The quality of your final product directly reflects the quality of your extrusion equipment,” notes one of our customers with over two decades in profile extrusion. “Investing in the right equipment pays for itself many times over through reduced scrap, fewer customer complaints, and a stronger reputation for quality.”
What Are the Maintenance Considerations for Extrusion Equipment?
Proper maintenance is the unsung hero of successful plastic extrusion operations. At JianTai Plastic Machinery Company, we emphasize that even the best معدات بثق البلاستيك requires thoughtful, regular care to deliver consistent performance and longevity.
Regular cleaning forms the foundation of any maintenance program. Over time, polymer residue can degrade, leading to contamination and potential equipment damage. We recommend cleaning screw and barrel assemblies during material or color changes and at scheduled intervals. Many of our customers have found that specialized purging compounds make this process significantly more efficient than manual cleaning methods.
Wear monitoring helps catch problems before they affect your product quality. Critical components like screws, barrels, and dies naturally experience wear over time, especially when processing abrasive materials. Regular inspection and measurement help identify when replacement becomes necessary. Some of our more advanced equipment includes automated wear monitoring to simplify this process.
Your temperature control systems deserve particular attention. Heating elements, thermocouples, and cooling systems require regular inspection and calibration to ensure accurate temperature control. A single failed heating zone can cause processing issues and product defects that might not be immediately obvious but will certainly impact quality.
إن drive system powers your entire operation, making its maintenance critical. Gearboxes, motors, and bearings need regular lubrication and inspection. Many of our customers have found that vibration analysis can detect potential failures before they occur, preventing costly emergency shutdowns. Our modern direct drive systems typically require less maintenance than traditional gearbox drives, which is why they’ve become increasingly popular.
Don’t overlook your electrical systems during maintenance rounds. Control panels, sensors, and wiring should be inspected regularly for signs of wear or damage. We recommend backup systems for critical controls to prevent extended downtime if primary systems fail.
Hydraulic and pneumatic components used in screen changers, die adjusters, and other components require regular fluid changes, filter replacements, and seal inspections. These systems often operate under significant pressure, making preventive maintenance particularly important for safety as well as performance.
Your downstream equipment needs just as much attention as the extruder itself. Pullers, cutters, and handling systems require alignment checks, lubrication, and wear monitoring to maintain proper operation and synchronization with the extruder. A perfectly functioning extruder can’t deliver quality products if the downstream equipment isn’t properly maintained.
“Preventive maintenance is always less expensive than reactive maintenance,” as our service manager often reminds customers. “A well-maintained extruder not only lasts longer but also produces more consistent, higher quality products with less scrap and downtime.”
At JianTai, we provide comprehensive maintenance training and support to ensure our customers achieve maximum equipment life and performance. Our service team is always available to assist with both routine maintenance questions and emergency support when needed, helping you keep your production running smoothly year after year.
الخاتمة
اختيار المناسب معدات بثق البلاستيك is much like selecting the perfect tool for a craftsman – it can make all the difference between merely acceptable results and truly outstanding production. Throughout our journey exploring extrusion technology, we’ve seen how various systems serve different needs, from the reliable single screw workhorses that handle most everyday production to the sophisticated twin screw systems that tackle complex materials with precision.
What becomes clear is that success in plastic extrusion isn’t just about buying machinery – it’s about creating a harmonious production ecosystem where each component complements the others. Your extruder might be top-of-the-line, but without properly matched downstream equipment, you might as well be driving a sports car on square wheels!
Modern extrusion technology has evolved tremendously in recent years. Today’s systems aren’t just more productive – they’re smarter, more energy-efficient, and increasingly capable of handling recycled materials. This evolution comes at the perfect time as manufacturers face growing pressure to reduce environmental footprints while maintaining competitive pricing and quality.
Think of your extrusion equipment as a long-term partner in your manufacturing journey. The right partner adapts to your changing needs, works reliably day after day, and helps you achieve goals you might have thought impossible. This perspective helps when weighing factors like initial cost against long-term performance, energy efficiency, and maintenance requirements.
At JianTai Plastic Machinery Company, we’ve watched manufacturers transform their operations with properly selected equipment. Located in Yuyao City, Zhejiang Province, our team specializes in developing advanced معدات بثق البلاستيك that balances production demands with environmental responsibility. We’ve seen how the right machinery can turn waste plastics into valuable raw materials, supporting both sustainability initiatives and bottom-line results.
The extrusion landscape will continue evolving, with tomorrow’s equipment likely offering even greater precision, energy efficiency, and material flexibility. By choosing equipment with an eye toward future adaptability, you position your operation to evolve alongside industry demands rather than struggling to catch up.
Even the finest equipment requires proper care. A comprehensive maintenance program isn’t just about preventing breakdowns – it ensures consistent quality, maximizes efficiency, and extends the useful life of your investment. The small time investment in regular maintenance pays enormous dividends in reduced downtime and consistent production.
Whether you’re establishing a new production line or upgrading existing equipment, our team at JianTai is ready to help steer the complex world of extrusion technology. We understand that each manufacturing operation has unique requirements, and we pride ourselves on finding solutions that precisely match those needs rather than forcing one-size-fits-all approaches.
The future belongs to manufacturers who balance productivity with sustainability – creating quality products efficiently while minimizing environmental impact. With the right معدات بثق البلاستيك, you’ll not only produce better products more efficiently today but contribute to a more sustainable plastics industry for tomorrow.
To explore how our advanced plastic extrusion solutions might benefit your specific operations, check out our resource on ماكينة بثق البلاستيك: إعادة التدوير بدقة or reach out to our team for personalized guidance.